Beyond the Surface: The Science of Electrodeposition
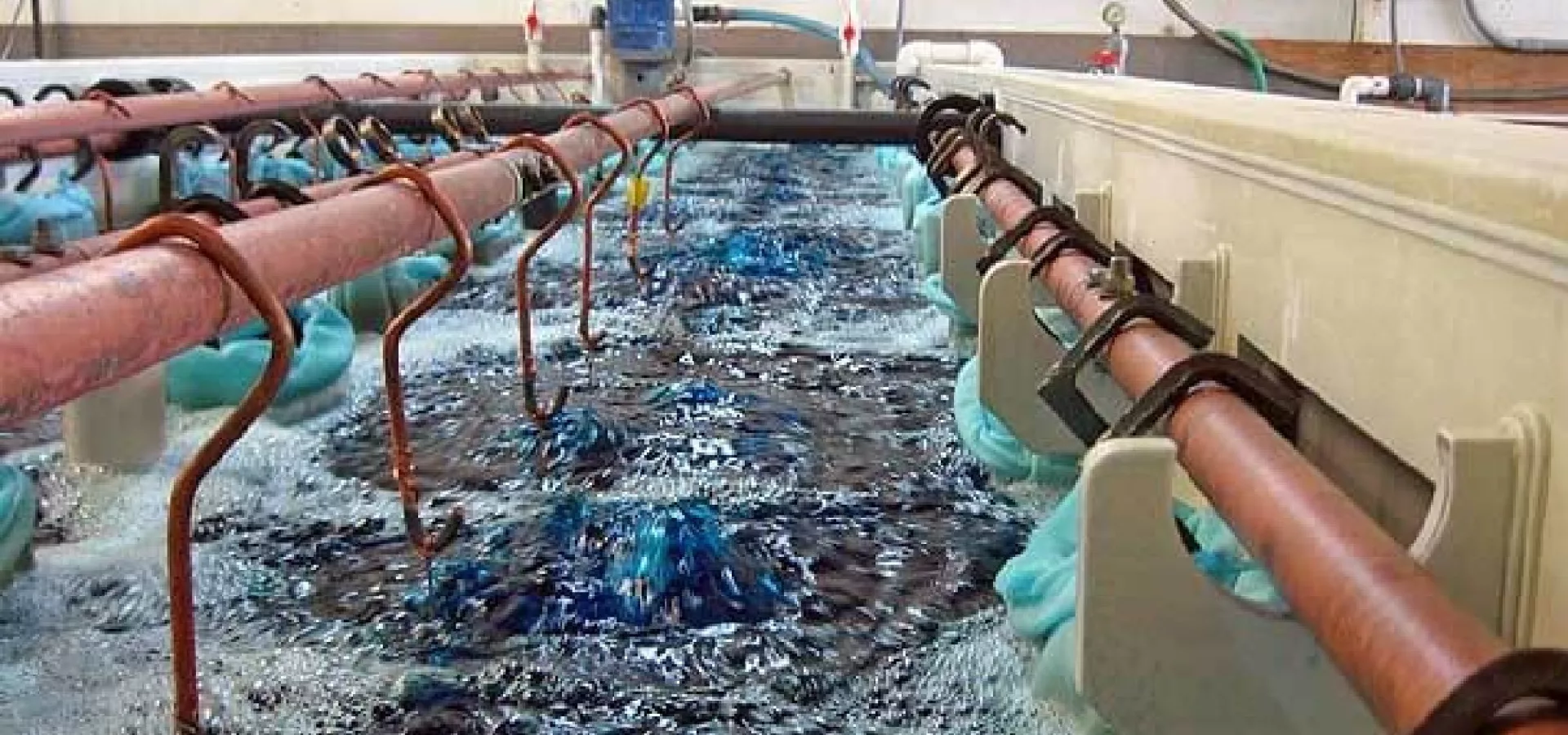
August 14, 2024
August 14, 2024
Electroplating is a sophisticated and widely employed technique in various industries, where a thin layer of metal is deposited onto a conductive substrate through the application of an electric current in an electrolyte solution.
This process is fundamental for enhancing wear resistance, providing corrosion protection, improving electrical conductivity, and enhancing aesthetic appeal. Understanding the science behind electrodeposition is crucial for industries that rely on high-quality metal coatings.
In this blog post, we will delve into the key components and principles of the electroplating process, focusing on the roles of the anode, cathode, electrolyte solution, and power source.
The Electroplating Process
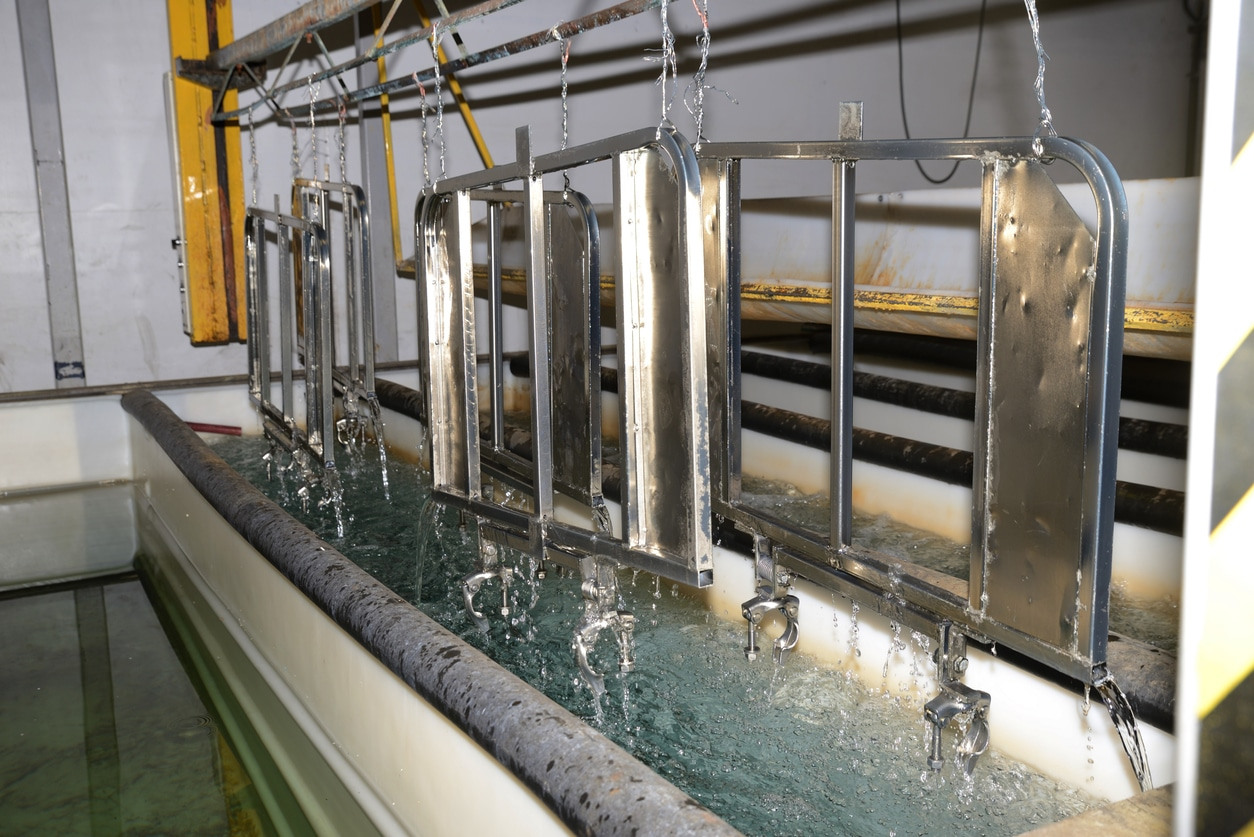
The electroplating process involves creating an electrolytic cell where two electrodes; the anode, and the cathode are immersed in an electrolyte solution containing ions of the metal to be plated. When an electric current is applied, it causes a redox reaction where one metal is oxidized at the anode and another metal is reduced and deposited at the cathode. This process can be broken down into several stages:
Preparation: The cathode is thoroughly cleaned and pre-treated to remove any surface impurities. This step is crucial for ensuring good adhesion of the metal layer.
Electrolytic Cell Setup: The anode and cathode are placed in the electrolyte solution, and the power source is connected to establish the electrical circuit.
Deposition: The electric current is applied, initiating the redox reaction. Metal ions from the anode dissolve into the electrolyte solution and are transported to the cathode, where they are reduced and deposited onto the substrate.
Post-Treatment: After the desired thickness of the metal coating is achieved, the substrate is removed from the electrolyte solution and subjected to post-treatment processes, such as passivation, topcoating, rinsing, drying, and sometimes heat treatment, to enhance the properties of the coating.
Key Components of Electroplating
Anode
The anode is the positively charged electrode, typically made of the metal to be deposited, but in some cases is inert. During the electroplating process, the anode dissolves into the electrolyte solution, releasing metal ions. These ions are then transported through the solution to the cathode, where they are deposited. The choice of anode material is essential as it determines the quality and properties of the final metal coating.
Cathode
The cathode is the negatively charged substrate that will receive the metal coating. It can be made of various conductive materials, depending on the application. The surface preparation of the cathode is critical, as any impurities or contaminants can affect the adhesion and uniformity of the metal layer.
Electrolyte Solution
The electrolyte solution is a key component of the electroplating process. It contains metal ions that facilitate the flow of electricity and enable the deposition of the metal onto the cathode. The composition of the electrolyte solution can vary depending on the metal being plated and the desired properties of the coating. Factors such as pH, temperature, and concentration of metal ions must be carefully controlled to achieve consistent and high-quality results.
Power Source
A direct current (DC) power supply drives the electrochemical reaction in the electroplating process. The voltage and current applied to the electrodes must be precisely controlled to ensure the proper deposition of the metal. Too high a current can lead to rough and uneven coatings, while too low a current can result in incomplete coverage. The power source must be able to deliver a stable and consistent current throughout the plating process.
Oxidation-Reduction Potentials (ORP)
Oxidation-reduction potential (ORP) measures the tendency of a solution to gain or lose electrons. In electroplating, ORP is crucial because it determines the feasibility of the electrochemical reactions. Metals with higher reduction potentials are more likely to be reduced and deposited onto the cathode.
For example, copper has a standard reduction potential of +0.34 V, making it favorable for electroplating processes. Understanding the ORP of different metals allows for the selection of appropriate materials and conditions for specific plating applications.
Pavco’s cutting-edge solutions
Pavco's solutions are designed to meet the specific needs of our clients, enhancing productivity, consistency, and longevity. Our services include:
Pre-plating solutions: This is a crucial step in the electroplating process that ensures a strong, long-lasting bond between the metal and the coating.
Plating technologies: We offer exceptional plating chemistry that delivers quality, durability, and corrosion resistance. Whether you require decorative plating or corrosion-protective finishes, we have the right products for your electroplating process lines.
Post-Plating solutions: Our post-plate solutions enhance the plated surfaces' performance, appearance, and longevity.
Staff training: Comprehensive training programs to ensure your team can fully capitalize on our cutting-edge technology and processes.
Contact us today to learn how our solutions can drive your success, conquer industry challenges, and elevate your operations.
IT’S HOW YOU FINISH
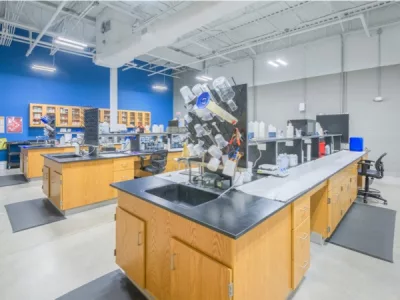
We’re a developer and supplier of chemistries for the metal finishing industry since 1948.
In PAVCO, we develop products and deliver services of the highest quality at a reasonable cost.