Role of Anodes in Electroplating
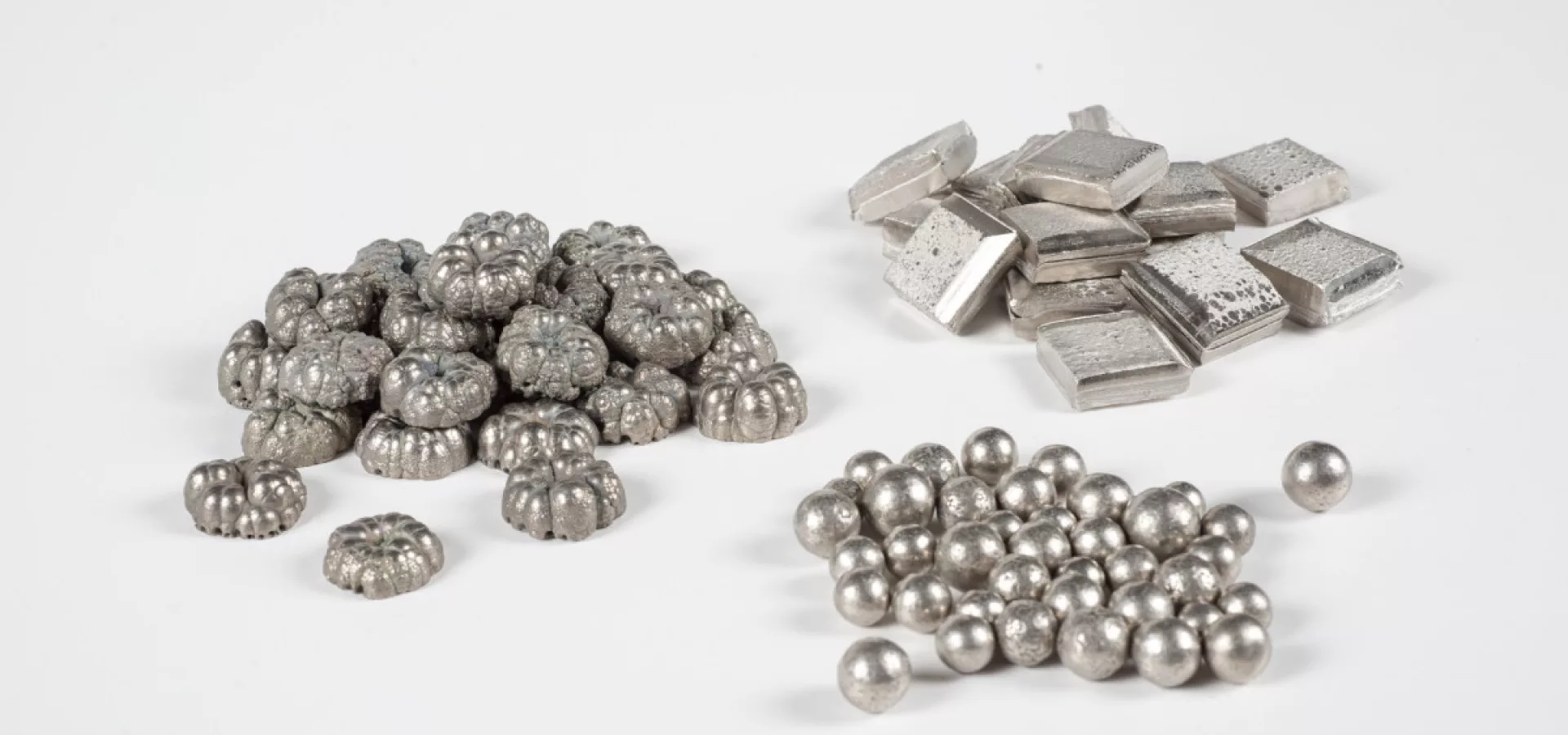
November 06, 2024
November 06, 2024
Electroplating is a critical industrial process that involves the deposition of a metal layer onto a substrate to enhance its properties such as corrosion resistance, aesthetic appeal, and surface hardness. At the heart of this process lies the anode, a component whose design and material selection are pivotal to the success of electroplating operations.
In this blog post, we explore the multifaceted role of anodes in electroplating, their impact on process efficiency, and how innovative anode technologies can address industry challenges.
Anodes: The Backbone of Electroplating
Critical Role in Electroplating
Anodes are indispensable in the electroplating process, serving as the positive electrode in the electrochemical cell. They complete the circuit by providing the oxidative current necessary for the deposition of metal ions onto the workpiece. The choice of anode material and design is crucial as it directly affects the efficiency, quality, and cost of the plating process.
Functionality and Selection
The functionality of an anode is determined by its ability to supply metal ions in solution through electrochemical and chemical dissolution processes. Anodes must be chosen based on the specific requirements of the plating application, considering factors such as the type of metal to be deposited, the plating environment, and the desired properties of the finished product.
Innovations in Anode Technology
Inert Anodes
In some plating baths, inert anodes are employed to prevent the dissolution of metal ions. These anodes offer several advantages, including reduced consumption of consumables and increased sustainability of the plating process. Inert anodes are particularly beneficial in trivalent-chromium plating baths.
Membrane Anodes
Membrane technology represents a significant advancement in electroplating, offering a competitive edge in acid zinc and acid zinc nickel plating baths. Membrane anodes help lower metal growth and help maintain a consistent quality deposit. In alkaline zinc-nickel solutions the membrane anodes prevent organic compounds from decomposing at the anode, which can inhibit cyanide formation.
Conformal Anodes
For complex or irregular-shaped workpieces, conformal anodes are invaluable. They ensure more uniform current distribution and plating thickness, addressing common challenges such as uneven deposition and defects. By tailoring the anode geometry to match the workpiece, conformal anodes enhance the quality and consistency of the plated layer.
Internal Anodes
Internal anodes are strategically placed within hollow or recessed areas of complex parts to improve plating uniformity in areas where current density is naturally low. By positioning these anodes closer to challenging surfaces, they ensure a more consistent deposit thickness in deep recesses and intricate shapes. Internal anodes are essential for achieving comprehensive coverage on complex geometries, reducing the likelihood of under-plated regions and ensuring a high-quality finish across the entire workpiece.
Addressing Industry Challenges
Operational Efficiency and Cost
Anode design and material selection can significantly impact operational costs. Innovations such as consumable or inert materials, tailored ion-release rates, and anode shields or bags enhance efficiency while minimizing material wastage and hazardous by-product generation.
Environmental Considerations
The electroplating industry faces increasing pressure to reduce its environmental footprint. Anode technologies that minimize waste and enable resource recovery are crucial for meeting sustainability goals. Membrane anodes, for instance, prevent the breakdown of organic compounds at the anode, maintaining high productivity and quality of the plating line and can extend the life of the plating bath.
Quality and Consistency
Achieving uniform plating thickness and avoiding defects are perennial challenges in electroplating. Anodes engineered to optimize current distribution play a vital role in ensuring the thickness, adhesion, and quality of the plated layer. Proper anode-cathode spacing and positioning are integral to achieving the desired outcomes.
Enhance your metal processes
Anodes are not merely passive components in the electroplating process; they are proactive tools that shape the deposition process. By carefully selecting and designing anodes, plating shops can enhance efficiency, reduce costs, and meet stringent environmental standards.
At PAVCO, we understand the critical role anodes play in your electroplating processes. Our innovative technologies are designed to enhance efficiency, quality, and sustainability in your plating processes.
Reach out to us today to discuss your specific requirements and learn how we can help optimize your plating operations.
IT’S HOW YOU FINISH
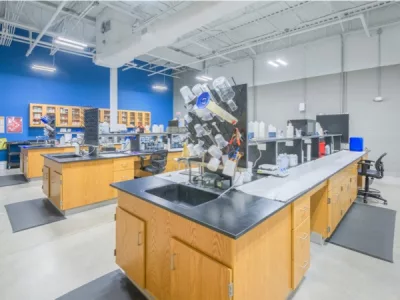
We’re a developer and supplier of chemistries for the metal finishing industry since 1948.
In PAVCO, we develop products and deliver services of the highest quality at a reasonable cost.