Why opt for Acid or Alkaline in Zinc Electroplating?
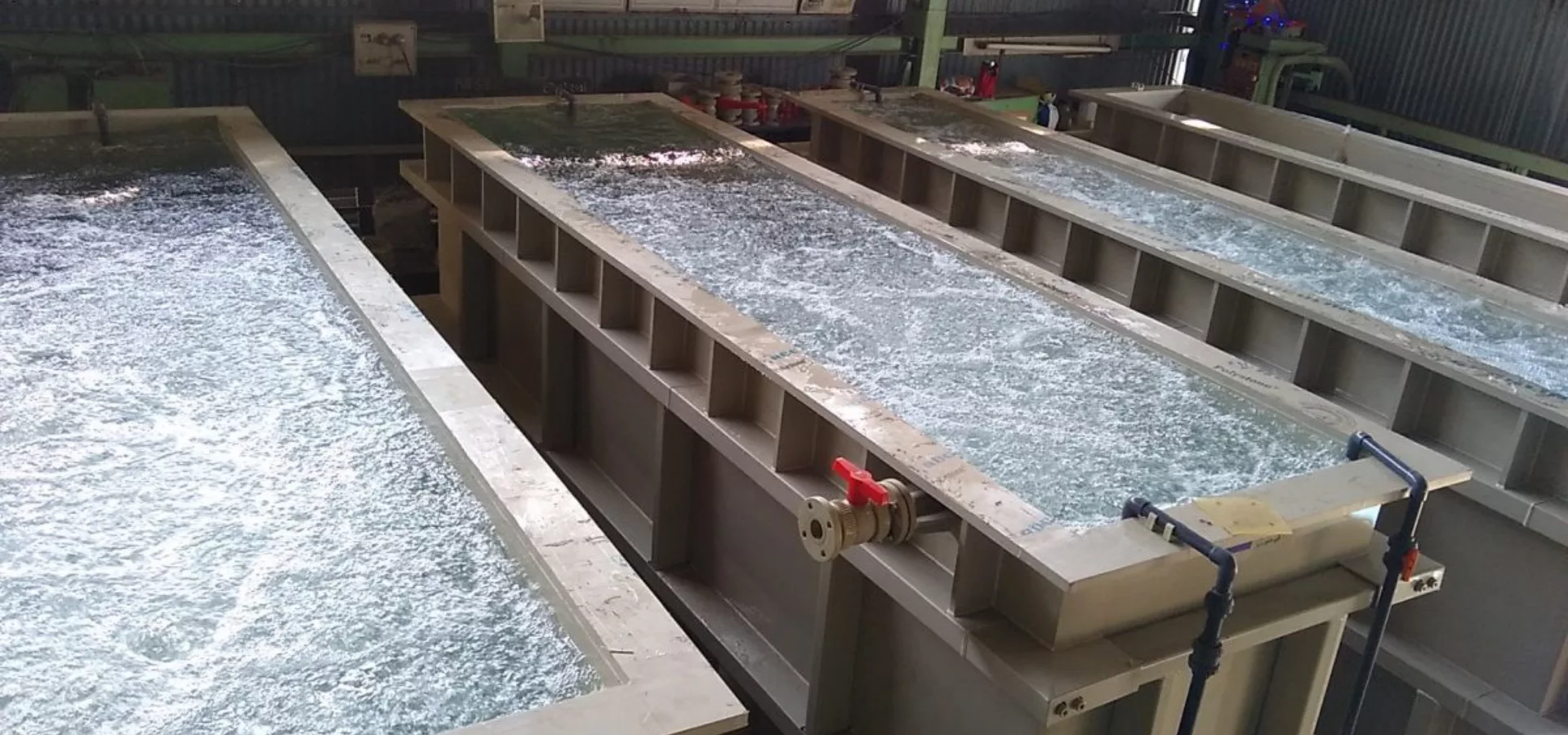
June 18, 2024
June 18, 2024
When we talk about electroplating, zinc dominates as a protective and versatile coating. But when it comes to the electroplating process itself, a crucial decision arises: an acid or alkaline bath?
Both methods offer distinct advantages, and understanding these differences is key to achieving optimal results.
Acid vs. Alkaline: Main differences
The primary difference between acid and alkaline zinc plating lies in the chemical composition of the electrolyte solution.
Acid baths, as the name suggests, utilize acidic solutions, typically containing zinc and chloride salts. In contrast, alkaline baths employ a basic or caustic environment with potassium or sodium hydroxide as a key component.
Acid Baths: Speed, Efficiency, and Cost-Effectiveness
For high-volume applications, acid zinc plating holds significant appeal. It offers faster plating, which translates into more production . Additionally, acid baths are known for their high efficiency, meaning less electricity is wasted during the process.
This efficiency makes acid plating a cost-effective choice. The resulting zinc deposits often have a brighter appearance, which can be desirable for certain applications.
However, there's a flip side to the coin. Acid solutions are inherently corrosive, requiring careful handling and disposal. Furthermore, acid baths exhibit poorer throwing power. This translates to uneven deposition on parts with complex geometries, potentially leading to thinner coverage in recessed areas.
Alkaline Baths: Uniformity and Ductility
When it comes to achieving a uniform and consistent zinc layer, alkaline baths are the clear winner. Their superior throwing power ensures excellent coverage on intricate parts, making them ideal for complex geometries.
Alkaline solutions are also generally less corrosive than their acidic counterparts, contributing to extended life of adjacent equipment and structures.. However, an alkaline zinc solution has a high concentration of sodium hydroxide, making it corrosive to human tissue. Additionally, the zinc deposits obtained through alkaline plating often exhibit superior ductility, making them more resistant to cracking or peeling.
However, there are trade-offs associated with alkaline baths. The plating rate is generally slower compared to acid baths, and the process can be slightly more expensive. The resulting zinc deposits may have a duller appearance compared to those achieved with acid plating.
Tailoring the Process to Your Needs
The selection between acid and alkaline zinc plating hinges on several key considerations:
Application Requirements: Is corrosion resistance, a bright finish, or uniform coverage the primary concern?
Desired Properties: Do you prioritize speed, ductility, or a specific aesthetic?
Part Geometry: Are you dealing with simple or complex shapes?
Cost Considerations: How important are initial setup costs and processing speed?
Environmental and Safety Regulations: Does your workplace have regulations regarding waste disposal or chemical handling?
The role of pH and chemical composition
The pH of the electrolyte solution plays a crucial role in determining the properties of the final zinc deposit.
Acid baths have a lower pH (more acidic), leading to faster plating rates and brighter finishes. Alkaline baths, with a higher pH, promote more uniform deposition and ductility.
The specific chemical composition of the bath, including additives, also influences factors like grain size and brightness of the deposit.
Temperature and Deposition Rate
Temperature plays a part in the plating process as well. Higher temperatures can accelerate the plating rate in both acid and alkaline baths, but they may also affect the quality of the deposit. The desired deposition rate will also influence the choice of bath chemistry and operating conditions.
Navigating the electroplating landscape
With so many factors at play, the ideal electroplating solution depends entirely on your specific project. Don't be overwhelmed by the options!
Here at PAVCO, we offer a comprehensive line of plating technologies, including chemistries for both acid and alkaline baths.
Our technical sales representatives are experts in guiding you through the selection process to ensure you achieve the perfect finish for your needs. Contact us today to discuss your project and explore all the possibilities!
IT’S HOW YOU FINISH
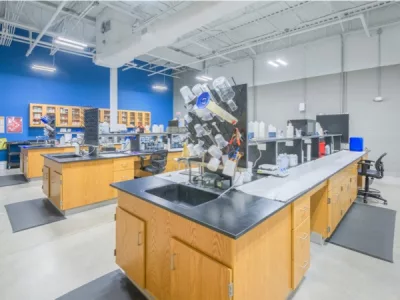
We’re a developer and supplier of chemistries for the metal finishing industry since 1948.
In PAVCO, we develop products and deliver services of the highest quality at a reasonable cost.