Anodizing vs. Electroplating: Coating Techniques unveiled
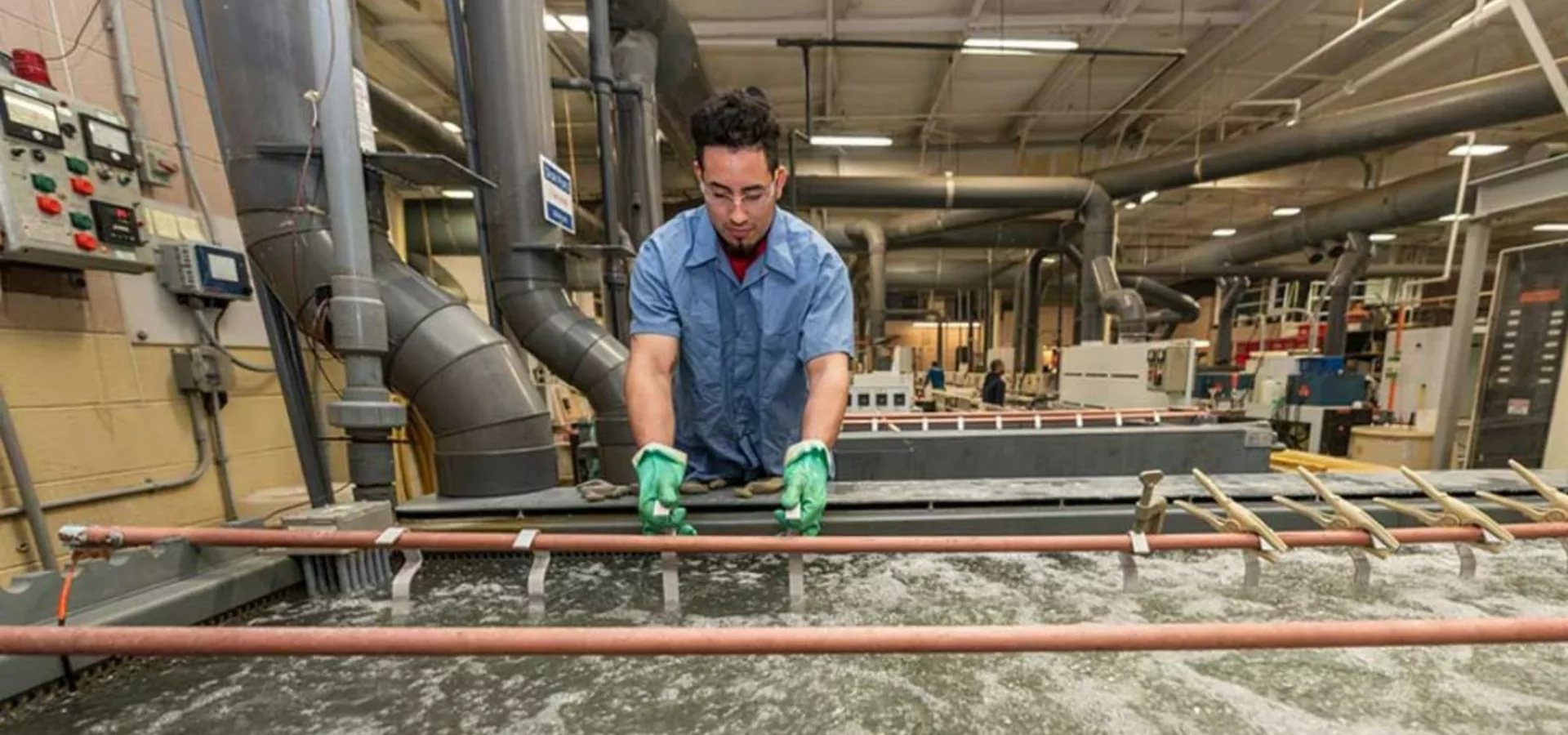
July 09, 2024
July 09, 2024
Ensuring the longevity and functionality of metal components often relies on protective coatings. Two prominent techniques in this realm are anodizing and electroplating. While both enhance metal properties, they operate on distinct principles, making them suitable for different applications.
Let's go into the world of these two coating techniques, exploring their science, benefits, and ideal uses.
Anodizing vs Electroplating
Anodizing
This oxide layer, in the case of aluminum anodizing (the most common type), significantly enhances the metal's durability, corrosion resistance, and wear resistance. Additionally, anodizing offers a wide range of aesthetic possibilities. By controlling the anodizing process, various colors and finishes can be achieved. Although anodizing is most commonly used to aluminum and its alloys, it may also be applied to other nonferrous metals. Stainless steel, magnesium, titanium, manganese, copper, and zinc are a few of them. It's important to recall that anodizing cannot be applied to steel or other iron alloys.
Electroplating
Electroplating, on the other hand, deposits a thin layer of a different metal onto the surface of a base metal. In contrast to anodizing, electroplating utilizes an external source of metal ions.
The base metal acts as the cathode (negative electrode) in a bath containing a solution of the desired plating metal. An electric current drives the positively charged metal ions in the solution to be deposited onto the negatively charged base metal.
Electroplating offers a vast array of metal coatings, each with unique properties. Common choices include nickel for enhanced corrosion resistance, chromium for a gleaming finish and superior hardness, and zinc for excellent protection against rust.
You may be interested in reading: Why opt for Acid or Alkaline in Zinc Electroplating?
Key differences between anodizing and electroplating
While both techniques provide protective coatings, some key distinctions set them apart:
Coating Material: Anodizing utilizes the metal's own oxide layer, while electroplating deposits a new metal layer.
Process: Anodizing is an electrochemical conversion process, while electroplating involves depositing a new metal layer through reduction.
Applications: Anodizing is ideal for enhancing the natural properties of the base metal, often used for aluminum components. Electroplating offers a wider range of functionalities depending on the chosen coating metal.
Which one is better for your project?
Understanding these differences is crucial for selecting the appropriate technique. Here are some industry-specific examples:
Aerospace: Both anodizing and electroplating play roles. Anodizing enhances the corrosion resistance and wear resistance of aluminum aircraft parts. Electroplating with chromium can be used for landing gear components due to its exceptional hardness.
Automotive: Electroplating with chrome offers a gleaming finish and corrosion protection for car parts. Zinc plating safeguards steel components from rust.
Electronics: Electroplating stands out as a superior technique to protect aluminum housings of electronic components. Unlike anodizing, which also offers corrosion protection, electroplating provides greater heat dissipation.
The Final Coat
Anodizing and electroplating are both valuable tools for optimizing metal components.
Selecting the right technique hinges on the desired properties and application. Anodizing excels in enhancing the natural properties of the base metal, while electroplating offers a broader spectrum of functionalities through diverse coating options.
At PAVCO, our innovative plating solutions are tailored to your specific requirements and our extensive post-plating technologies are designed to enhance the durability and performance of your coated components, ensuring they meet the highest standards.
Reach out to us today to discover how we can elevate your metal finishing processes to new heights of excellence and sustainability.
IT’S HOW YOU FINISH
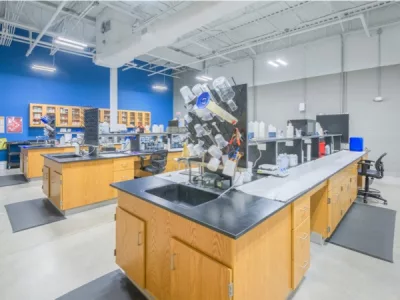
We’re a developer and supplier of chemistries for the metal finishing industry since 1948.
In PAVCO, we develop products and deliver services of the highest quality at a reasonable cost.