Top 10 Troubles in a Functional Plating Shop
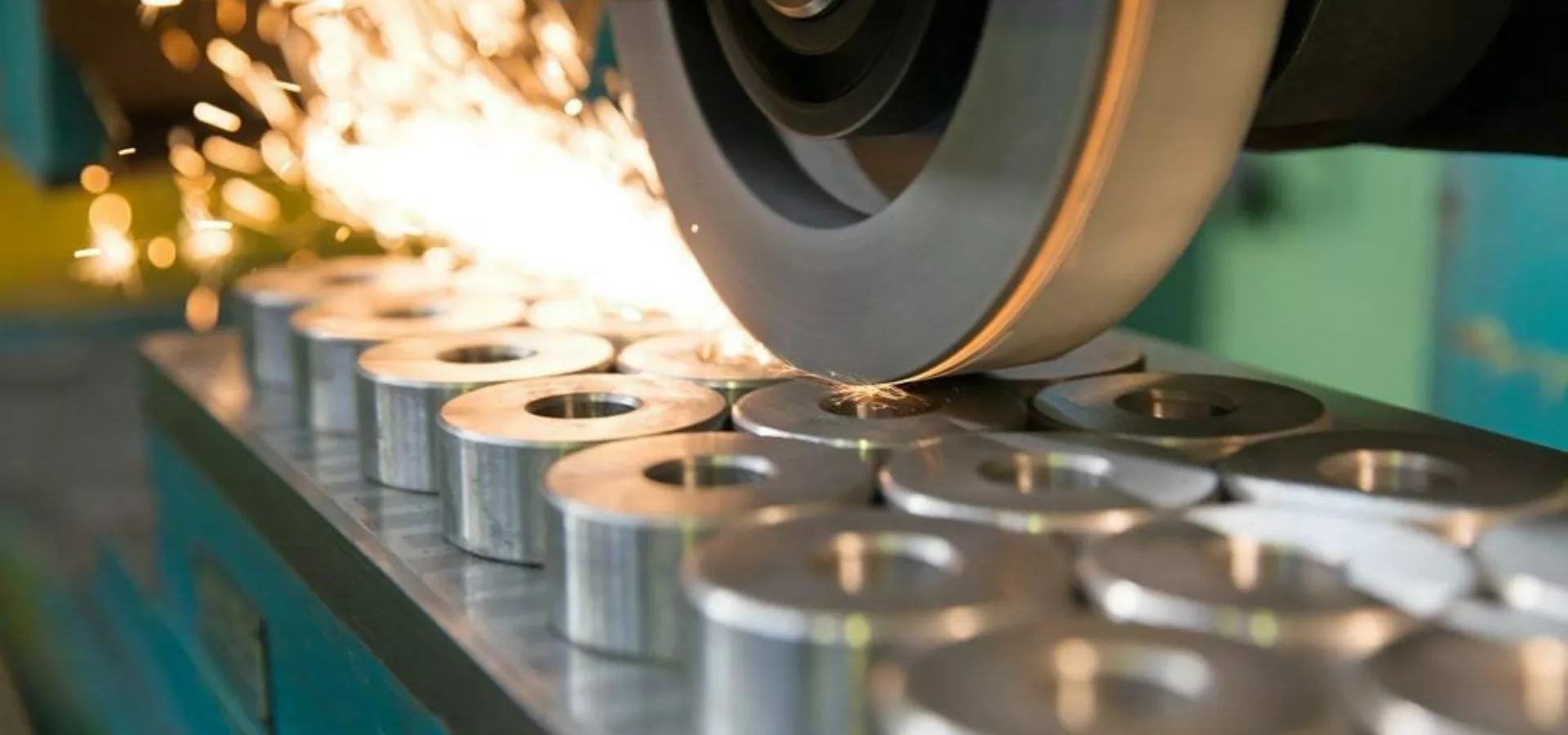
June 23, 2022
June 23, 2022
There is a vast list of things that can go wrong in a typical functional plating process. Most platers find ways to keep that list as short as possible. For now, we are mainly talking about alkaline zinc or zinc nickel, as well as acid zinc or zinc nickel.
PAVCO® has been a leading developer and supplier of chemistries for the metal finishing industry since 1948. Thanks to our experience in the metal finishing industry, it is possible to detect the top 10 problems in a functional plating shop and in honor of David Letterman, we are narrowing the focus to the TOP TEN!
10. Water
It turns out that plating needs rinsing. Staining or contamination of process tanks can be created by insufficient or inconsistent rinse water flow. Use conductivity meters to monitor water quality. Flow volume is an area that modern platers pay much more attention to.
Using enough water but not too much saves you on water cost and wastewater treatment. Water quality is also important. Know your water hardness. Water softening or use of specific ”Water Conditioners” may be recommended depending on the plating process.
9. “The New Guy”
Change in personnel in production or quality can introduce issues. Sometimes this points to insufficient training but other times it can just be that new eyes see different things. Even changes to rackers can influence quality output. Take note of new personnel and the potential influence they may have in your process.
8. Automatic Feeder Gone Haywire / Auditing
Feeders, just like any automated equipment, can simplify process control. The downside occurs when this equipment is not made part of routine line audits. Automated feeders should be checked daily to confirm appropriate feed rates are maintained.
Avoid the Haywire with regular line audits, using a line specific checklist. This should be conducted by trained staff. Leaky lines, clogged check valves, unplugged pumps, empty feed reservoirs can all generate avoidable rejects.
7. Filtration Failures
Filters can be very effective pieces of purification equipment. Or they can just circulate sludge in your process tank. They can be used in process tanks like cleaners to improve longevity and quality.
Care must be taken to inspect equipment and monitor solution quality to ensure the filters are performing properly. Cracked discs and other means of media bypass can cause significant reduction in filtration efficiency making your filter a useless piece of equipment.
6. Poor Record Keeping
This may not sound so exciting, but it is more challenging to identify root sources for failures when there is no information to draw from. Modern line Controllers make data collection for every plating lot possible, with items like process sequence, tank times, current, voltage, all readily tracked.
On lines where this is not possible, much of this should be documented manually. All maintenance and additions should be documented. Line audits mentioned above should be documented and easily accessible.
This makes for a more rapid response when problems arise. We have all heard “Nothing has changed”. This almost always seems true when you have no documented history to review and compare. In plating, the devil is in the details.
5. Bright dip control
The nitric polishing dip, or any other chemical bright dip used after plating is a frequently neglected step. In the case of nitric, it can fix many sins when operating well. It is not uncommon to find lines where this process is not well controlled.
It is possible that the established procedure could be to dump this tank weekly, and avoid process control by just making up a new bath. This can be costly in terms of overall quality, as some lines will see a pH shift here in as little as 1 shift.
Daily, by shift, or continuous monitoring and adjustment by pH is recommended. This is relatively easy to implement and yields a large benefit in terms of uniform brightness. It also improves passivate uniformity in terms of appearance and corrosion performance.
This is especially critical in alkaline zinc and alkaline zinc nickel, where alkaline films must be neutralized.
4. Oil Oil Everywhere
It is easy to imagine oil being an issue on some high production barrel processing lines where you can see oil all the way down the line. With Rack lines, it is easy to be seduced into complacency by one’s gloriously extensive double cleaning cycle.
It is hard to imagine that oil can get past such a cycle. It does. Extensive analytical testing for signature surfactants and oils repeatedly show oils getting into and even past the plating tank even in the most thorough cycle.
Oil skimmers, displacement cleaners, and proper rinsing sequences and techniques can minimize this. Precleaning is a must on some lines, depending on the incoming oil loading and available cleaning time on existing lines.
There are plenty analytical techniques used to monitor contamination, like TOC and cloud point. These can help you understand and react if the inevitable happens. The old “Something Changed”, which could perhaps be a new customer with new oils, tubular work, or blind holes, and suddenly you have oil coming down your line.
This could require an upgraded cleaning process, precleaning, or just a discussion with the customer.
3. Chemical Maintenance
Routine analysis is important to good process control. Having a control plan that identifies critical parameters and monitoring frequencies is a must. Playing loose here will cost you. Using this information is the next step.
Making routine additions based on throughput is preferred to keeping smooth control charts. Use analytical data for small adjustments, and adjust additional volume or schedule based on analytical feedback. Use reliable suppliers to cross check results or perform additional analysis procedures for more extensive analytical control.
2. Racking - Rack Maintenance
Talking about racking in a few sentences is a lost cause. Less than optimal racking is pretty common in job shops, as platers prefer to use “good enough” racks rather than buy new tooling for every job that comes along.
Suitable contacts and part orientation are critical for quality results. Poor rack maintenance can result in deposit buildup on rack tips which may cause contact issues. Cracked rack coatings will cause staining and premature corrosion even with the most thorough rinsing.
Compromised rack coatings also result in plating of the rack, which can add significant cost to your process due to wasted plating and unnecessary stripping. It can also degrade quality, as less plating goes on actual parts.
Modern lines have high bay rinsing to eliminate contamination caused by dried salt building up on carriers. Pay attention to where these systems drain and how they are maintained.
1. pH Measurement
And finally, everyone has their own #1 headache in mind, but we are going with pH. Old pH buffers, fouled pH probes, dead probes, corroded control units, infrequent calibration, temperature compensation, fluoride attack.
We don’t have the space here to go beyond mentioning pH papers. These are all common causes to pH issues in a functional line. Passivates, SmartZinc acid zinc baths, NiClipse acid zinc nickel plating baths, and post plate polishing dips, these all require accurate and regular pH monitoring.
Well established pH procedures for maintenance and use can prevent your supplier from coming into your shop and speaking the unpleasant phrase, “It’s your pH.” The proper response is usually “I’m sorry”.
We have heard these phrases uttered in many languages on many continents. We suspect it won’t move off this list any time soon. If you have your own take on this list, feel free to send us your own version.
Happy plating!
By Matt Stauffer
Business Development Manager, Pavco Europe
mstauffer@pavco.com
IT’S HOW YOU FINISH
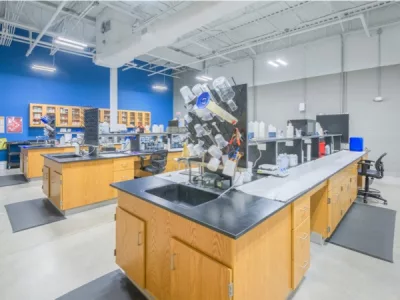
We’re a developer and supplier of chemistries for the metal finishing industry since 1948.
In PAVCO, we develop products and deliver services of the highest quality at a reasonable cost.