Hexavalent vs Trivalent Chromium
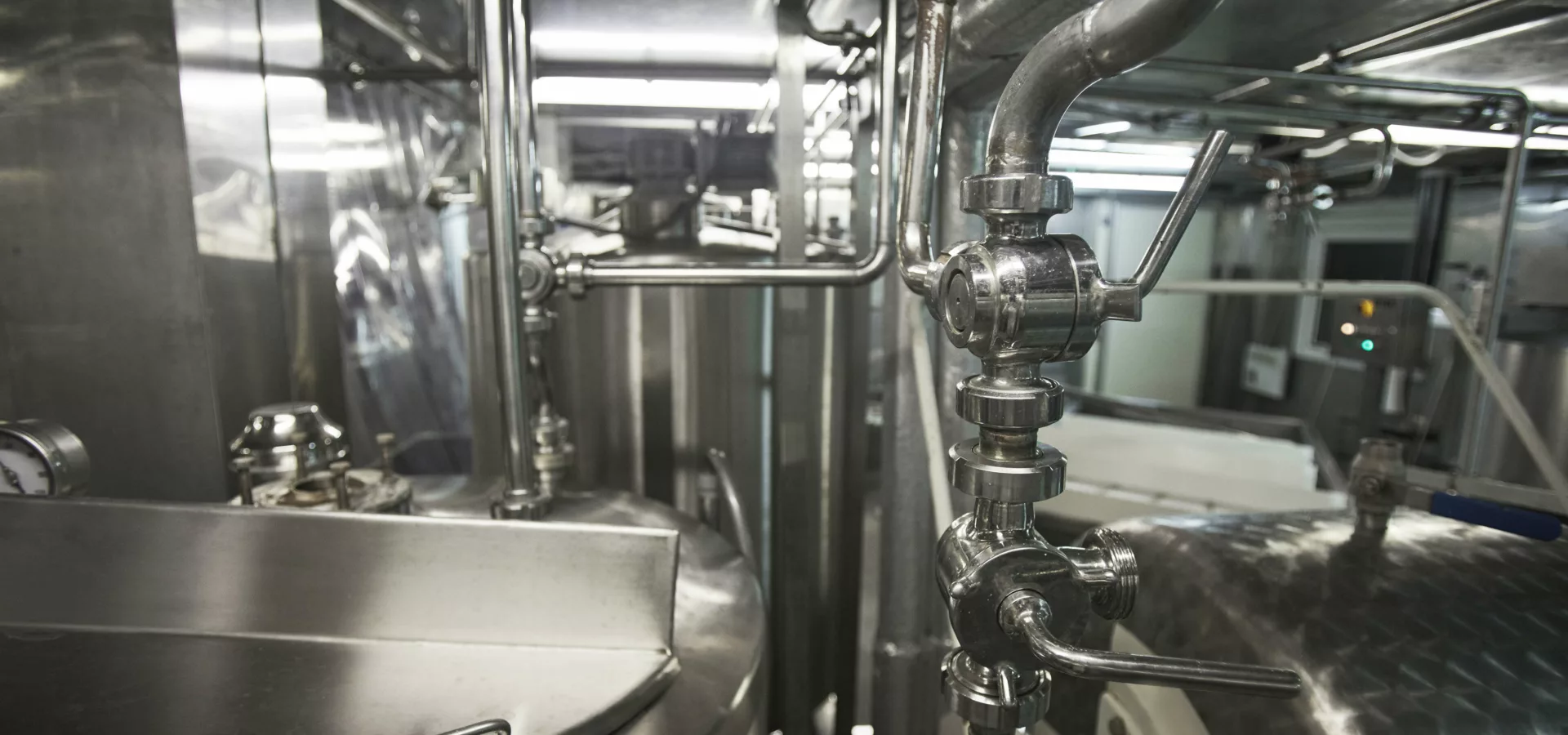
June 13, 2022
June 13, 2022
Chromium readily comes to mind when we think of things that shine. We know of course that not all that shines is chrome. Chrome is applied by an electroplating process and depending on the chemistry of the plating bath, we can produce functional chrome with hexavalent chromium or decorative chrome plating using hexavalent and trivalent chromium.
Functional electroplated chromium coatings are known for their high resistance to tarnish, their high hardness, and their low coefficient of friction. With a bright silver and a blueish appearance, they are widely used as decorative finishes.
While chromium deposits from hexavalent electrolytes are silver with a blueish tinge, those formed from trivalent chromium baths can have an attractive and smoky appearance. Black chromium deposits can also be formed and are often used for optical equipment and cameras.
Chemistry for Hexavalent Chromium
Hard chromium plated deposits, which are usually thicker plating, are widely used in the mining and aircraft industries and for hydraulics and metal forming equipment. They are also used in the finishing of medical and surgical equipment.
Hexavalent chromium electrolytes require a source of chromium ions and one or more catalysts in order to plate. The formulation of the traditional process, called the conventional bath, contains hexavalent chromium and sulfate as the only catalyst.
Proprietary additives that can be added to the conventional hexavalent chromium plating bath formulation to enhance the process are called mixed-catalyst baths since the additives contain at least one additional catalyst in addition to sulfate.
Given that hexavalent chrome has a record of doing what it does very well, we must contend with the high cost of waste treatment, OSHA regulation concerning mist and vapor handling. Another aspect of plating technical issues relates to high current density burning and whitewash. All of these will have to be balanced in the scheme of things when deciding on the process to implement.
Chemistry for Trivalent Chromium
The electrolytes for trivalent chromium plating solutions differ in chemistry, but they all contain a source of trivalent chromium, which is typically added as the sulfate or chloride salt. They also contain a solubilizing material that combines with the chromium to permit it to plate in the desire to increase conductivity in the solution.
Wetting agents are used to help in the deposition reaction and to reduce the surface tension of the solution. The reduced surface tension essentially eliminates the formation of mist at the anode or cathode. The plating process operates more like Nickel bath chemistry than a Hex chrome bath. It has a much narrower process window than hexavalent Chrome plating. That means that most of the process parameters must be controlled well, and much more precisely. The efficiency of Trivalent Chrome is higher than that for Hex. The deposit is good and can be very attractive.
Hexavalent chromium plating has its disadvantages, however. It is known as human carcinogen and can lead to serious health problems. Remember what made Erin Brockovich a household name? This type of plating produces several byproducts which are considered hazardous.
Trivalent chromium plating is more environmentally friendly than hexavalent chromium; the electrodeposition process is generally accepted to be more than 500 times less toxic than hexavalent Chromium. The major benefit of trivalent chromium processes is that it is more versatile. Plating distribution is more uniform, barrel plating is possible for trivalent chrome, which is not possible with hexavalent chrome.
We are here at this point of our discussion because Environmental considerations and the health and safety of people are at stake. International regulations have made us rethink our way of doing business. So, Hex versus Tri?
We have no choice in the matter. The challenge here is to make trivalent chromium plating as good as, or even better that what we had with hexavalent chrome. Our job at PAVCO is working to make this a reality, contact us!
Table comparing some properties of Hexavalent and Trivalent Chromium
Hexavalent Chromium | Trivalent Chromium | |
Waste Treatment | Expensive | Easy |
Throwing Power | Poor | Good |
Safety | Very Unsafe | Relatively safe; similar to Nickel |
Tolerance to Contamination | Fairly Good | Not as Good |
NSS and CASS | Similar | Similar |
Resistance to burning | Not Good | Very Good |
IT’S HOW YOU FINISH
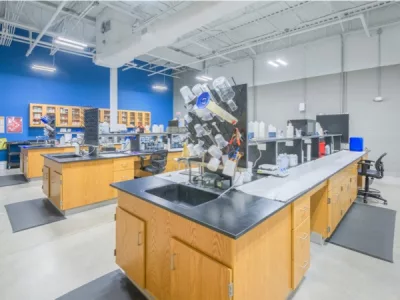
We’re a developer and supplier of chemistries for the metal finishing industry since 1948.
In PAVCO, we develop products and deliver services of the highest quality at a reasonable cost.