Understanding Galvanic Reaction: How It Affects Metal Durability
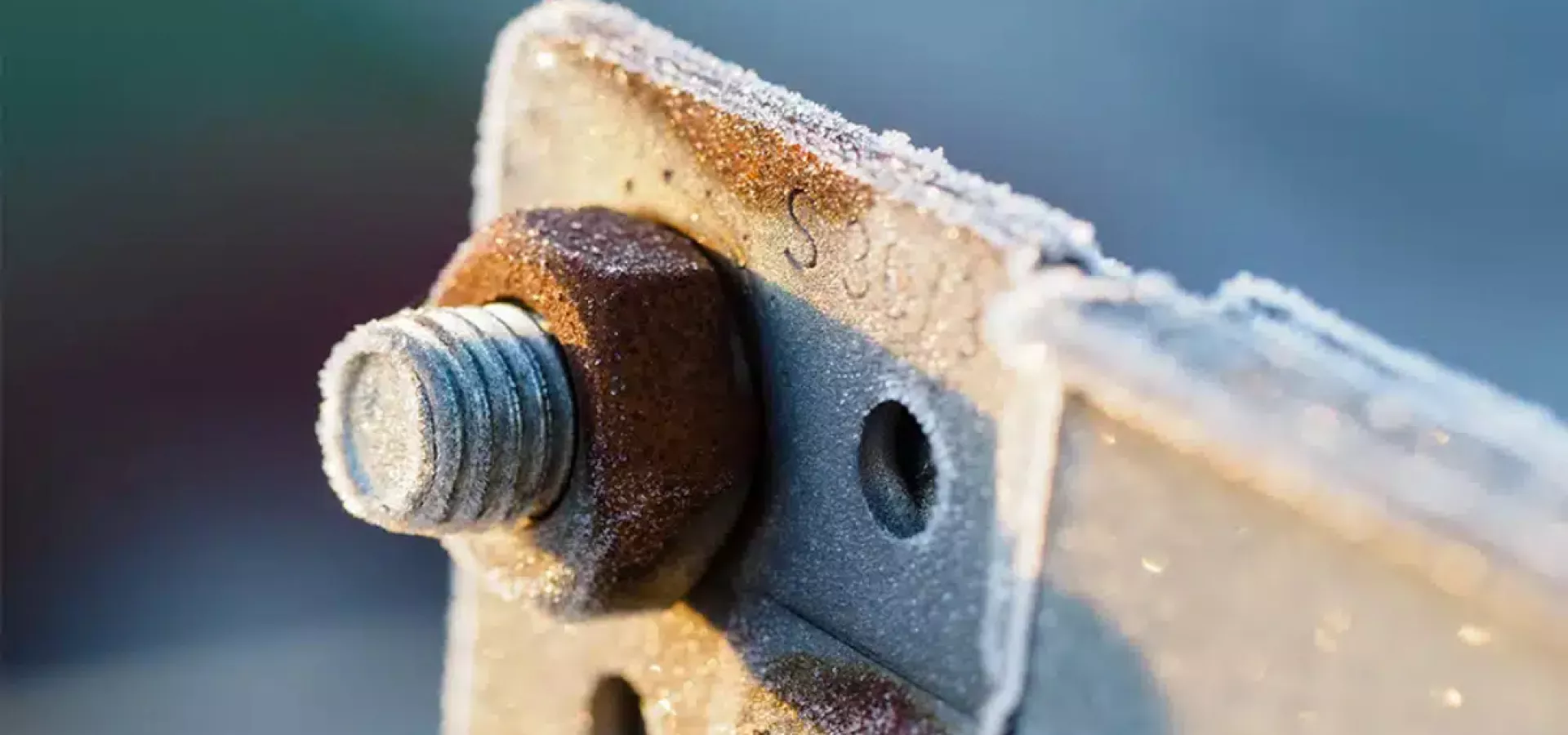
July 24, 2025
July 24, 2025
Galvanic corrosion, also referred to as bimetallic corrosion, is an electrochemical process that significantly impacts the durability of metal structures and components. This form of corrosion arises when two dissimilar metals (e.g., aluminum and steel) are in direct electrical contact in a corrosive environment, such as salt water.
In such a scenario, a galvanic cell is formed, and due to the difference in electrochemical potential between the metals, a redox reaction occurs. The less-noble metal (anode) corrodes at an accelerated rate, while the more-noble metal (cathode) is preserved, potentially even corroding more slowly than it would in isolation. Understanding this mechanism and employing strategic countermeasures is crucial for maximizing the service life of metallic components.
The Electrochemical Nature of Galvanic Corrosion
Galvanic corrosion is inherently an electrochemical process. It results from a potential difference between two metals in electrical contact, leading to electron flow through the conductive connection and ion migration through the electrolyte.
For instance, when aluminum and steel are paired in the presence of salt water, aluminum (being less noble) becomes the anode and corrodes preferentially:
Zn → Zn²⁺ + 2e⁻
This degradation occurs to protect the more noble metal (steel in this case), which acts as the cathode and facilitates reduction reactions.
Key Factors Influencing Galvanic Corrosion
Electrochemical Potential Difference
The greater the difference in electrochemical potential between two metals, the more aggressive the corrosion. Use the Galvanic Series Chart to predict compatibility.
Presence of an Electrolyte
Galvanic corrosion only occurs in environments where a conductive electrolyte (like salt water) is present.
Area Ratio (Cathode-to-Anode)
A large cathode in contact with a small anode will significantly accelerate corrosion of the anode. This ratio should always be minimized during design.
Environmental Conditions
Temperature, humidity, and salinity of the environment can further influence corrosion rates.
Effects on Durability and Performance
Structural Integrity: Compromised by accelerated degradation of critical parts, especially in infrastructure like pipelines and marine platforms.
Aesthetic Damage: Pitting, discoloration, and surface degradation affect visual appeal and consumer perception.
Functional Impairment: Connectors, fasteners, and other essential components may lose functionality or fail entirely.
Practical Strategies to Prevent Galvanic Corrosion
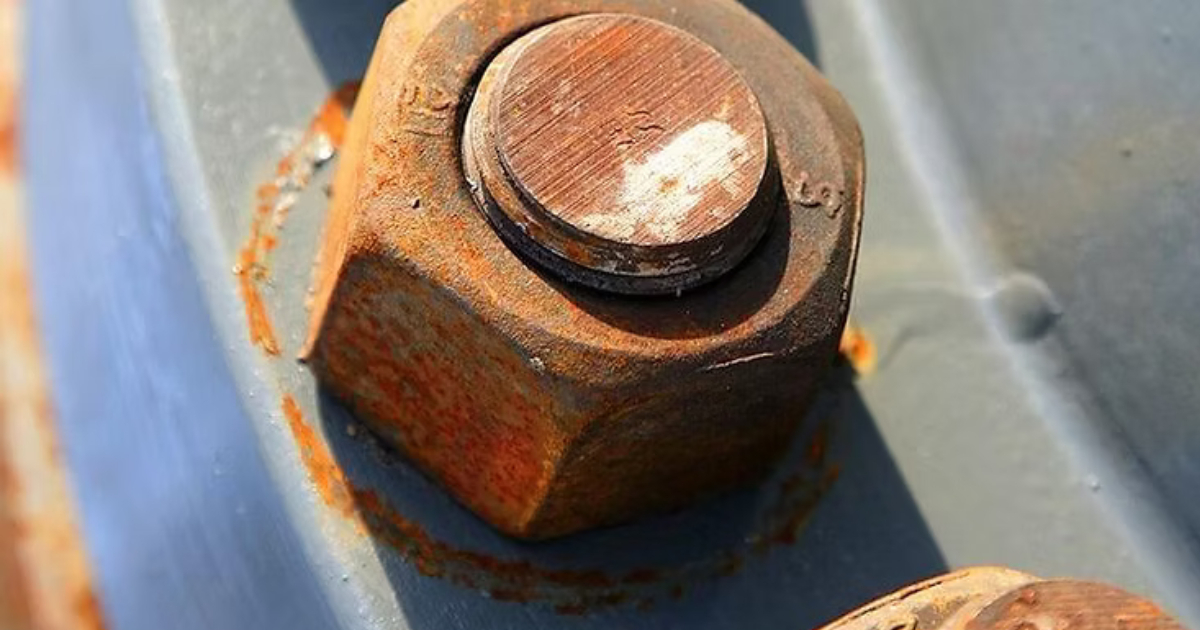
Select Compatible Metals
Choose metals with similar electrochemical activity to minimize galvanic potential. For necessary dissimilar pairings, refer to the Galvanic Series to assess relative nobility.
Apply Matching Plating Chemistries
Use PAVCO plating solutions to coat both metals with the same plating chemistry, minimizing electrochemical disparity.
Insulate the Metals
Electrically disconnect the metals using non-conductive materials like polymer bushings, gaskets, or PAVCO topcoats. These topcoats break the electrical connection, effectively preventing galvanic interaction.
Use Sacrificial Anodes
In some applications, a third metal like zinc or magnesium can be introduced as a sacrificial anode, corroding in place of the protected structure.
Control the Area Ratio
Design assemblies to avoid a small anodic metal surface connected to a large cathodic metal. This helps reduce corrosion current density and damage rate.
Isolate from Electrolytes
Use barriers like coatings, greases, or sealants to prevent electrolyte access, especially in marine or high-humidity environments.
Partner with PAVCO for Expert Corrosion Solutions
PAVCO is a trusted leader in corrosion resistant electroplating. We provide:
Customized Technical Guidance: Our electroplating specialists evaluate your materials and conditions to recommend the optimal corrosion mitigation strategy.
Advanced Plating Chemistries: Tailored to equalize electrochemical behavior between dissimilar metals.
Non-Conductive Topcoats: Designed to electrically insulate and protect metal interfaces.
Ongoing Support and Training: Ensure proper implementation and long-term protection.
Ready to protect your assets?Contact us todayfor personalized corrosion control solutions that preserve structural integrity and extend the life of your products.
IT’S HOW YOU FINISH
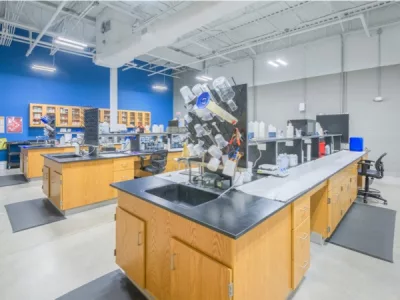
We’re a developer and supplier of chemistries for the metal finishing industry since 1948.
In PAVCO, we develop products and deliver services of the highest quality at a reasonable cost.