Understand nickel plating: Electrolytic and Electroless methods
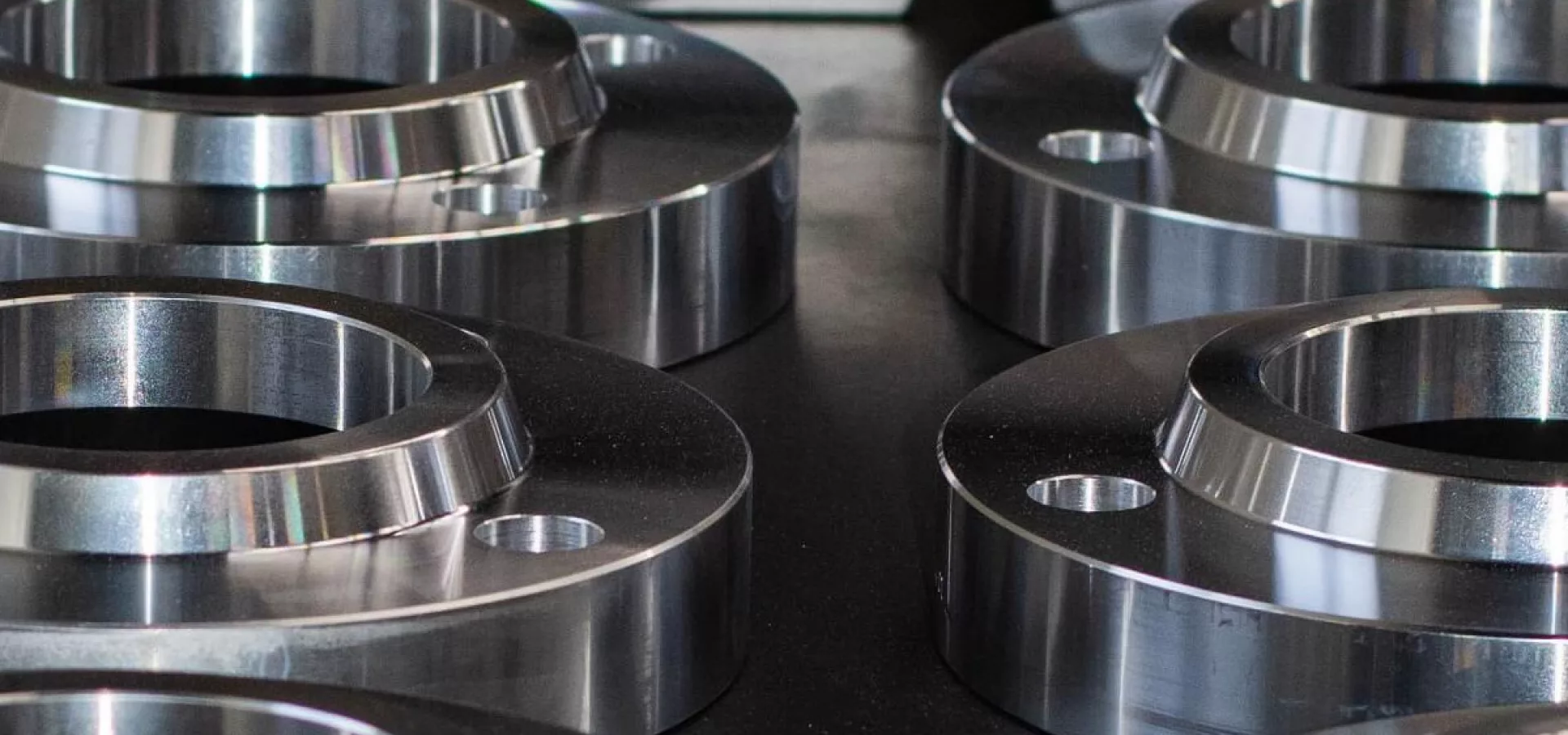
August 14, 2024
August 14, 2024
Nickel plating is a versatile process used across various industries due to its durability and corrosion resistance. Common applications include the automotive industry for parts like fuel systems and brake systems, aerospace for aircraft components, and electronics for connectors and contacts. It's also utilized in the oil and gas sector, as well as in food processing and packaging equipment due to its safe and resilient properties. Nickel plating ensures that machinery and components can withstand harsh environments and extend their service life, making it a critical process in manufacturing and engineering.
In this blog post, we'll explore the distinctions between electrolytic and electroless nickel plating techniques and explore their processes, advantages, and how to choose between them.
What is Nickel Electroplating?
Nickel electroplating is a technique where a thin layer of nickel is deposited onto the surface of an object through an electrochemical process. The electroplating process involves several key steps:
Surface Preparation: The object to be plated is thoroughly cleaned to remove any dirt, grease, or oxidation.
Electrolyte Solution: The object is immersed in an electrolyte solution containing nickel salts.
Electrochemical Reaction: An electric current is passed through the solution, causing nickel ions to migrate and deposit onto the object's surface.
Benefits of Nickel Electroplating
Nickel electroplating offers numerous benefits:
Corrosion Resistance: Nickel plating provides a protective barrier against corrosion, extending the lifespan of the object.
Aesthetic Appeal: The shiny, reflective finish of bright nickel plating enhances the object's appearance.
Wear Resistance: Nickel plating increases the hardness and wear resistance of the surface, making it more durable.
Adhesion: It improves the adhesion of subsequent coatings, such as chrome or paint.
Types of Nickel Electroplating
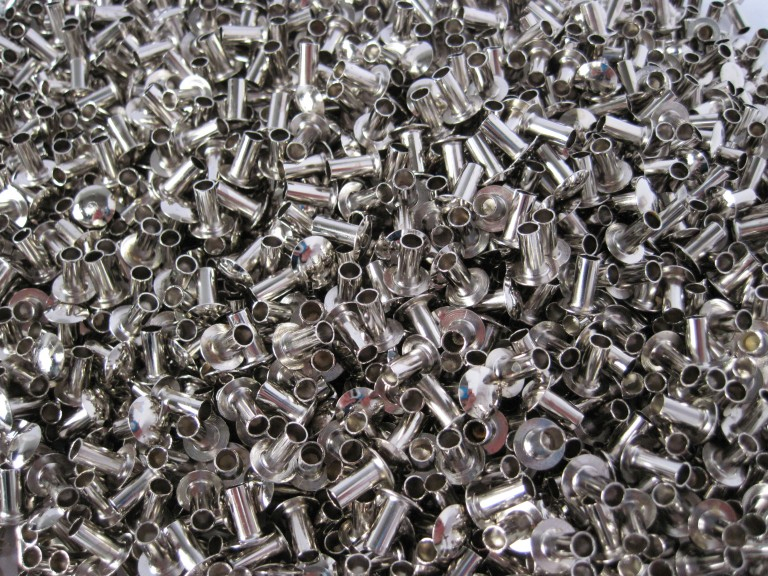
Nickel electroplating comes in several types, each with its unique properties and applications:
Semi-Bright nickel
Semi-bright nickel offers a smooth, matte finish. It's often used as an undercoat for other layers of Ni of plating, providing excellent corrosion resistance and ductility.
Bright nickel
Bright nickel plating, as the name suggests, provides a shiny, reflective finish. It's commonly used in decorative applications, such as automotive trim and household fixtures.
Microporous nickel
Microporous nickel plating involves creating tiny pores in the nickel layer. This type of plating is used to improve the adhesion of subsequent coatings, such as chrome, and enhance corrosion resistance.
What is Electroless nickel plating?
Electroless nickel plating is a chemical process that deposits a uniform layer of nickel-phosphorus alloy onto the surface of an object without using electricity. This method is known for its ability to coat complex shapes and provide a consistent thickness.
The electroless plating process involves the following steps:
Surface Preparation: Similar to electroplating, the object is cleaned to remove contaminants.
Chemical Bath: The object is immersed in a chemical bath containing nickel salts and a reducing agent.
Chemical Reaction: A chemical reaction occurs, causing nickel to deposit onto the object's surface uniformly.
Benefits of Electroless nickel plating
Electroless nickel plating offers several advantages:
Uniform Coating: The process provides a consistent thickness, even on complex shapes and internal surfaces.
Corrosion Resistance: The nickel-phosphorus alloy offers excellent corrosion resistance.
Hardness: Electroless nickel plating increases the hardness of the surface, enhancing wear resistance.
No Electricity Required: The process does not require an electric current, making it suitable for coating non-conductive materials.
How to choose between electroplating and electroless plating?
Choosing between electrolytic and electroless nickel plating depends on several factors:
Object shape and complexity
Electroplating: Best for objects with simple shapes and external surfaces.
Electroless Plating: Ideal for complex shapes, internal surfaces, and non-conductive materials.
Desired coating properties
Electroplating: Offers a shiny, reflective finish and is suitable for decorative applications.
Electroless Plating: Provides a uniform coating with excellent corrosion resistance and hardness.
Cost considerations
Electroplating: Generally more cost-effective for large-scale production.
Electroless Plating: May be more expensive but offers superior coating uniformity and versatility.
Application requirements
Electroplating: Suitable for applications where aesthetic appeal and adhesion of subsequent coatings are important.
Electroless Plating: Ideal for applications requiring uniform thickness, corrosion resistance, and hardness.
Elevate your operations with Pavco's solutions
Pavco’s Nickel electroplating solutions are engineered to meet the specific needs of our clients, enhancing productivity, consistency, and longevity. Contact us today to discover how our innovative solutions can drive your success and elevate your operations.
IT’S HOW YOU FINISH
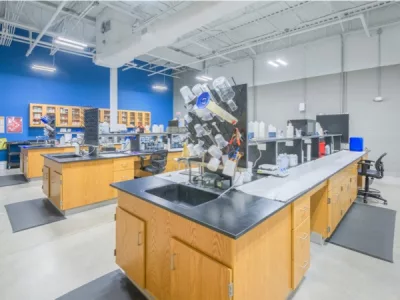
We’re a developer and supplier of chemistries for the metal finishing industry since 1948.
In PAVCO, we develop products and deliver services of the highest quality at a reasonable cost.