Maximizing Productivity in the Zinc Barrel Plating Process
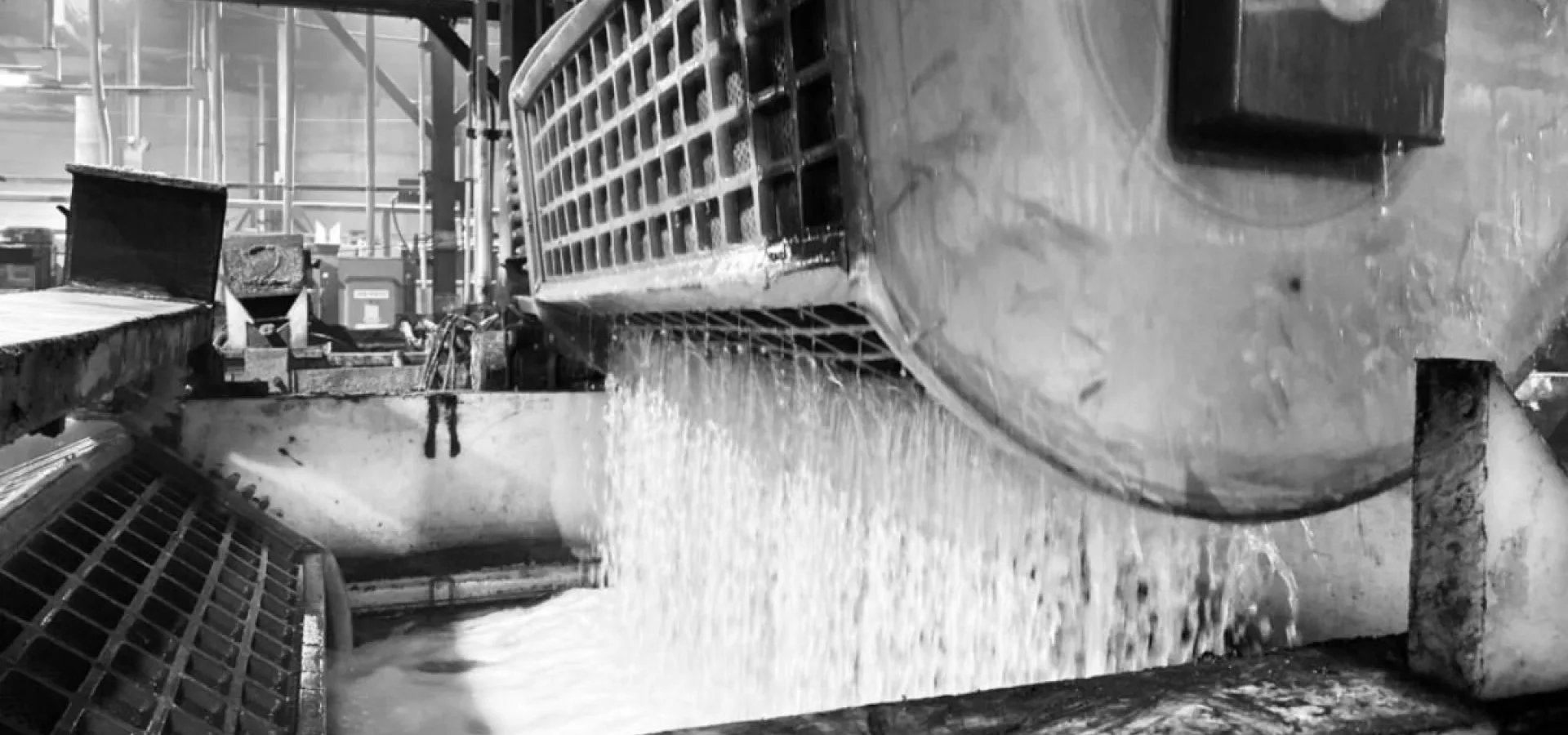
October 08, 2024
October 08, 2024
The zinc barrel plating process is a cornerstone of the manufacturing industry, especially for finishing small metal parts like screws, nuts, and bolts. This process not only enhances the visual appeal of components but also provides essential corrosion protection, making it indispensable in industries that prioritize durability and mass production.
Understanding Barrel Plating
Barrel plating involves placing small parts into a rotating barrel submerged in an electrolyte solution. The continuous rotation ensures that all surfaces of the parts receive uniform exposure to the plating solution, resulting in an even metal coating.
This method is especially effective for plating large quantities of small parts simultaneously, making it a cost-effective solution for mass production environments.
Key Factors for Maximizing Productivity
Current Density Higher current densities can accelerate the plating process, provided the electrolyte's salt and additive levels are well-balanced. The current density, or the electric current passing through the surface area of the plating parts, directly impacts the deposition rate of metal ions.
Barrel Design The design of the barrel is critical to ensuring efficient plating. Barrels with larger perforations allow for better flow of the plating solution and current, improving both the speed and uniformity of the plating. Additionally, materials like non-reactive plastics or stainless steel are preferred for barrel construction, as they prevent unwanted chemical reactions during the process.
Barrel Rotation Optimizing the barrel’s rotation speed is essential. Slow rotation can hinder the plating rate, while fast rotation may cause parts to flip less frequently, resulting in uneven coating. Achieving the right balance in rotation speed ensures that all parts are evenly exposed to the electrolyte solution, leading to a more uniform finish.
Load Capacity Overloading the barrel can slow down the plating process and result in non-uniform coating due to restricted movement and reduced solution flow. Adhering to recommended load capacities ensures optimal solution contact, facilitating even plating across all parts.
Maintenance of Danglers These elements carry the electrical current into the barrel and need regular maintenance to prevent current loss. Well-maintained danglers ensure an even current distribution throughout the barrel, minimizing the risk of defects and improving the overall quality of the plating.
Temperature Control Increasing the bath temperature can enhance the plating rate by improving ion mobility in the solution. However, careful monitoring is required to prevent negative effects on the plating quality. Utilizing advanced solutions like Pavco’s Smart Zinc Premier, a chloride zinc plating system, that was specifically designed for operating at higher temperatures while maintaining plating quality and efficiency.
Maximize your productivity
Maximizing productivity in zinc barrel plating requires a deep understanding of the factors influencing process efficiency. By optimizing variables like current density, barrel design, rotation speed, load capacity, and temperature, manufacturers can achieve higher throughput and superior product quality.
Solutions like Pavco’s plating chemistries, including Smart Zinc Premier, provide manufacturers with the tools they need to improve process efficiency, reduce costs, and ensure long-lasting corrosion protection for metal parts.
IT’S HOW YOU FINISH
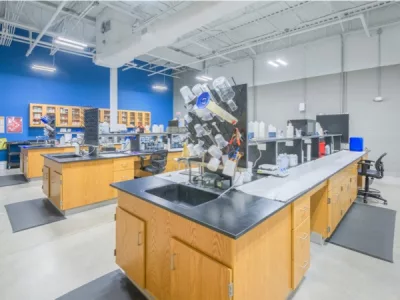
We’re a developer and supplier of chemistries for the metal finishing industry since 1948.
In PAVCO, we develop products and deliver services of the highest quality at a reasonable cost.