Why is Heat Management Crucial in the Electroplating Process?
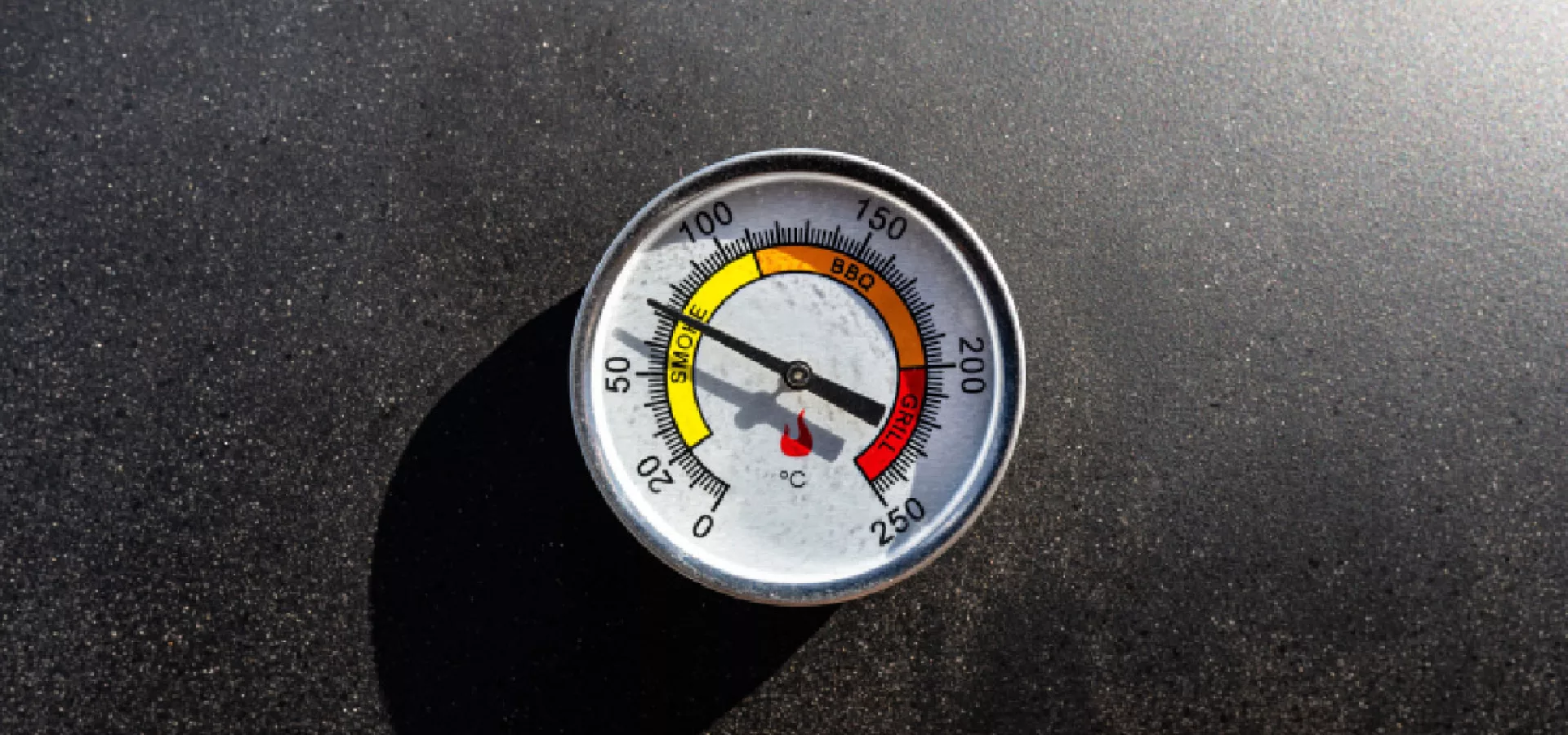
November 04, 2024
November 04, 2024
Electroplating, a process that involves depositing a layer of metal onto a substrate through an electrochemical reaction, is widely used across various industries for applications ranging from enhancing corrosion resistance to improving aesthetic appeal.
However, the success of this process heavily relies on precise temperature control. This blog post will delve into why heat management is crucial in the electroplating process, examining its impact on chemical reactions, deposition rates, and the properties of both the substrate and the plating layer.
The Role of Temperature in Electroplating
Influence on Chemical Reactions and Solution Conductivity
Temperature plays a critical role in the electroplating process by affecting the chemical reactions that occur within the plating bath. The rate of these reactions is temperature-dependent, meaning that any deviation from the optimal temperature can lead to undesirable outcomes.
For instance, at elevated temperatures, the rate of metal ion reduction increases, which can enhance the deposition rate but also lead to issues such as increased oxidation and reduced plating efficiency if not properly controlled.
Moreover, the conductivity of the plating solution is influenced by temperature. Higher temperatures generally improve solution conductivity, facilitating better current distribution across the substrate. This can lead to more uniform plating, which is crucial for achieving high-quality coatings.
Direct Impact on Metal Deposition Rate
The temperature of the plating solution directly affects the rate of metal deposition. As temperature increases, the kinetic energy of the particles in the solution also increases, leading to a higher rate of deposition.
This can be advantageous in reducing the time required for the electroplating process. However, it is essential to maintain a balance, as excessively high temperatures can destabilize the plating bath, resulting in poor quality deposits and inefficient plating.
Methods for Controlling Plating Bath Temperature
Effective temperature management in electroplating involves the use of advanced temperature control systems, agitation, and continuous monitoring of the bath temperature. These methods ensure that the plating bath remains within the desired temperature range, optimizing the deposition process and minimizing the risk of defects.
Temperature Control Systems
Temperature control systems are integral to maintaining the stability of the plating bath. These systems can automatically adjust the temperature to compensate for any fluctuations, ensuring consistent plating conditions. By employing precise temperature control, manufacturers can achieve the desired electrodeposition results, reduce the risk of corrosion, and minimize energy consumption.
Plating bath heaters and chillers are critical components of temperature control systems, maintaining the optimal temperature for consistent plating quality. Heaters are used to raise the bath temperature, accelerating reaction rates and improving plating speed, while chillers prevent overheating, which can lead to undesirable outcomes such as burning or dull deposits.
Agitation and Monitoring
Agitation of the plating bath helps in maintaining uniform temperature distribution throughout the solution. It prevents localized overheating or cooling, which can lead to uneven plating. Continuous monitoring of the bath temperature is also crucial, as it allows for real-time adjustments to be made, ensuring optimal plating conditions are maintained at all times.
Heat Treatments and Their Impact on the Plated Layer
Heat treatments, both during and after electroplating, significantly influence the microstructure of the plated layer. These treatments can enhance the mechanical properties of the coating, improve adhesion, and relieve stresses introduced during the plating process.
Microstructure and Coating Quality
Heat treatments can alter the grain structure of the plated layer, which in turn affects its mechanical properties. For instance, controlled heat treatments can improve wear resistance and fatigue life by refining the grain structure. However, if not properly managed, heat treatments can lead to unwanted grain growth, reducing the strength and increasing the brittleness of the coating.
Influence on Other Properties
In addition to microstructure, heat treatments can impact other properties such as uniformity, internal stress, ductility, and adhesion between the plating layer and the substrate. Properly executed heat treatments can enhance these properties, leading to improved performance and longevity of the plated components. Conversely, improper heat treatment parameters can result in poor adhesion, increased brittleness, and a propensity for early failure.
Conclusion
In conclusion, heat management is a critical aspect of the electroplating process, influencing everything from chemical reactions and deposition rates to the microstructure and properties of the plated layer. By employing precise temperature control systems, continuous monitoring, and appropriate heat treatments, manufacturers can optimize the electroplating process, ensuring high-quality coatings that meet specific performance criteria.
Discover PAVCO's advanced electroplating solutions to take your operations to the next level. We offer a range of products designed to enhance the efficiency and quality of your plating process.
IT’S HOW YOU FINISH
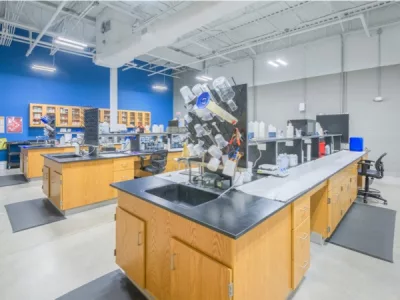
We’re a developer and supplier of chemistries for the metal finishing industry since 1948.
In PAVCO, we develop products and deliver services of the highest quality at a reasonable cost.