Corrosion protective coatings for diverse applications
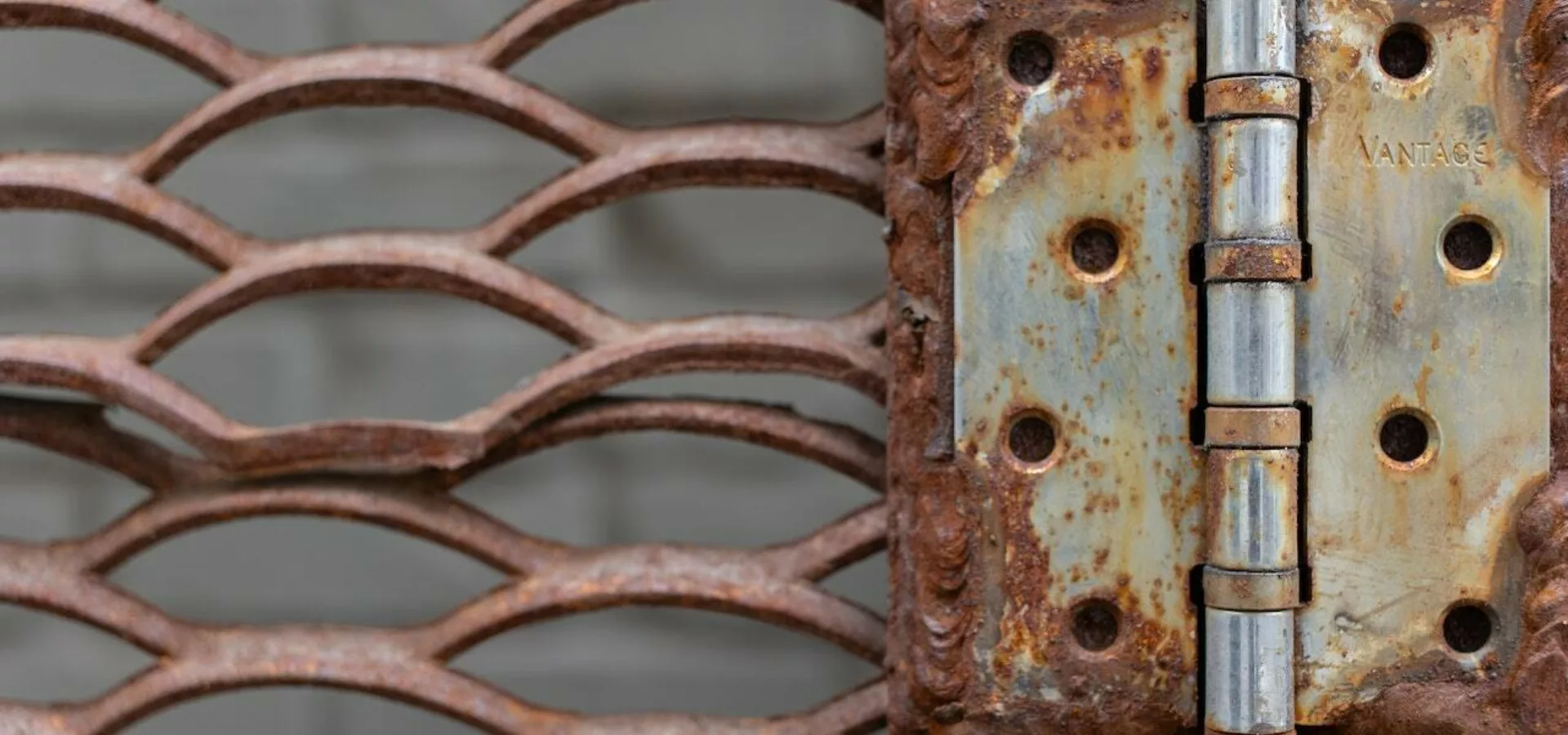
August 31, 2022
August 31, 2022
Corrosion generates billions of dollars in losses every year around the world. Many metallic components are exposed to this accelerated oxidation process, which rapidly shortens their functionality.
For centuries we have tried different ways to extend the life of products by coating them with protective materials, providing sacrificial corrosion properties, or isolating their surfaces from oxygen or chemical agents in the environment that accelerate this corrosion.
Which properties must be considered to combat corrosion?
In order to extend the functionality of these products, we can focus on various properties, including lubricity, hardness, brightness, porosity, conductivity, ductility, adhesion, solderability, and/or wear resistance.
Therefore, many coatings have been developed to provide these specific characteristics in order to extend the duration of these products. Throughout the years, processes, such as painting, powder coating, dip spin, hot dip galvanizing, electro-coating, and anodizing, have emerged in the industry as ways to prevent corrosion.
PAVCO focuses primarily on the process of electroplating to delay metal corrosion. We choose from alkaline or acid water-base plating solutions that contain metals, such as zinc, nickel, tin, chrome, copper, and cobalt.
How does this process work?
We apply a single layer or multiple layers of coatings containing one of these metals in order to protect the products. Additionally, new technology has recently been developed that allows us to apply a coating containing an alloy of two or more metals.
As such, manufacturers have a wide variety of metals to select from when selecting a protective coating for their substrate in order to best enhance its functionality. The most important factor to consider when selecting a corrosion protective coating, among the various properties desired for a product’s functionality, is the Electromotive Force (EMF).
The EMF defines the nobility or activity of one metal in reference to the base metal of the part. Generally, the coated metal needs to be more active than the base metal to serve as a sacrificial coating in order to protect it from corrosion. Zinc is the most widely coating metal used over iron components for corrosion protection.
However, some alloys, such as zinc-nickel, provide 4-5 times higher corrosion protection than zinc over iron. For this reason, the demand for zinc-nickel has recently been increasing in the industry, although it is more expensive than pure zinc.
Another application that is frequently used is nickel-chrome because of its decorative properties. In many cases, it is used to protect from aggressive corrosive environments with high temperature and humidity, acid water from rain, salt water from coastal environments and road salt, mud containing calcium chloride, and electrolytes from human sweat.
However, nickel is more noble than iron, so it is less protective against corrosion when compared to zinc. Therefore, in many cases, a multilayer coating made of nickel strike/copper/semi-bright nickel/high sulfur nickel/bright nickel/microporous nickel/chrome layers is required to enhance corrosion protection.
Additional coatings after electroplating
Once the base metal is protected with the sacrificial coating, chromates (Cr+6) or passivates (Cr+3) should be applied over this protective coating to increase corrosion resistance. Nowadays, passivates with trivalent chromium are preferred over hexavalent chromates because hexavalent chromates have a carcinogenic effect.
A conversion coating from Cr+6 or from Cr+3 is generated during the immersion of the plated part into working chromate or passivate solution. Working conditions, such as pH, temperature, concentration, immersion time, and agitation, are critical for the coating to develop. In most cases, this coating also provides the desired color of the product.
At this step, manufacturers can choose to protect the base metal further by applying a topcoat or sealer over the conversion coating. The sealer can provide many properties other than corrosion protection, such as enhanced appearance, modify the coefficient of friction for torque applications, fluid compatibility for automotive and agriculture applications, wear resistance, and self-cleaning properties. Some sealers can provide conductive or insulating properties for electronic applications.
The sealers are generally classified as inorganic silicate coating or inorganic-organic hybrid coating. The latter can have multiple ingredients such as polymer, colloidal silica, wax, wetting agent, co-solvent, and defoamer.
In some cases, they can contain cross-linker and adhesion promoters, UV tracers, dyes, antibacterial agents, or antifreeze agents. As you can see, this final coating can provide many properties other than corrosion protection.
PAVCO has developed many of these coatings throughout the years, providing innovative technology in the electroplating process, passivates and sealers, and providing a wide range of products with a variety of colors and appearances required in the industry.
We have also developed sealers with enhanced properties for corrosion resistance, auto fluid compatibility, coefficient of friction required for automotive, aerospace and construction applications, and transparent sealers for black passivates with minimum drip marks.
Also, heat resistance, tolerance for changes in the pH of the solution, UV tracer and dyes application for identification. Most of these processes are easy to control by the lab or plant operator. The world's technology changes rapidly, and the requirements for corrosion prevention increase every day.
These changes require new materials and processes to be able to provide superior coatings with increasing corrosion resistance without affecting the function and properties of the products. We are convinced of the quality of our products.
We invite you to check out all the downloads you can do on our site, and don't forget to check our blog to learn more about the metal finishing industry all around the world. Have a happy plating, see you in the next!
Juan Araque
Technical Service Engineer
IT’S HOW YOU FINISH
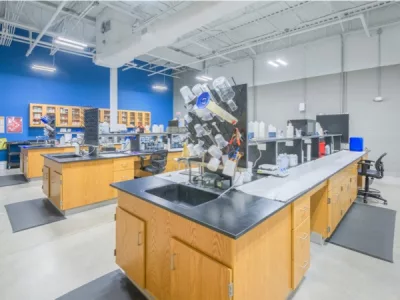
We’re a developer and supplier of chemistries for the metal finishing industry since 1948.
In PAVCO, we develop products and deliver services of the highest quality at a reasonable cost.