Plating Automation: Enhance Quality and Reduce Production Time
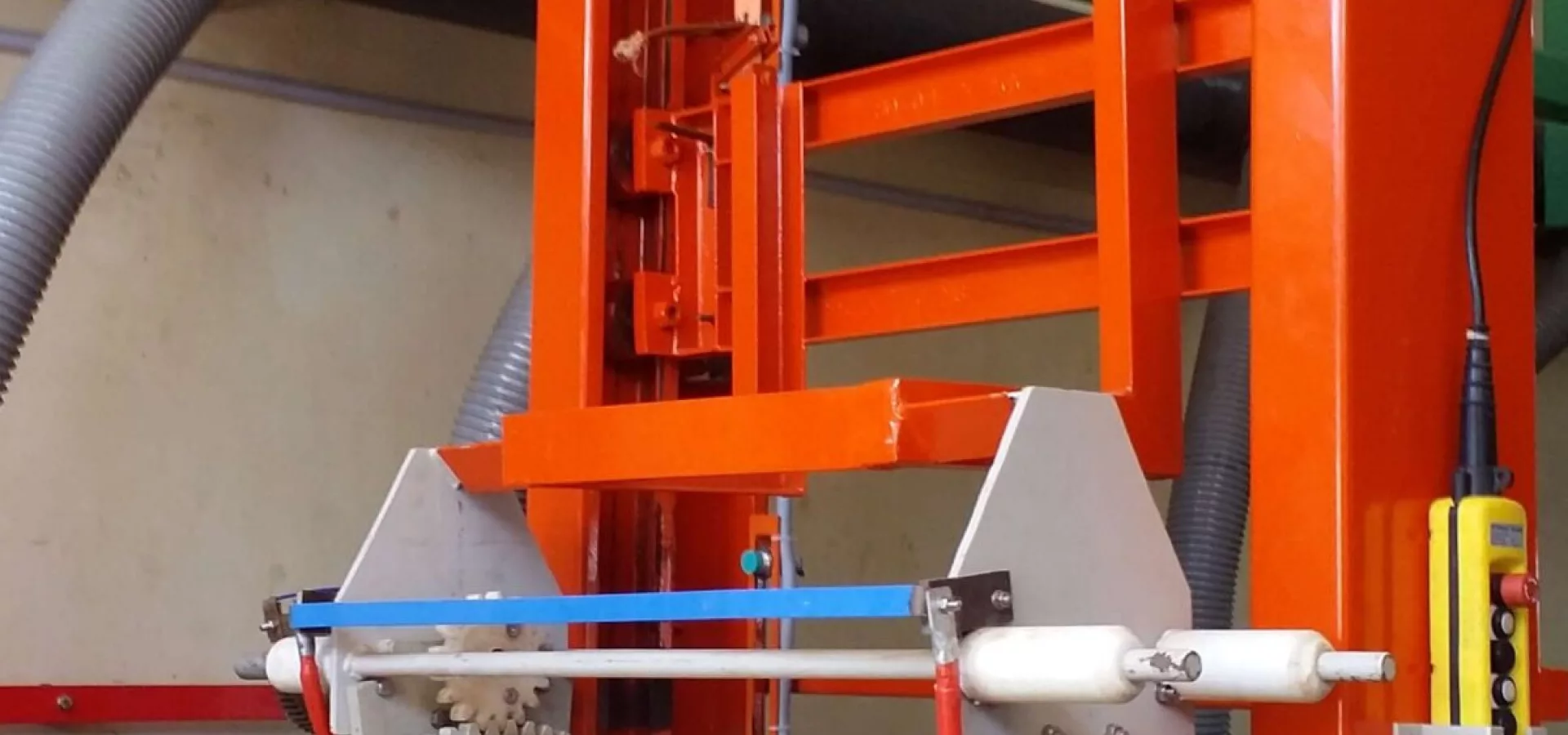
October 08, 2024
October 08, 2024
In the rapidly evolving landscape of industrial manufacturing, automation has emerged as a transformative force, particularly in the realm of plating operations. Plating automation is revolutionizing traditional methods by enhancing efficiency, precision, and safety. In this blog post we will discuss how automation improves plating lines by ensuring consistent quality through precise control and real-time monitoring. Which in turn boosts production with fast continuous operations, reducing errors and part rejection, thereby enhancing overall productivity and profitability.
The Evolution of Plating Automation
Plating, a process of depositing a thin layer of metal onto a conductive surface, has been utilized for centuries to enhance the durability, appearance, and functionality of products across industries.
Traditionally, electroplating involved manual labor and complex machinery, leading to challenges such as inconsistent plating thickness, high error rates, and safety hazards. The incorporation of automated technologies in electroplating lines has significantly transformed operational efficiency and reliability.
Ensuring Consistent Quality
One of the primary benefits of plating automation is the ability to ensure consistent quality through precise control and real-time monitoring. Automated systems streamline the plating process by reducing human intervention, minimizing errors, and ensuring consistent quality output. From loading and unloading parts to controlling chemical dosages and monitoring parameters, automation optimizes every stage of electroplating, leading to higher throughput and cost savings.
Boosting Production and Reducing Errors
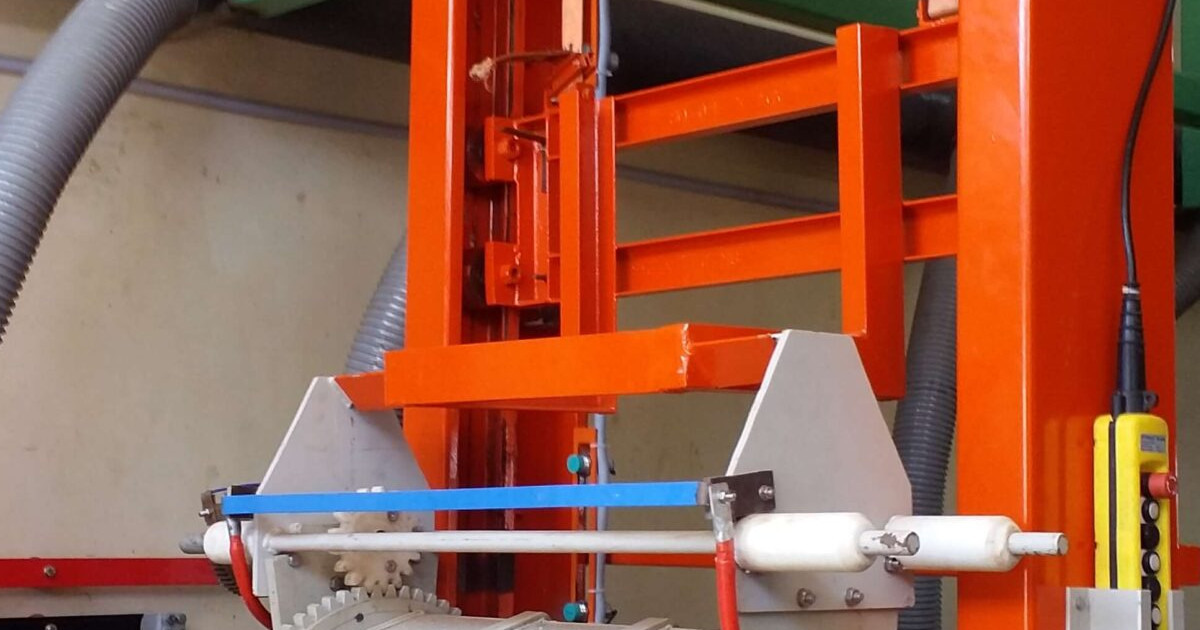
Automation significantly boosts production by enabling faster, continuous operations. Automated systems are often chosen for better plating productivity, allowing people to maintain high work output despite having small teams. Reaching higher speeds is especially advantageous when the material requiring plating is on a large item, such as a wind turbine blades.
Moreover, automation reduces errors and part rejection, which enhances overall productivity and profitability. For example, integrating automation with Pavco’s plating technologies not only improves bath stability but also reduces the environmental impact, ensuring both high-quality output and compliance with industry standards.
Enhancing Safety and Ergonomics
Automated plating systems also relieve people from spending too much time in positions that eventually strain the body. Even if a process still requires some manual steps, machines could offer a more ergonomic option for workers. Automation can also reduce the overall number of people required to do a task without causing fatigue in the workforce. For example, one manufacturer needed more than a dozen workers overseeing four to five machines before investing in automation. Now, one or two people can do the same job.
Economic and Competitive Advantages
The move towards automation has a significant impact on the industry as a whole, affecting employment, productivity, and the ability to compete globally. Automation is vital if the U.S. finishing industry wants to compete at an international level. The sheer amount of cheap manpower available to Chinese finishers allows them to produce large volumes of product. Recent years have seen an increase in wages in China, causing a shift within the industry to automation.
Future Trends and Outlook
As technology continues to advance, the future of electroplating holds even greater promise. Anticipated developments include enhanced AI-driven process optimization (IoT for real-time monitoring) and predictive maintenance, and further miniaturization of robotic systems for micro-scale plating applications. Moreover, collaborative robots (cobots) are expected to play a more prominent role, working alongside human operators to maximize efficiency and flexibility in electroplating operations.
A Future Driven by Automation and Innovation
In conclusion, plating automation is not just a trend but a strategic imperative for modern electroplating facilities. By harnessing the power of advanced technologies, manufacturers can unlock new levels of productivity, quality, and competitiveness in an increasingly demanding market landscape.
For those looking to stay ahead, integrating solutions like Pavco's high-performance chemistries for zinc, nickel, zinc alloys and trivalent- chrome plating will not only streamline processes but also enhance product durability and appearance, while maintaining environmental compliance.
IT’S HOW YOU FINISH
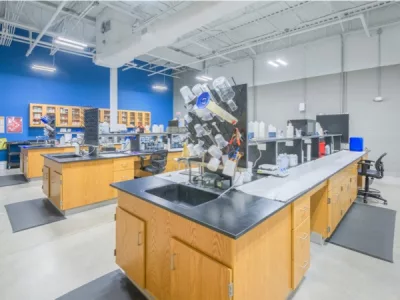
We’re a developer and supplier of chemistries for the metal finishing industry since 1948.
In PAVCO, we develop products and deliver services of the highest quality at a reasonable cost.