Zinc Plating: Enhancing the service life of metal components
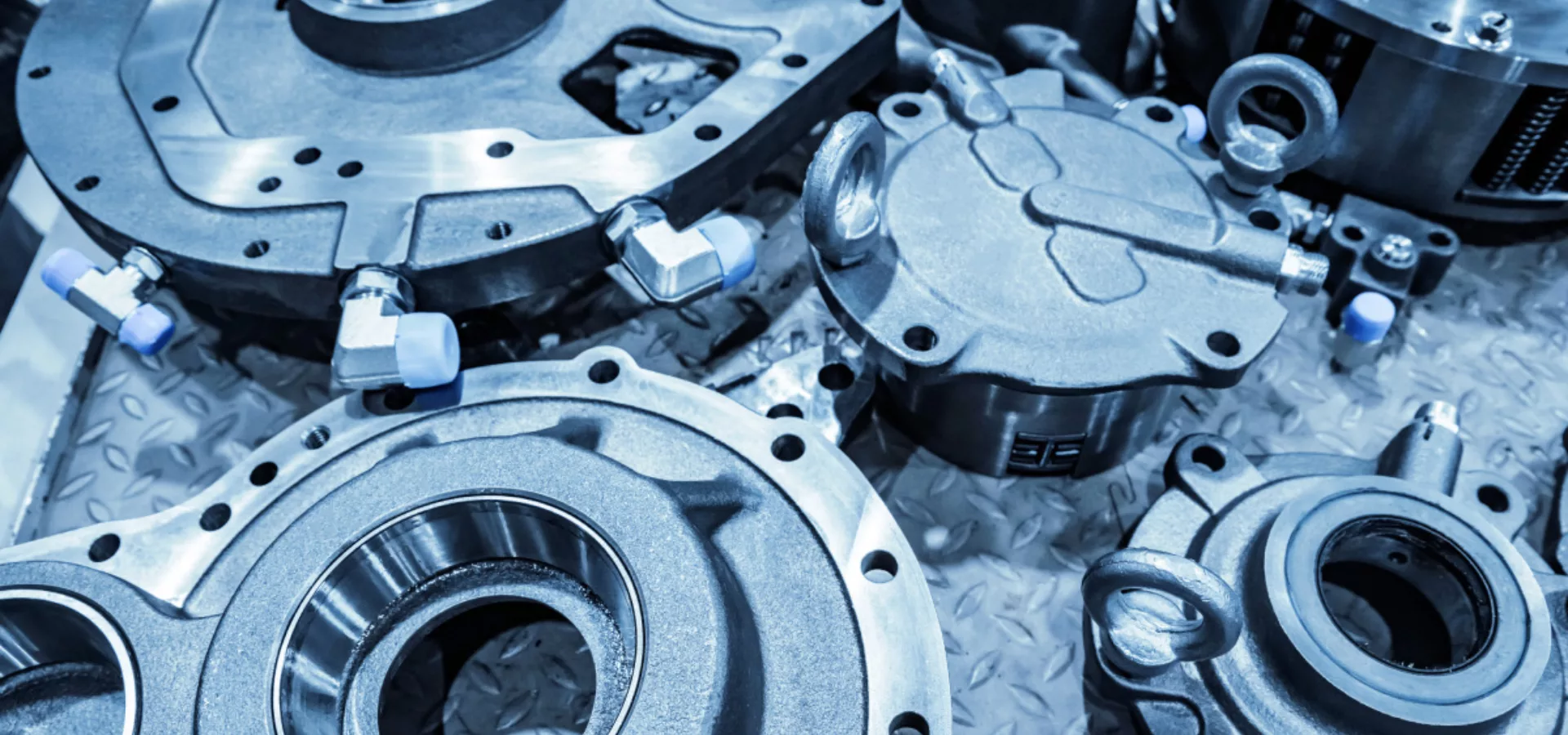
April 30, 2024
April 30, 2024
When battling against rust and corrosion, metal components often need an extra layer of protection. Zinc plating emerges as a champion in this fight. This well-established metal finishing technique is like a suit of armor for your metal components, significantly enhancing their longevity.
What is zinc plating?
Zinc plating is a well-established metal finishing technique that significantly enhances the longevity of metal components. It works like magic, but the science behind it is quite fascinating.
Imagine an electrolytic bath filled with a zinc-rich solution. The object to be plated (the cathode) and a zinc anode are submerged in this bath. When an electric current is applied, zinc ions from the anode dissolve and travel through the solution. These tiny charged particles are attracted to the cathode (the object being plated) where they are deposited as a thin layer of pure zinc.
By carefully controlling the current, time, and solution chemistry, the Zinc plating offers several advantages compared to other corrosion protection methods like painting or lacquering. Here's why it stands out:
Self-sacrificing hero: Zinc acts as a sacrificial layer. When exposed to a corrosive environment, the zinc corrodes preferentially, protecting the underlying metal from rust and deterioration.
Excellent adhesion: Zinc adheres exceptionally well to many common metals, offering a robust and long-lasting barrier against corrosion.
Electroconductive: Unlike paint or some coatings, zinc plating retains electrical conductivity, making it suitable for applications where electrical grounding is crucial.
Cost-effective: Zinc plating is a relatively inexpensive process compared to other advanced corrosion protection techniques.
Zinc Plating for Enhanced Functionality
Zinc plating's magic lies in its sacrificial nature. Here's the science behind it: zinc is more reactive than many common metals used in components.
When exposed to corrosive elements like moisture, salt, or chemicals, zinc corrodes first, forming a protective barrier and preventing the underlying metal from rusting. This sacrificial action effectively extends the lifespan of the protected metal component.
Environmental factors affecting Zinc Plating life
Several environmental factors influence the service life of zinc-plated components:
Humidity and Moisture: High humidity accelerates corrosion. Zinc plating acts as a barrier, but prolonged exposure to moisture can compromise its effectiveness. Regular maintenance and protective coatings are essential.
Temperature Fluctuations: Extreme temperatures impact zinc’s stability. Thermal cycling can cause expansion and contraction, affecting the adhesion of the zinc layer. Properly designed plating systems account for temperature variations.
Chemical Exposure: Exposure to chemicals (acids, alkalis, salts) can corrode zinc. Industries such as automotive, construction, and marine must consider the specific chemicals their components encounter.
How post-treatments improve the performance of zinc plating?
While zinc plating offers excellent corrosion protection on its own, combining it with post-treatments like passivation and topcoating elevates its performance to a whole new level.
Passivation: This process involves treating the zinc plating with a mild chemical solution that creates a thin, invisible film on the surface. This film acts as a barrier, further enhancing corrosion resistance and improving the overall appearance of the plated component.
Topcoating: An additional layer of lacquer, paint, or other protective coating can be applied over the passivated zinc layer. This topcoat provides superior protection against harsh environments, mechanical wear, and UV radiation, making the plated component even more durable and aesthetically pleasing.
By combining zinc plating with these post-treatments, you achieve a synergistic effect, creating a robust and long-lasting protective barrier for your metal components.
Applications of Zinc Plating
Zinc plating finds widespread use due to its exceptional corrosion resistance properties:
Automotive Industry: Fasteners, brackets, and chassis components benefit from zinc plating. It enhances durability, especially in undercarriage parts exposed to road salt and moisture.
Construction: Steel beams, bolts, and nuts used in construction rely on zinc plating. It protects against weathering, ensuring structural integrity.
Marine Equipment: Zinc-coated marine hardware (anchors, chains, fittings) withstands saltwater exposure. The sacrificial protection prevents galvanic corrosion.
Zinc Plating Solutions
We offer a range of cutting-edge zinc plating solutions tailored to diverse needs:
Smart Zinc Premier™: This chloride zinc solution maximizes productivity. It ensures consistent coating quality, even in high-throughput applications. Ideal for industries seeking efficiency without compromising corrosion resistance.
Blaze™ Zinc: A high-performance alkaline zinc, Blaze™ withstands extreme conditions. Its bake-resistant properties make it suitable for applications requiring post-plating heat treatment.
Pavco’s extensive experience in the metal finishing industry benefits customers:
Quality Assurance: Our reputation ensures top-notch quality. Customers can trust the reliability of our zinc plating solutions.
Technical Support: Our experts provide guidance on process optimization, troubleshooting, and best practices. This support streamlines production and maximizes performance.
Feel free to explore our plating technologies for specific details on each product!
IT’S HOW YOU FINISH
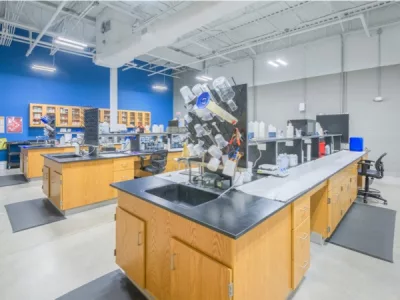
We’re a developer and supplier of chemistries for the metal finishing industry since 1948.
In PAVCO, we develop products and deliver services of the highest quality at a reasonable cost.