Chromating: The ultimate solution for corrosion resistance
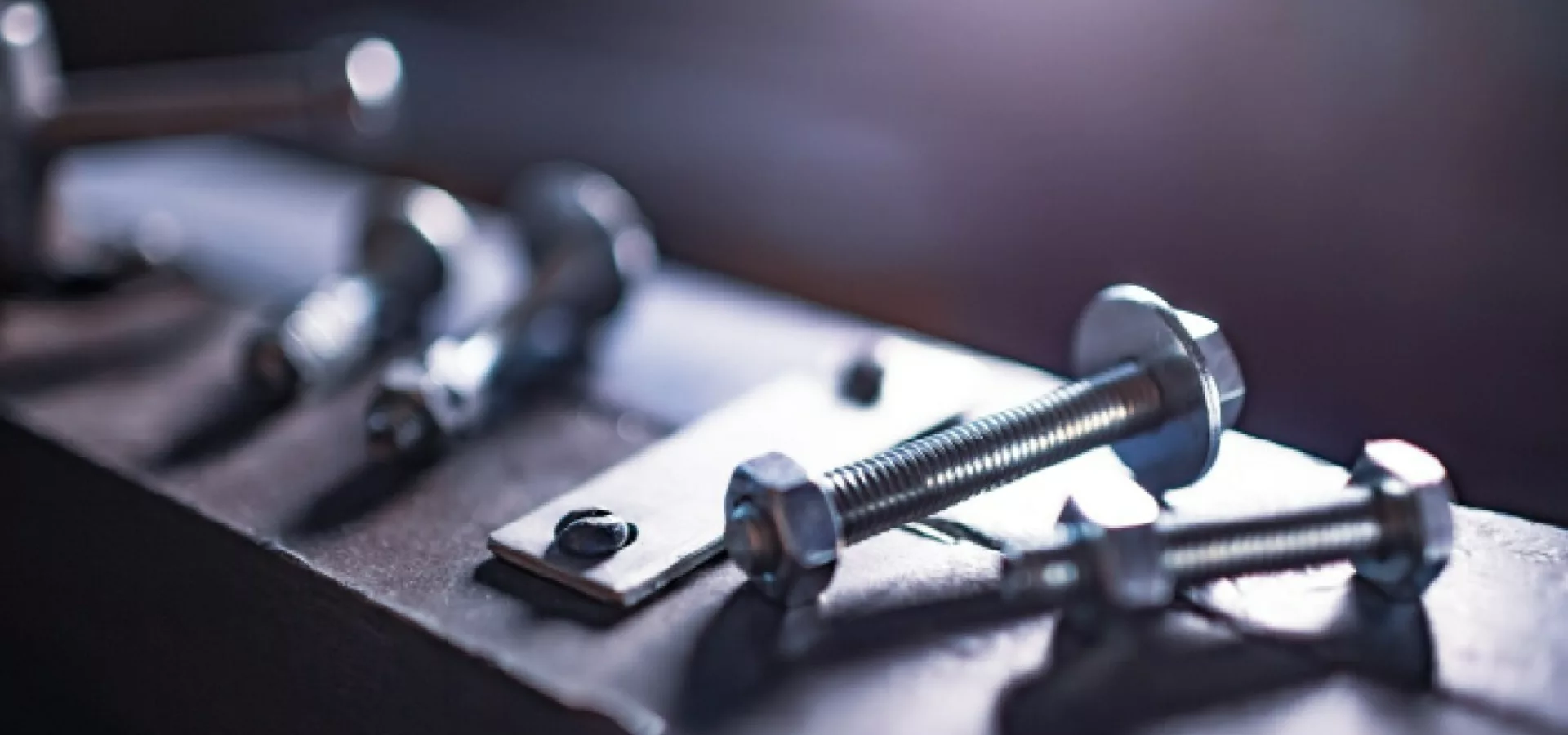
March 20, 2024
March 20, 2024
Corrosion is a natural process that can occur to any metal, and it can be a major problem for industries that rely on metal products. Corrosion can lead to product failure, downtime, and costly repairs.
In this blog post, we will take an in-depth look at chromating and how this process can prevent corrosion and increase the life of your metal surfaces.
What is chromating?
Chromating is a process that applies a thin layer of chromium hydroxide to a metal surface. This layer protects the metal from corrosion by creating a barrier between the metal and the environment. The chromating process can be used on a variety of metals, including steel, aluminum, and zinc.
Within the electroplating industry, chromating usually refers to hexavalent chromates whilst passivating refers to the incumbent technology, trivalent chromium passivates.
How does chromating work?
This process works by creating a chemical conversion coating on the metal surface. This coating is made up of chromium ions and other chemicals that bond to the metal. The coating creates a barrier that prevents oxygen and water from reaching the metal surface, which prevents corrosion.
Benefits of chromating
There are many benefits, including:
Increased corrosion resistance: Chromating can significantly increase the corrosion resistance of metal products. This can help to extend the life of products and reduce the need for repairs.
Improved appearance: This process can also improve the appearance of metal products. The chromate coating can produce blue, yellow, and black finishes for example.
Increased durability: Chromating can also increase the durability of metal products. The chromium coating makes the metal more resistant to wear and tear. Hexavalent chromating has a self-healing capacity for minor damage to its thin film.
Types of chromating
There are two main types of chromating:
Hexavalent chromium chromating: This type of chromating uses hexavalent chromium, which is a toxic chemical. Hexavalent chromating is no longer as common as it once was due to concerns about its environmental and health impact.
Trivalent chromium chromating: This type of chromating uses trivalent chromium, which is a less toxic chemical. Trivalent chromium chromating or passivating is much more common and an environmentally friendly alternative to hexavalent chromium chromating.
Applications of chromating
Chromating offers a broader range of advantages that extend its applications across various industries:
- Automotive: Chromating safeguards car parts from corrosion, ensuring their longevity and functionality. This extends to components like:
Engine parts: Protecting against fluid leaks due to corrosion.
Electrical components: Corrosion products can alter electrical flow
Decorative elements: Providing a visually appealing and durable finish.
- Aerospace: Crucial aircraft components receive a vital layer of chromating for:
Corrosion resistance: Maintaining structural integrity in harsh environments.
- Construction: Chromating helps prevent corrosion of construction materials, particularly:
Fasteners and hardware: Ensuring long-term structural stability.
Building facades: Enhancing weather resistance and maintaining aesthetic appeal.
Chromating is a proven and effective method for protecting metal products from corrosion. The process is versatile and can be used on a variety of metals. Chromating can also improve the appearance and durability of metal products.
How to choose the right chromating solution
When selecting a chromating solution, it’s important to consider several factors:
Type of Metal: Different metals may require different chromating processes.
Desired Corrosion Resistance: The type of chromating process can influence the level of corrosion resistance.
Environmental Impact: Some chromating processes are more environmentally friendly than others. There are also regulations that prohibit the use of Cr(VI) or Cobalt in some regions as they have been deemed Substances of Very High Concern (SVHC)
We highly recommend our Trivalent chromium conversion coatings. This type of chromium is less toxic than hexavalent chromium, making it a more environmentally friendly option.
They have been widely used in various industries, including automotive, due to their outstanding performance. These conversion coatings are easier to manage in terms of waste treatment and have great resistance to white corrosion.
Choose PAVCO. Choose quality.
IT’S HOW YOU FINISH
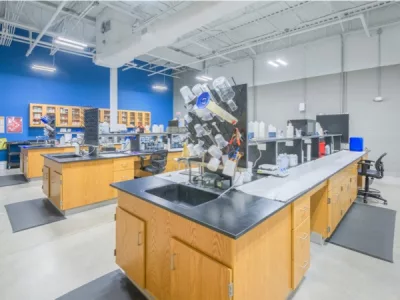
We’re a developer and supplier of chemistries for the metal finishing industry since 1948.
In PAVCO, we develop products and deliver services of the highest quality at a reasonable cost.