Finishing Technologies: Extracting Performance
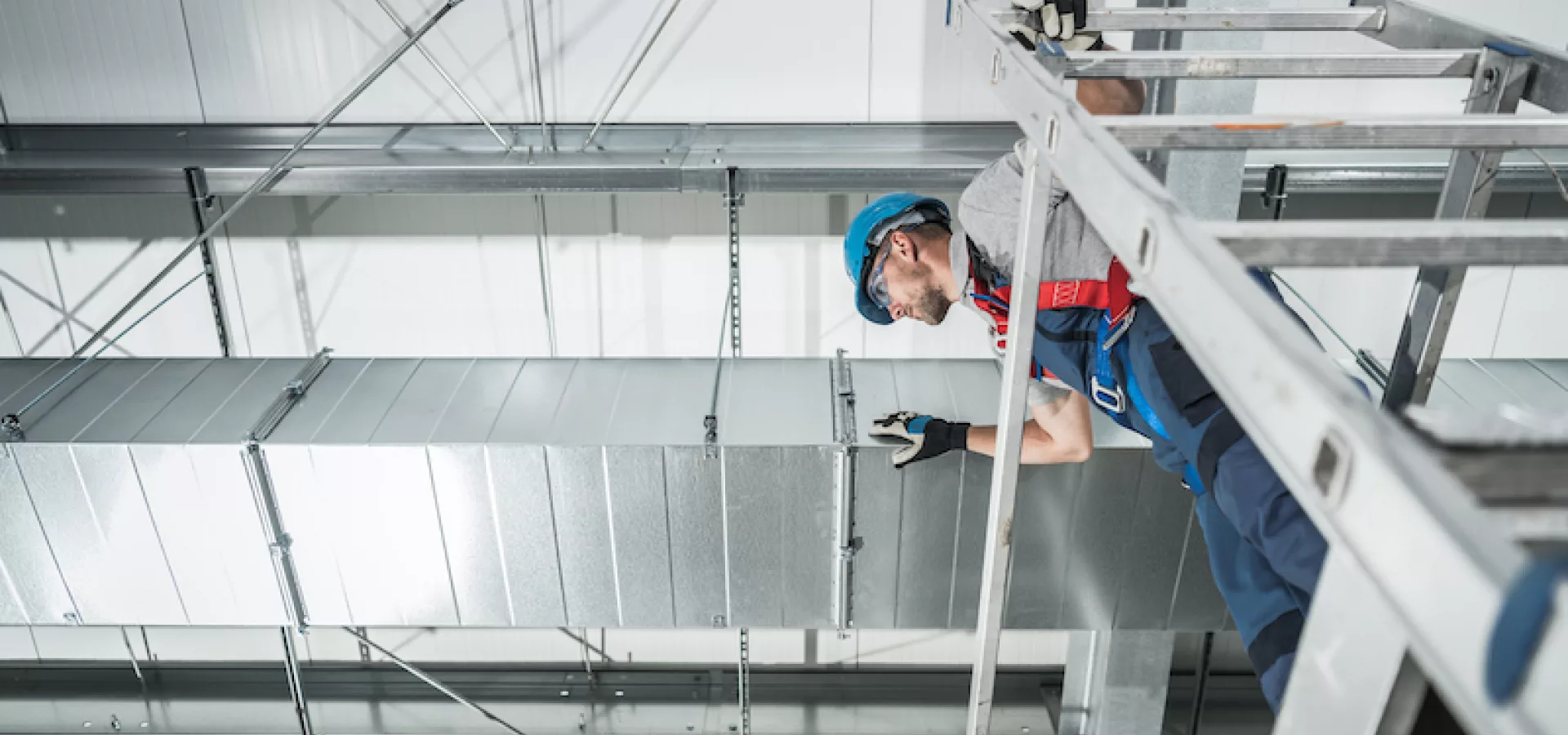
January 14, 2022
January 14, 2022
A quick debrief on zinc plating technology and the importance of passivation and topcoat technology.
Long gone are the days when - make it shiny - was good enough for surface finishing.
Every day, material engineers are looking for the next best thing and this is part of an exciting trend. Pushing the boundaries of what a coating can do is a fundamental part of innovation in our industry.
This past Sur/Fin (Surface Finishing industry’s annual conference in the United States), one of the keynotes featured practical futurist Michael Rogers who gave the attendees an opportunity to step back and realize how fast technology is changing our world in so many different fronts. One of his remarks was that material science is an enabler of all this change. It so happens that we in the surface finishing world are part of this.
So, what are these changes and how can we materialize them into impactful implementations?
Well, there are many interesting things going on in our industry but let us focus on what we at Pavco know best. Traditional corrosion protection finishes like zinc or zinc-alloy electroplating have been around for as long as current generations can remember. The sacrificial protection that zinc electroplating offers over steel is really hard to match. The relative ease of use, low cost and high output make this a great coating to apply. However, the road to getting to these statements has been bumpy. From the days when zinc electroplating could only be achieved via a cyanide rich electrolyte, to protecting the zinc coating using hexavalent chromates, the industry has evolved dramatically.
As we focus on extracting performance from a readily available industrial process, innovation needs to find its way in an evolutionary matter rather than revolutionary. There seems to be little to be done with the zinc coating itself other than applying it in more efficient ways, but if we focus on the subsequent layers that comprise this coating, that’s where innovation is fast to drive change.
Enter next generation passivates and topcoats
Passivate and topcoat technology is the focus of research with most proprietary suppliers and for a good reason, these are the most customizable layers. CrIII passivation has been widely adopted and improved from its first iterations switching from CrVI following the industry’s ELV (End of Life Vehicle) directive and other environmental regulation bodies. But with this change, Cobalt took the passenger seat in this amazing drive. This element and some of its compounds have been in the SVHC (Substance of Very High Concern) list from ECHA (European Chemical Agency) for years. While these types of lists regulate amounts used and type of applications allowed, they are sometimes regional and hence several SVHC compounds are still used in our industry.
It is here where companies can innovate away from hazardous components and sometimes extract better performance than the status quo. In the pursuit of development of next generation trivalent passivates; Pavco has discovered amazing performance out of Cobalt free formulations. The synergies that can be achieved with proper topcoat technology are groundbreaking.
As end-users request more of these finishes, the supply chain for the electroplating industry can keep funding innovation and discovering better and more environmentally conscious ways to do something we have done for decades. – make it shiny –
IT’S HOW YOU FINISH
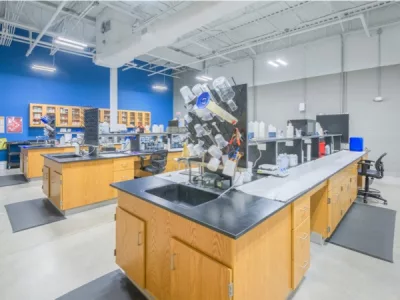
We’re a developer and supplier of chemistries for the metal finishing industry since 1948.
In PAVCO, we develop products and deliver services of the highest quality at a reasonable cost.