Power Supply for Plating: The Critical Role of Rectifiers
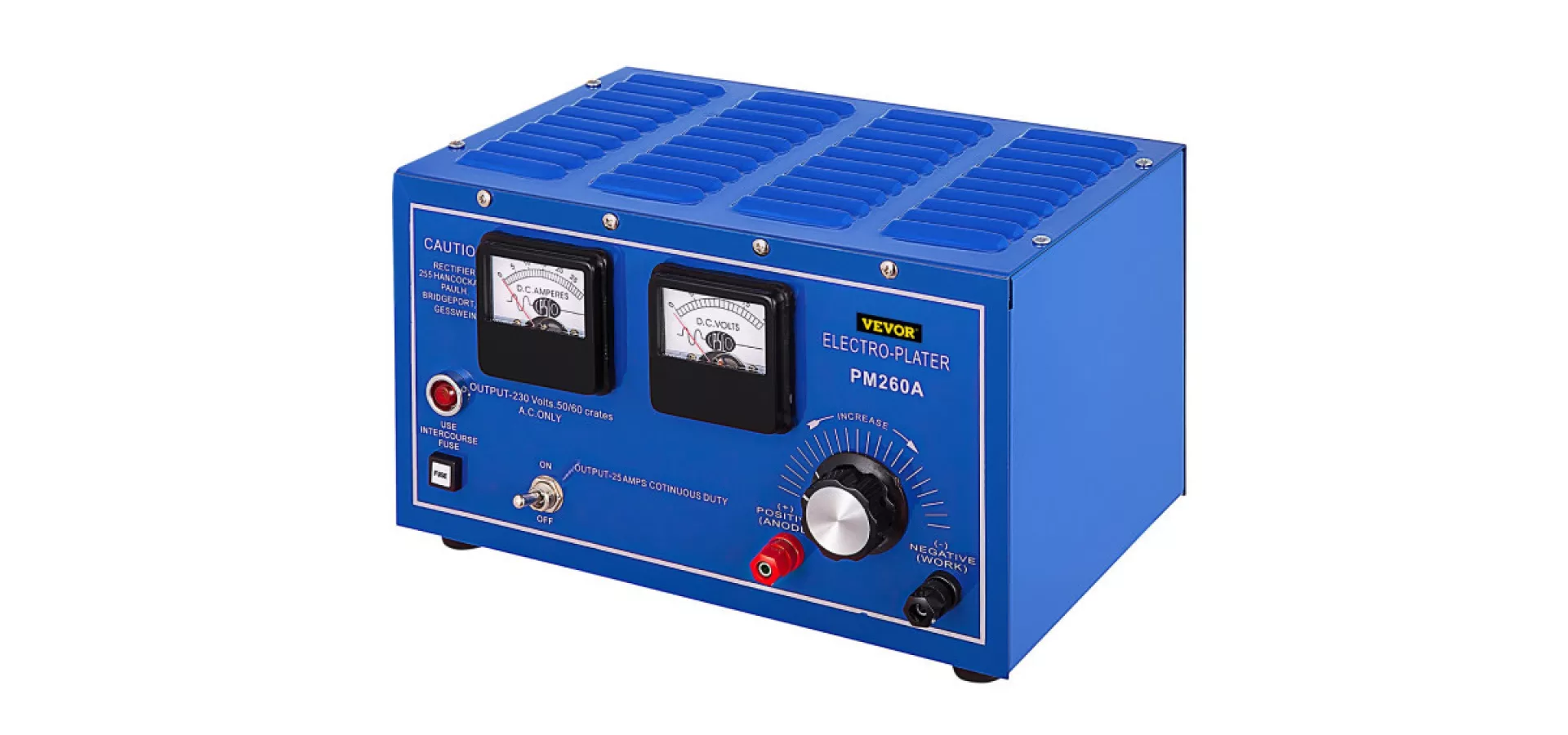
January 06, 2025
January 06, 2025
In the intricate world of electroplating, where precision and quality are paramount, rectifiers play a critical role. As industries demand higher standards and efficiency, understanding the role of rectifiers in the plating process becomes essential.
This blog explores the importance of rectifiers, their functions, and advanced features, shedding light on their impact on plating applications.
Understanding the Basics: AC vs. DC
Before diving into the role of rectifiers, it's essential to understand the difference between AC and DC. AC is the type of electricity supplied by utility companies; it flows in alternating directions, similar to ocean waves. DC, in contrast, flows in a single direction, much like water through a garden hose. In electroplating, DC is critical because it provides a stable and controlled flow of electrons, ensuring an even deposition of metal onto surfaces.
How Rectifiers Work: Simplified
Imagine trying to paint a wall with a brush that keeps changing direction unpredictably—that's what using AC directly in plating would feel like. Rectifiers act like a skilled painter, converting the unpredictable AC into a steady, consistent DC flow. This ensures a uniform layer of metal is deposited on the surface, avoiding issues like uneven distribution, poor adhesion, or inconsistent thickness.
Ensuring Stability and Uniformity
A high-quality rectifier is designed to minimize the "ripple" effect, a periodic variation in current that occurs when AC is converted to DC. Ripple can lead to irregularities in plating thickness, pits, or a lackluster finish. Modern rectifiers use advanced filtering and smoothing technologies to reduce ripple. Think of it like a water filtration system that removes impurities, leaving behind a clean, consistent flow.
Advanced Features: More than Just Pulse Plating
While pulse plating—delivering current in short bursts to improve throwing power and adhesion—is a standout advanced feature, modern rectifiers also offer digital interfaces, programmable settings, and energy-efficient modes. For example:
Silicon-Controlled Rectifiers (SCRs): Known for their robustness and ability to handle high power, these rectifiers are ideal for applications requiring stable, high-output DC.
IGBT Switch Mode Rectifiers: These are more efficient and responsive, making them perfect for precision plating applications. They reduce power consumption and allow for precise programming.
Elevate Your Plating Processes with PAVCO
While rectifiers are critical for electroplating, achieving consistent, high-quality results requires a synergy of advanced equipment and chemistry. Since 1948, PAVCO has been a trusted partner in the metal finishing industry, offering a comprehensive range of solutions for preplating, plating, and post plating processes.
Why Choose PAVCO?
Comprehensive Solutions: From surface preparation to innovative plating chemistries, PAVCO supports every stage of your process.
Expert Guidance: With decades of experience, our team provides personalized advice to optimize your operations.
Sustainability Commitment: Our eco-friendly solutions, including cobalt-free systems, align with modern environmental standards.
IT’S HOW YOU FINISH
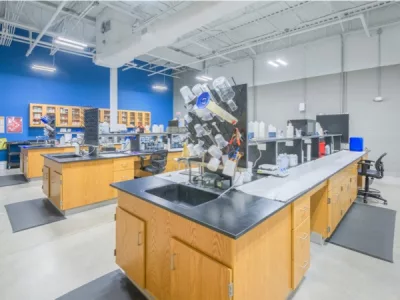
We’re a developer and supplier of chemistries for the metal finishing industry since 1948.
In PAVCO, we develop products and deliver services of the highest quality at a reasonable cost.