Understanding the Interaction of Passivation and Topcoat
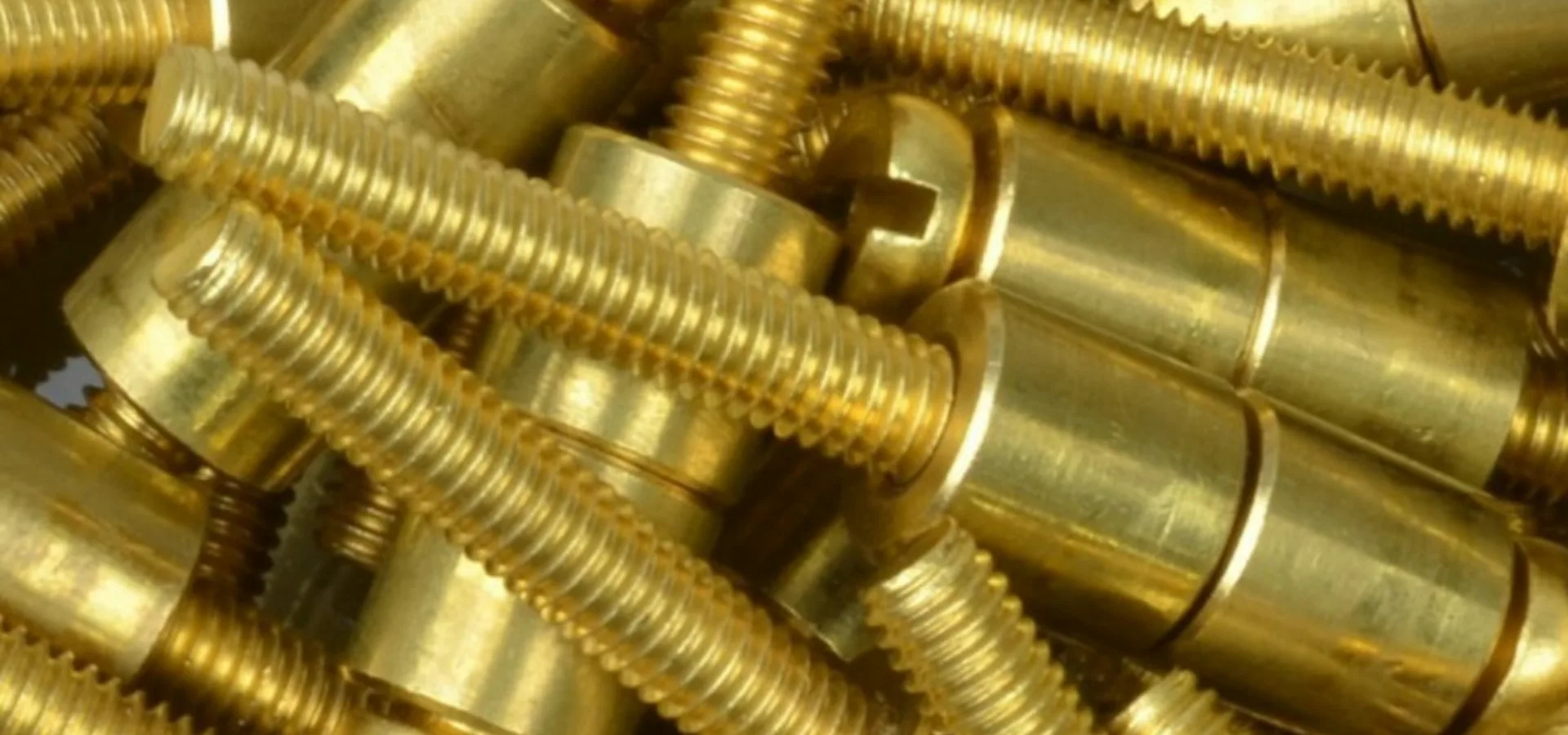
June 18, 2024
June 18, 2024
In the realm of metal surface protection, two powerful tools reign supreme: passivation and topcoats. But their true magic lies not in their individual strengths, but in the remarkable synergy they create when used together.
This blog explores the interaction between passivation and topcoats and how they optimize the durability and aesthetics of metal surfaces.
Passivation: The foundation of protection
Passivation acts as the invisible shield, transforming a metal surface into a more corrosion-resistant form. It achieves this by creating a thin, passive oxide layer on the metal.
The metal is immersed in a carefully formulated solution, often containing acids or oxidizing agents. This mix acts as a catalyst, triggering the oxidation process that transforms the metal's surface.
As the metal interacts with the solution, its surface atoms readily lose electrons, combining with oxygen to form a thin layer of metal oxide.
Remember, passivated surfaces boast enhanced corrosion resistance without significant changes to the underlying metal's mechanical properties. However, on their own, they might lack the robustness needed for harsh environments.
Topcoats take durability to the next level
This is where topcoats come in. Unlike passivation's focus on corrosion resistance, topcoats offer a broader spectrum of protection.
Inorganic or ceramic topcoats significantly enhance wear and heat resistance, ensuring long-lasting performance even in demanding environments.
Some topcoats formulated with lubricants can further improve wear resistance and even provide precise control over friction, making them ideal for fastening applications.
The synergy of passivation and topcoats
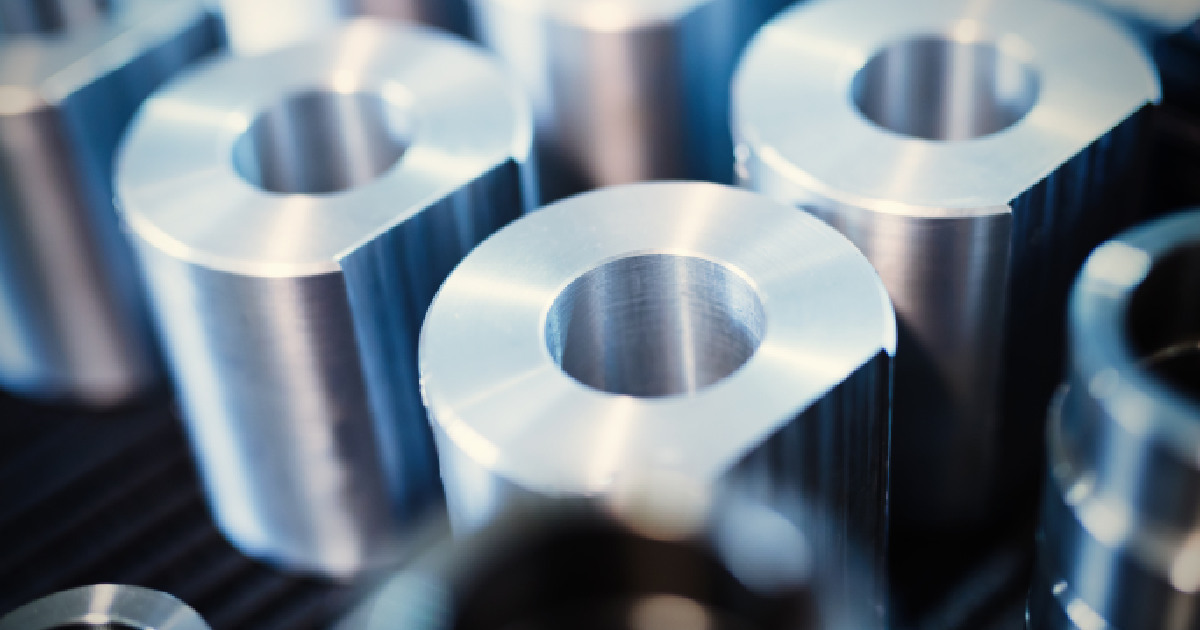
The true brilliance of corrosion protection lies in the synergistic dance between passivation and topcoats.
The passivate layer acts as a meticulously prepared canvas, offering a stable and uniform foundation for the topcoat to adhere to. This strong bond ensures the topcoat's protective properties, like weatherproofing and UV resistance, are maximized. Together, they create a robust shield, significantly enhancing the metal's overall durability.
The type of passivation method used plays a critical role. A poorly formed or uneven layer can be the Achilles' heel of the entire system. This compromised base can lead to weak adhesion between the metal and the topcoat.
Optimizing the process
The key to overcoming these challenges lies in meticulous process optimization. Selecting the appropriate passivation method based on the metal type and intended application is crucial.
Additionally, ensuring proper control of variables like solution composition, immersion time, pH, temperature, and surface preparation techniques is paramount. By carefully optimizing each step, we can create a robust and uniform passive layer that provides the perfect foundation for a strong topcoat bond, leading to superior long-term corrosion protection for the metal.
Responsible use of surface treatments
Both passivation and topcoats involve the use of chemicals. It's crucial to prioritize environmentally friendly options and adhere to proper disposal regulations. Additionally, safety precautions should always be followed when handling these materials.
How to choose the perfect match?
Choosing the right passivation and topcoat combination, depends entirely on the specific metal substrate. Several factors play a crucial role in this decision, including the type of metal, the desired level of corrosion and wear resistance, and the final aesthetic requirements. Understanding these factors ensures optimal performance and a visually appealing finish.
PAVCO offers a comprehensive line of trivalent passivates, line. come in a variety of finishes that can be paired with PAVCO's HyProCoat™ series of topcoats to create a customized solution for your specific needs.
Don't settle for anything less than the perfect match.Explore our full range of solutions, and unlock the full potential of your plating process. .
IT’S HOW YOU FINISH
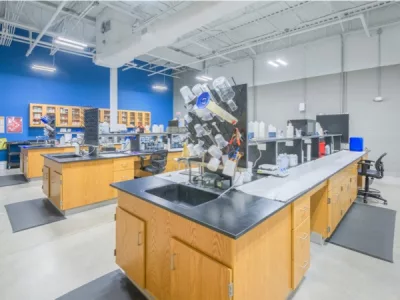
We’re a developer and supplier of chemistries for the metal finishing industry since 1948.
In PAVCO, we develop products and deliver services of the highest quality at a reasonable cost.