Hydrophobic Coatings: The ultimate barrier to metal protection
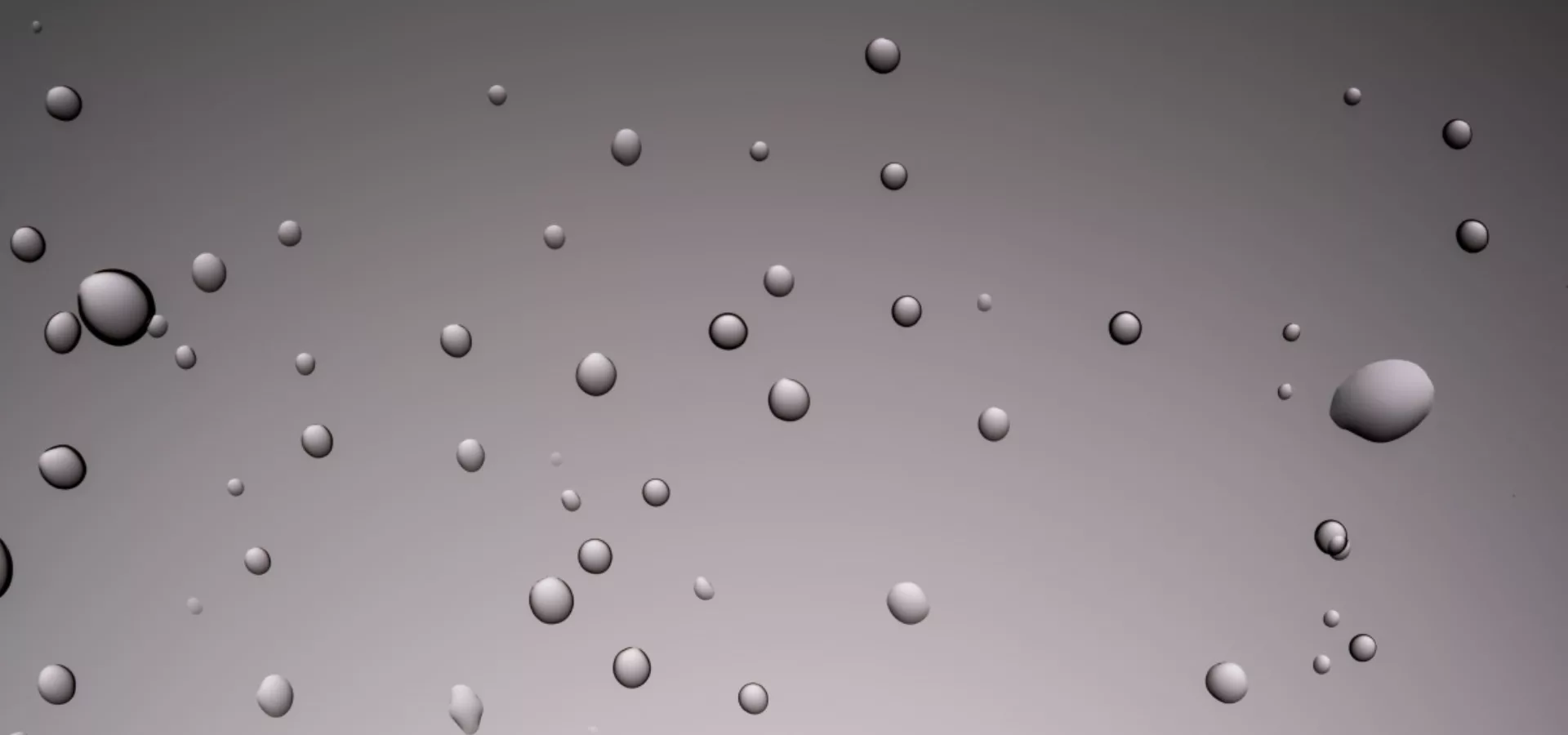
April 30, 2024
April 30, 2024
The pursuit of an effective protection against corrosion and wear has led to the development of a diverse array of surface treatments. Among these, hydrophobic coatings have emerged as a front-runner, offering a remarkable shield for metal surfaces.
To fully grasp the performance of these coatings, let's deepen into their fundamental principles and explore how they safeguard metals from the relentless assault of the environment.
What are hydrophobic coatings, and how do they work?
Hydrophobic coatings, as the name suggests, possess an aversion to water, stemming from their inherently low surface energy.
This unique property manifests at the molecular level, where the coating molecules align in a manner that minimizes the surface area exposed to water. As a result, when water droplets encounter a hydrophobic surface, they are unable to spread and adhere, instead forming beads that easily roll off.
Surface Tension: The driving force behind Hydrophobic Coatings
The interplay between surface tension and hydrophobic coatings is crucial in understanding their effectiveness. Surface tension, the cohesive force that binds liquid molecules together, acts as a measure of a liquid's resistance to deformation. In the case of water, its relatively high surface tension causes it to form beads on hydrophobic surfaces.
When a water droplet lands on a hydrophobic coating, the water molecules experience a stronger attraction to each other than they do to the coating molecules. This cohesive force pulls the water molecules together, forming a compact bead that minimizes the surface area in contact with the coating. As a result, the bead remains spherical and rolls off the surface with minimal resistance.
How do hydrophobic coatings prevent corrosion?
Corrosion, the gradual deterioration of metals as a result of chemical reactions with their environment, is a major threat to the longevity and integrity of metal components. Hydrophobic coatings, with their ability to repel water and moisture, act as a formidable barrier against corrosion by minimizing the contact between the metal surface and corrosive agents.
The effectiveness of hydrophobic coatings in preventing corrosion is evident in various applications, from industrial machinery and equipment to construction materials and automotive components.
Can hydrophobic coatings extend the lifespan of metal components?
The short answer to this question is a resounding yes. Hydrophobic coatings, by effectively preventing corrosion, contribute significantly to extending the lifespan of metal components.
Hydrophobic coatings act as a protective shield, safeguarding metal surfaces from the corrosive action of water, moisture, and other harmful substances. By minimizing the interaction between the metal and its environment, these coatings effectively slow down the corrosion process, extending the useful life of metal components.
Hydrophobic coatings advantages
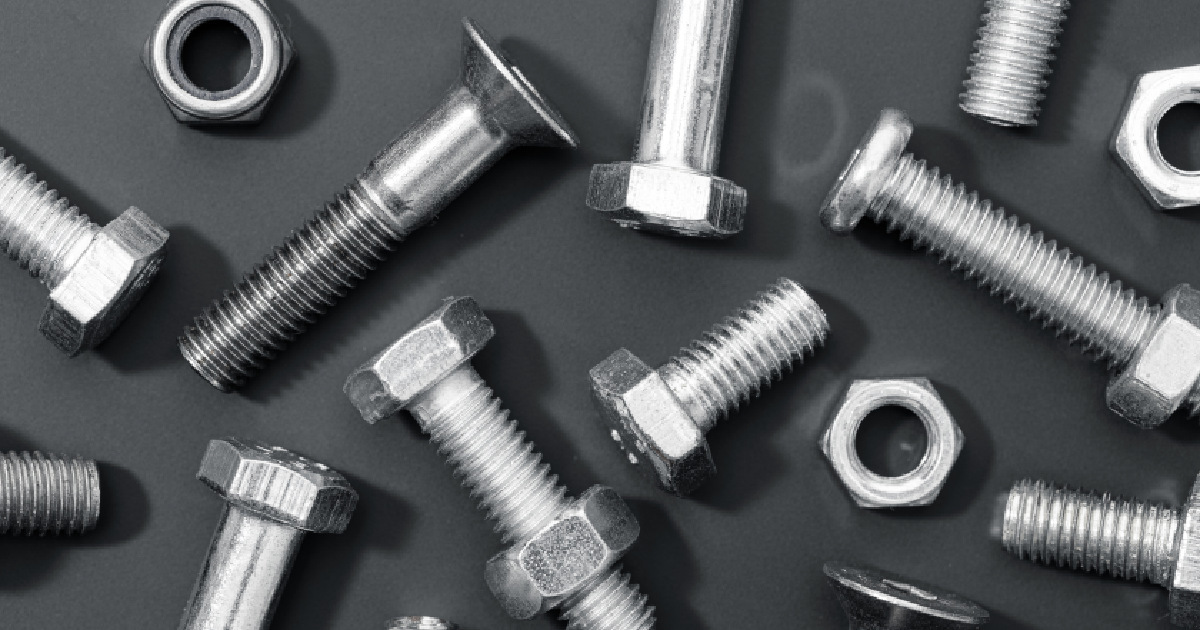
The benefits of hydrophobic coatings extend beyond their exceptional corrosion-fighting abilities. These versatile coatings offer a range of additional advantages that enhance the performance and functionality of metal components.
One notable benefit is friction reduction. Hydrophobic coatings, with their smooth, low-surface-energy surfaces, can minimize friction between moving metal parts, leading to smoother operation, reduced wear and tear, and improved energy efficiency.
Hydrophobic coatings also exhibit self-cleaning properties. Their ability to repel water and other liquids prevents dirt, debris, and contaminants from adhering to the metal surface. This self-cleaning effect reduces the need for frequent cleaning and maintenance, saving time and labor costs.
Furthermore, hydrophobic coatings can enhance the electrical insulation properties of metals. By preventing moisture from forming conductive pathways, these coatings can protect electrical components from short circuits.
PAVCO's Hydrophobic Coatings for exceptional metal finishing
Hydrophobic coatings have revolutionized the way industries safeguard their metal components from corrosion and wear.
Our range of hydrophobic topcoats offer a comprehensive solution to diverse metal finishing needs. These topcoats not only shield metals from corrosion but also impart a range of beneficial properties, making them an invaluable asset across various industries.
Our portfolio of hydrophobic coatings encompasses a range of formulations, each tailored to address specific metal finishing challenges.
Let's deepen into the unique properties of these topcoats:
HyproCoat™ 318: Versatile, low COF, torque modifier topcoat. Low VOC, self-crosslinking, excellent corrosion resistance and no iridescence on black chromates, interior rust protection, recoatable, tough, flexible coating.
HyproCoat™ 319: Eliminate white haze of black passivates over Zn-Ni, excellent corrosion resistance on Zn-Ni platings, torque modifier, low COF and VOC, interior rust protection.
INS™ 630: pH Insensitive, torque modifier, low COF and VOC, excellent corrosion resistance on clear passivates.
HyproCoat™ 855: Designed to enhance color, add gloss, minimize drip marks, and achieve low COF values.
With a variety of options available, selecting the ideal hydrophobic topcoat can seem daunting. Don't hesitate to contact PAVCO's expert team!
Our knowledgeable representatives can guide you through the selection process, ensuring you choose the perfect topcoat to meet your specific needs and achieve optimal metal protection.
Contact us today and discover how we can elevate your metal finishing process.
IT’S HOW YOU FINISH
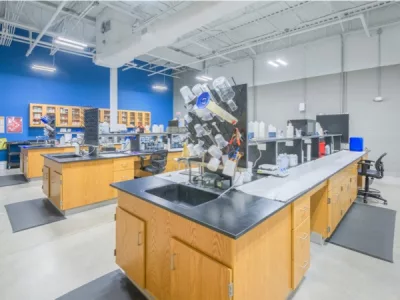
We’re a developer and supplier of chemistries for the metal finishing industry since 1948.
In PAVCO, we develop products and deliver services of the highest quality at a reasonable cost.