Why Are Racks and Hooks Essential for Effective Metal Finishing?
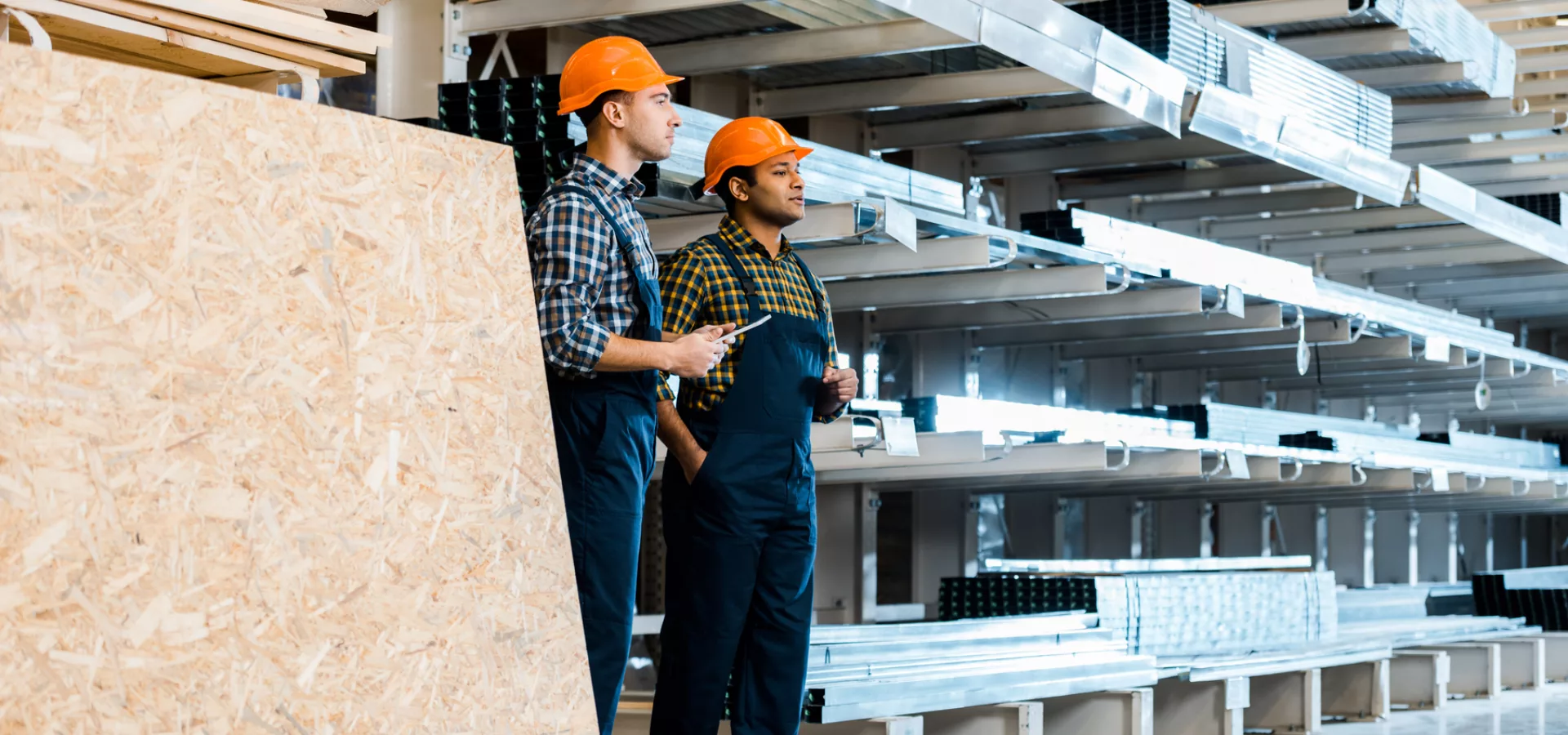
May 03, 2023
May 03, 2023
The visual properties of a coating are the last step in the metal finishing process, and they are the most crucial because they determine the final result that the end customer will see. Customers perceive an aesthetically pleasing finish as an indicator of higher quality.
Racks and hooks are both indispensable for achieving a correct coating. Racks enable parts to be fixed and travel from step to step for an optimal layer and surface treatment, while careful hook design helps with faster and higher quality production.
In this article, we'll explore why both racks and hooks are essential for effective metal finishing and how they can help you achieve professional results that your customers deserve.
Racks for Effective Metal Finishing
Racks are a fundamental element of the metal finishing process, and they can significantly improve the quality of the coatings of metals. The use of adequately insulated racks can decrease the cost of the process due to their superior quality and durability, but this is only true when they are used correctly.
Racks need to be built with solid and conductive materials. Bronze, copper, and steel are the main materials used for this purpose. A correct balance of these three will allow the rack to have rigidity, strength, conductivity, and stay within a budget. A coating commonly known as plastisol is needed to cover these metallic materials, which would deteriorate quickly in a plating line, but would also generate immense costs if they are coated and stripped every time they are used.
The way parts are held on racks can vary from simple or hard-wired to specially designed racks for specific details. The design of the racks can include internal anodes or spring-loaded contacts, depending on the parts' needs.
Achieving the Perfect Finish with the Help of Racks
The load capacity and material used in racks are crucial factors in designing racks. Proper rack design provides stability during the baths, preventing parts from falling, shaking, or coming into contact with each other or any other unwanted surface.
Hooks for Effective Metal Finishing
Hooks are critical to achieving the quality and speed the industry requires in the production line. Simple principles such as desired throughput and the dimensions of both the tanks and the parts can lead to initial hook and rack designs. The competing forces here would be: the maximum number of components in a rack vs. proper spacing required to achieve the coating’s requirements, such as minimum thickness or to avoid parts shading each other.
Equally important as the number of hooks on a rack is the design itself. It must be robust or intricate enough to keep the parts on the rack throughout the plating process. A typical plating process will have big changes in temperature, intense agitation in some stages, and the movement of a hoist transporting the racks from stage to stage.
Likewise, the racks need to be efficient enough for the racking and unracking of the parts. If the people performing this process struggle too much, they will damage both the hooks and parts in the process and be exposed to unnecessary fatigue.
At PAVCO, we can help you achieve excellent finishes. Contact us for more information or a quote. Check out our blog for more expert insights to create better results.
IT’S HOW YOU FINISH
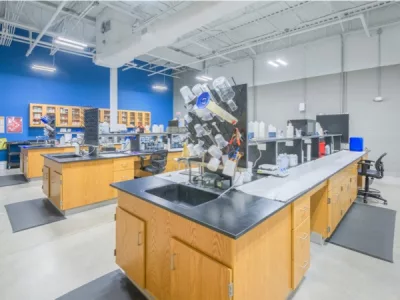
We’re a developer and supplier of chemistries for the metal finishing industry since 1948.
In PAVCO, we develop products and deliver services of the highest quality at a reasonable cost.