Alkaline Zinc Troubleshooting: Identify and Resolve Issues
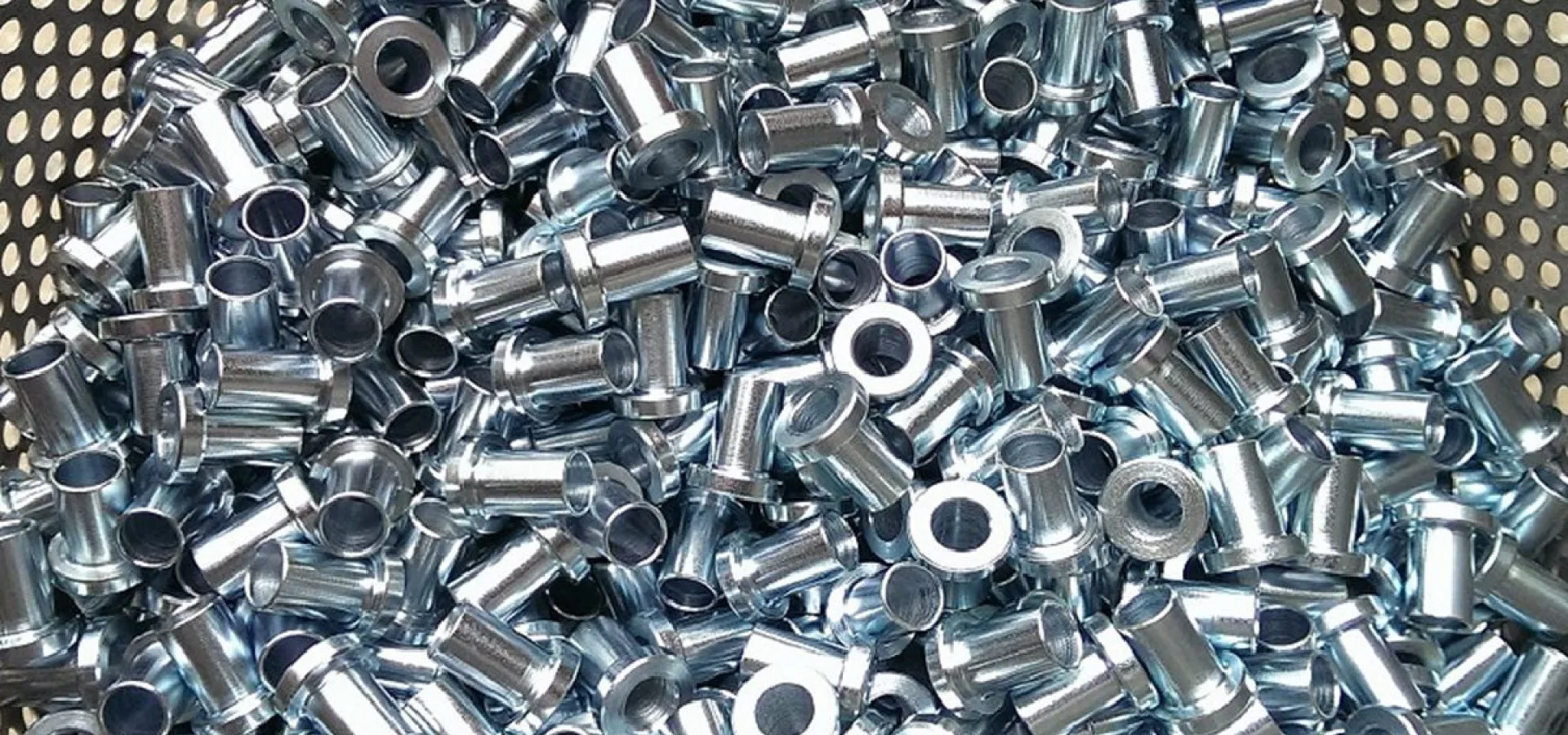
November 06, 2024
November 06, 2024
Alkaline zinc plating is a widely used electroplating process known for its excellent corrosion resistance and uniform coverage. However, like any industrial process, challenges can arise that require careful troubleshooting to maintain optimal performance.
In this blog post, we will explore how to identify and resolve common plating issues, ensuring your operations run smoothly and efficiently.
Identifying Plating Problems
The first step in troubleshooting alkaline zinc plating issues is identifying the issues. Common visual indicators include dull or cloudy deposits, blisters, rough areas, and uneven coverage. These issues can significantly affect the quality and appearance of the plated parts, leading to potential rework or rejection.
Visual Inspection
Conducting a thorough visual inspection of the plated parts is crucial. Look for signs of dullness, cloudiness, blisters, or uneven surfaces. Pay close attention to high current density areas for burning or dullness and low current density areas for dull deposits. These defects may indicate underlying issues such as improper bath chemistry or contamination.
Hull Cell Panels
Running Hull cells is another effective method for diagnosing plating issues. These tests help evaluate plating thickness and appearance at different current densities, providing insights into the bath's performance.
Common Issues and Pavco's Solutions
Once you've identified the issues, the next step is to address the root causes. Here are some common issues encountered in alkaline zinc plating and their corresponding solutions, powered by Pavco's expertise:
Slow Plating Speed / Poor Coverage
Check the zinc metal and starter concentrations and verify they are within the recommended range. Ensure the caustic soda level is at least 16 ounces per gallon.
High levels of carbonates in the alkaline zinc plating bath can significantly reduce the plating speed. Carbonates form as a byproduct of the chemical reactions in the plating process, accumulating over time. As carbonate levels increase, they interfere with the efficiency of the plating bath, which can lead to slower deposition rates,uneven coverage, and in some cases a burn like pattern in the HCD
Blisters or Rough Deposits
Blisters and rough deposits are often caused by excess brightener or insufficient cleaning. Reduce the brightener concentration if necessary and improve the cleaning cycle.
High-performance cleaners and filtration solutions help eliminate contaminants, ensuring a smoother finish and better-quality plating.
Dull or Burned Deposits
Adjust the starter and brightener levels based on Hull cell test results and check the plating bath temperature. Verify that the current density is within the proper range and maintain the balance of NaOH to ZnO, preventing uneven deposits and ensuring high-quality results.
Excessive Brightener Consumption
Excessive brightener use can lead to higher costs and inconsistent plating results.. Skip plating can also occur in the LCD when brightener concentration is too high in the plating bath. A carbon treatment will remove excess brightener from the plating bath.
Uneven Distribution
Uneven distribution of alkaline zinc plating can result from high or low zinc and or starter concentrations. Poor anode placement and a lack of solution agitation can also cause poor distribution.Effective troubleshooting of alkaline zinc plating issues requires a proactive approach and attention to detail. By identifying issues early and implementing routine analysis and hull cells, you can maintain high-quality plating results while reducing operational costs.
Pavco's plating chemistries and expert support can help you overcome challenges and optimize your plating processes. Contact us today to learn more about how our innovative solutions can elevate your plating operations.
IT’S HOW YOU FINISH
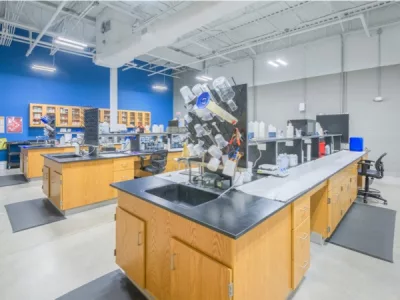
We’re a developer and supplier of chemistries for the metal finishing industry since 1948.
In PAVCO, we develop products and deliver services of the highest quality at a reasonable cost.