The Impact of Deposition Rate on Chloride vs. Sulfate-Based Trichrome Processes
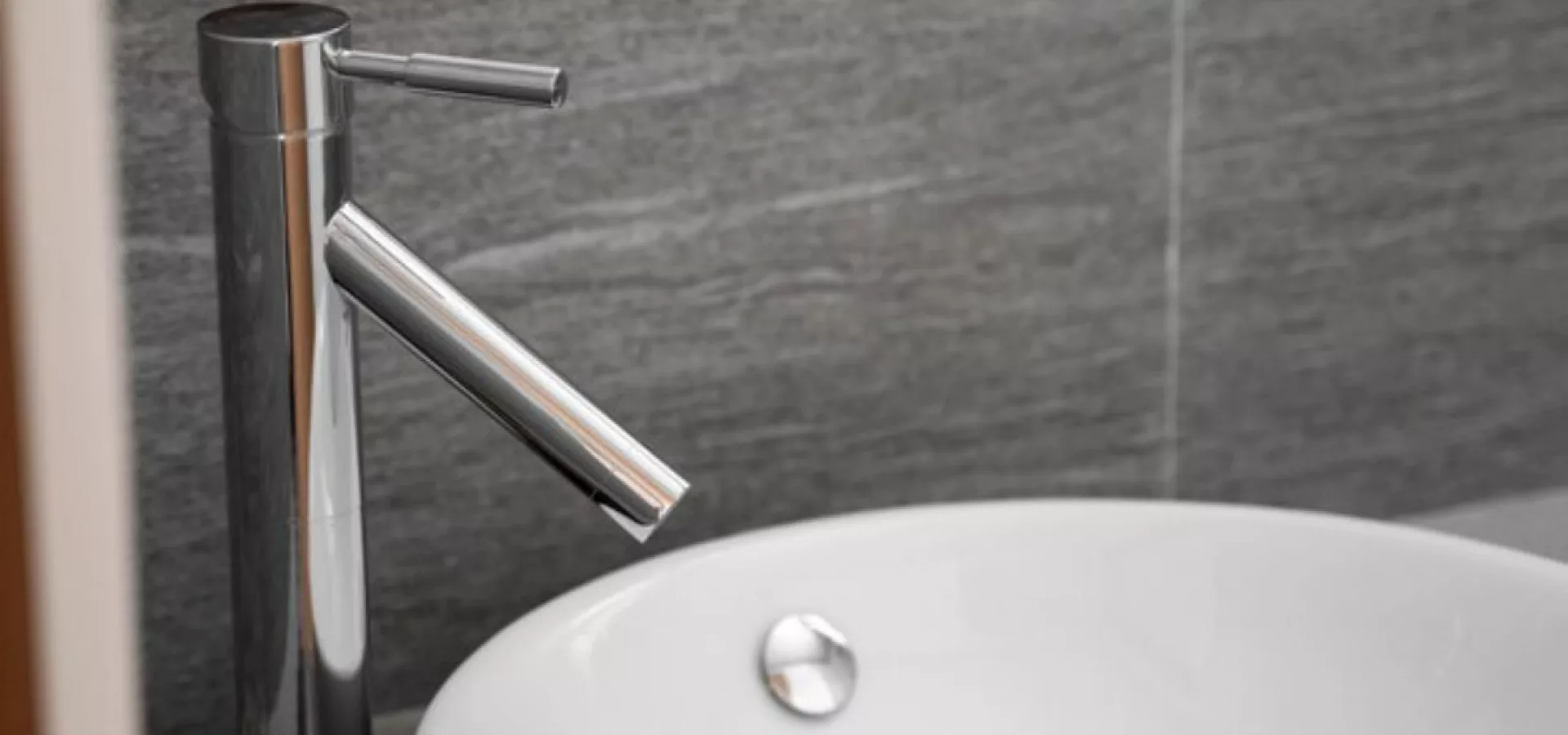
October 08, 2024
October 08, 2024
In electroplating, the deposition rate is crucial for determining the efficiency, quality, and overall success of the final product. This is especially relevant in trivalent chromium plating processes, which typically use either chloride or sulfate ions in the solution. The choice between these two systems directly affects the deposition rate, plating thickness, uniformity, appearance, and overall coating quality.
Chloride-Based Trivalent Chromium Processes
Chloride-based trivalent chromium processes are known for their high deposition rates, enabling thicker coatings in less time. This speed benefits electroplating lines where time is limited. Examples include existing plating lines using hexavalent chromium and a set plating cycle. Return type machines are prime examples of this limitation, as more plating time usually means a longer plating tank. This consideration is a big factor favoring chloride chemistry.
Nonetheless, chloride based processes tend to produce a slightly darker and yellower deposit compared to sulfate based processes.
Sulfate-Based Trivalent Chromium Processes
Sulfate-based processes have slower deposition rates when the primary objective is to achieve a deposit color that is as close to the hexavalent deposit as possible. Sulfate systems can also increase their speed by increasing the Chromium salt concentration in the plating bath. Higher Cr metal reduces low current density covering and throwing power so it is important to balance these two attributes.
Influence of Deposition Rate on Plating Quality
The deposition rate is a critical parameter that directly impacts the final quality of trivalent chromium coatings. For chloride-based systems, deposition rates typically range from 0.1 to 0.25 microns per minute, allowing for faster buildup of the coating layer. On the other hand, sulfate-based systems feature deposition rates between 0.04 and 0.08 microns per minute.
Deposition Rate in Trivalent Chromium Plating
The deposition rate in trivalent chromium plating plays a pivotal role in determining both the efficiency and the quality of the process. The difference between chloride and sulfate-based systems is most noticeable in how the deposition rate affects the coating's thickness, uniformity, and overall quality.
Our solutions are engineered to enhance both quality and consistency, providing reliability in applications that demand precision.
Impact on Coating Thickness and Uniformity
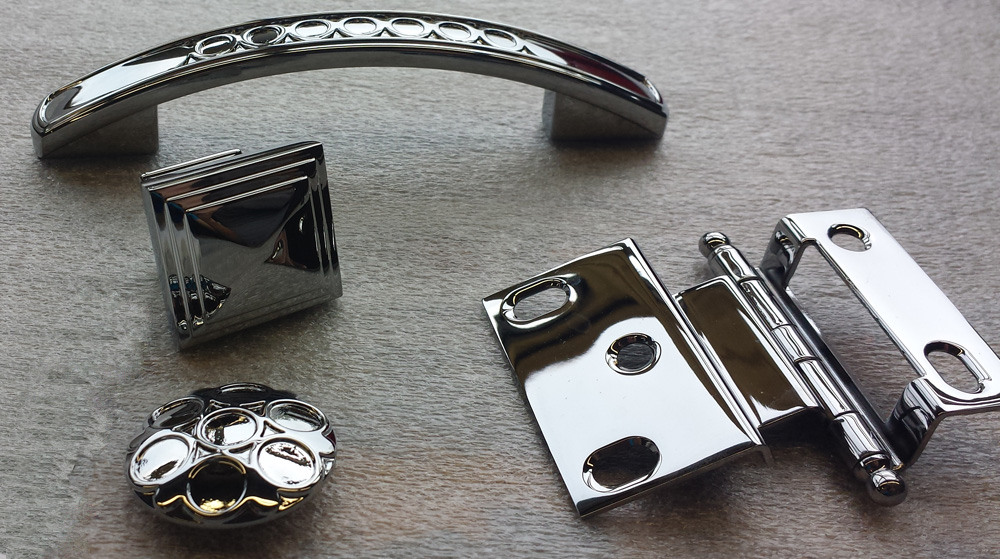
Operational and Application-Specific Considerations
When choosing between chloride and sulfate-based systems, industries must carefully weigh factors such as operational costs, time, efficiency, and the required finish quality. For high-volume production, chloride-based systems are often preferred due to their faster deposition rates. However, industries focused on color that is as close to Cr VI as possible, may opt for sulfate-based systems, despite their slower processing times.
Operational Implications of Deposition Rate
The choice between chloride and sulfate-based systems also has significant operational implications. The faster deposition rates of chloride systems mean that the desired coating thickness can be achieved in less time, reducing operational costs and increasing throughput. This makes chloride systems particularly attractive in high-volume production environments where efficiency is key.
However, the rapid deposition rate of chloride systems may require additional measures, such as adjusting current density or using additives or fixtures to further control the plating environment. Conversely, sulfate systems, with their slower deposition rates, may require additional equipment or modifications, such as larger tanks or more plating stations, to accommodate the longer processing time. Although this increases setup costs, the improved quality and uniformity of the final product can offset these expenses in the long term.
Environmental and Safety Considerations
Both chloride and sulfate-based trivalent chromium systems offer significant environmental and safety benefits over traditional hexavalent chromium plating. Trivalent systems are less toxic and pose fewer health risks to workers, making them a more sustainable choice for many applications.
Why is PAVCO your ideal partner?
In summary, choosing between chloride and sulfate-based trivalent chromium plating systems depends largely on the specific requirements of your application. While chloride-based systems offer speed and efficiency, sulfate-based processes provide superior control, uniformity, and finish quality. Each method has its strengths, but finding the right balance of speed, cost, and quality is critical to ensuring optimal results.
This is where Pavco excels. With decades of expertise in electroplating solutions, we offer tailored chemistries that address both the rapid deposition needs of chloride-based systems and the precision and consistency required by sulfate-based processes. Since Pavco offers both systems, we can assist you with choosing the right one for your application.
Explore our solutions and learn how to optimize your plating process.
IT’S HOW YOU FINISH
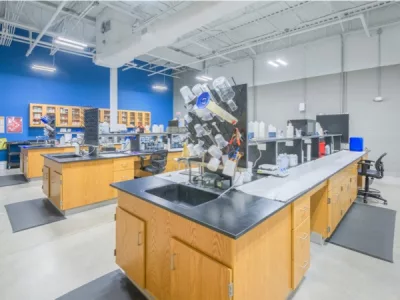
We’re a developer and supplier of chemistries for the metal finishing industry since 1948.
In PAVCO, we develop products and deliver services of the highest quality at a reasonable cost.