Rust Prevention Through Electroplating
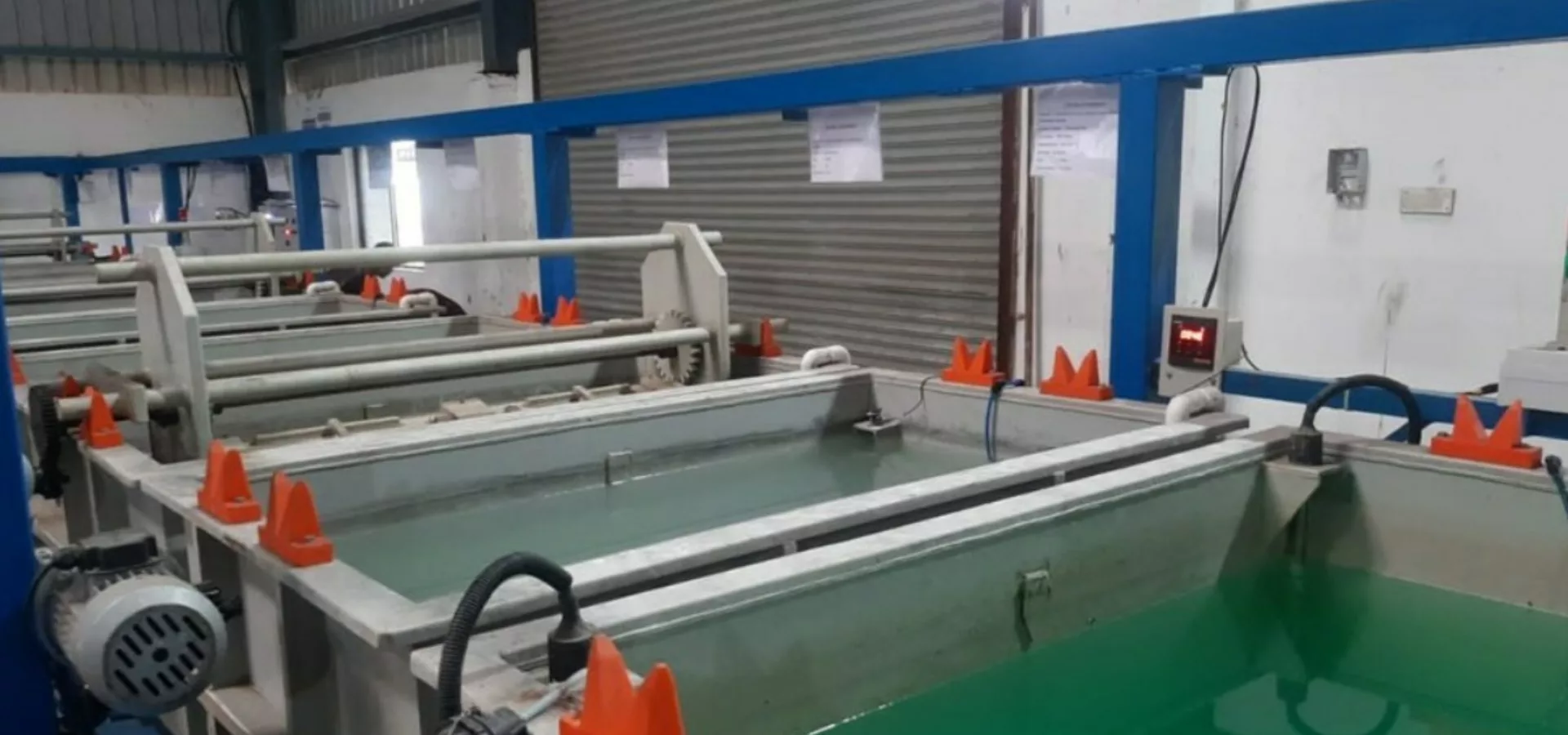
July 09, 2024
July 09, 2024
Ever wondered how that shiny chrome finish on your car bumper keeps the rust at bay? The answer lies in a fascinating process called electroplating. But before we delve into the world of electroplating, let's tackle the enemy it fights: rust.
Rust is the chemical term for the iron oxide that is produced when moisture and oxygen interact with iron or steel. Usually, it is denoted by the chemical formula Fe3O4. Iron oxide is created when iron atoms lose electrons to oxygen molecules in the air during rusting, which is a sort of oxidation reaction. The reddish-brown hue that corrodes metal surfaces, such as old nails or automobile components left outside.
What is Galvanic corrosion?
Imagine a tiny battery forming between two different metals in a salty solution (like seawater). This is essentially a galvanic cell, where an unwanted electrical current flows and accelerates corrosion. In this battle, one metal acts as the anode (sacrificial offering) and corrodes easily, while the other, the cathode, enjoys some protection. Iron, the main ingredient in steel, is particularly vulnerable to this attack, readily turning into rust (iron oxide).
To predict this, metallurgists use the galvanic series of metals. This ranking system tells you which metals become anodes (corrode first) when paired with others. By understanding this hierarchy, we can strategically choose a protective metal for electroplating.
Electroplating: The shining armor against rust
Electroplating is like putting a metal suit of armor on your vulnerable steel. It involves using an electric current to deposit a thin layer of a different metal onto the steel's surface. This creates a barrier that shields the steel from the environment and prevents the flow of the destructive current from a galvanic cell.
Zinc, a champion on the galvanic series, is a popular choice for electroplating steel. This is because zinc corrodes more easily than steel, acting as a sacrificial anode. Even if the plating gets scratched, zinc corrodes first, protecting the steel underneath.
The charm of Zinc Electroplating
Zinc electroplating boasts several advantages. It's a relatively affordable process, making it ideal for mass-produced items like screws, nails, and car parts. Additionally, zinc offers excellent corrosion protection, especially in mild environments.
The automotive and construction industries heavily rely on zinc electroplating for rust prevention. You'll find it on car bodies, fasteners, and building materials exposed to outdoor elements. However, it's important to note that zinc plating can be susceptible to wear and tear in harsh environments.
Beyond zinc: A broader arsenal for rust prevention
While zinc reigns supreme in many applications, electroplating offers a wider arsenal of weapons against rust. Nickel, for example, provides good corrosion resistance and a lustrous finish, but requires a great thickness and, in many cases, multilayer. Chromium, another popular option, offers exceptional hardness and a dazzling shine, often used for car parts that require both aesthetics and durability.
The choice of plating material depends on the specific needs. If a component demands high hardness and a decorative finish, nickel or chromium might be preferable. However, for cost-effective protection in mild environments, zinc remains the champion.
Choosing the right weapon: Electroplating vs. other methods
Choosing your defense strategy depends on factors like the environment, desired lifespan, and budget. By understanding the science behind electroplating, you’ll be able to make informed decisions to keep your metal objects rust-free for years to come.
Pavco’s plating technologies offer tailored solutions to protect against corrosion. Contact us today to find the ideal products for your specific needs!
IT’S HOW YOU FINISH
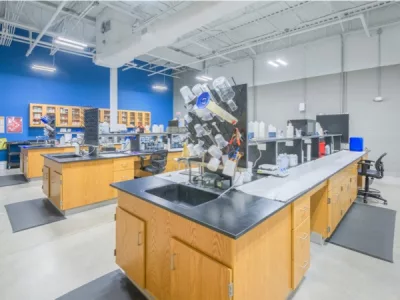
We’re a developer and supplier of chemistries for the metal finishing industry since 1948.
In PAVCO, we develop products and deliver services of the highest quality at a reasonable cost.