Heat Resistant Coatings for High-Temperature Applications
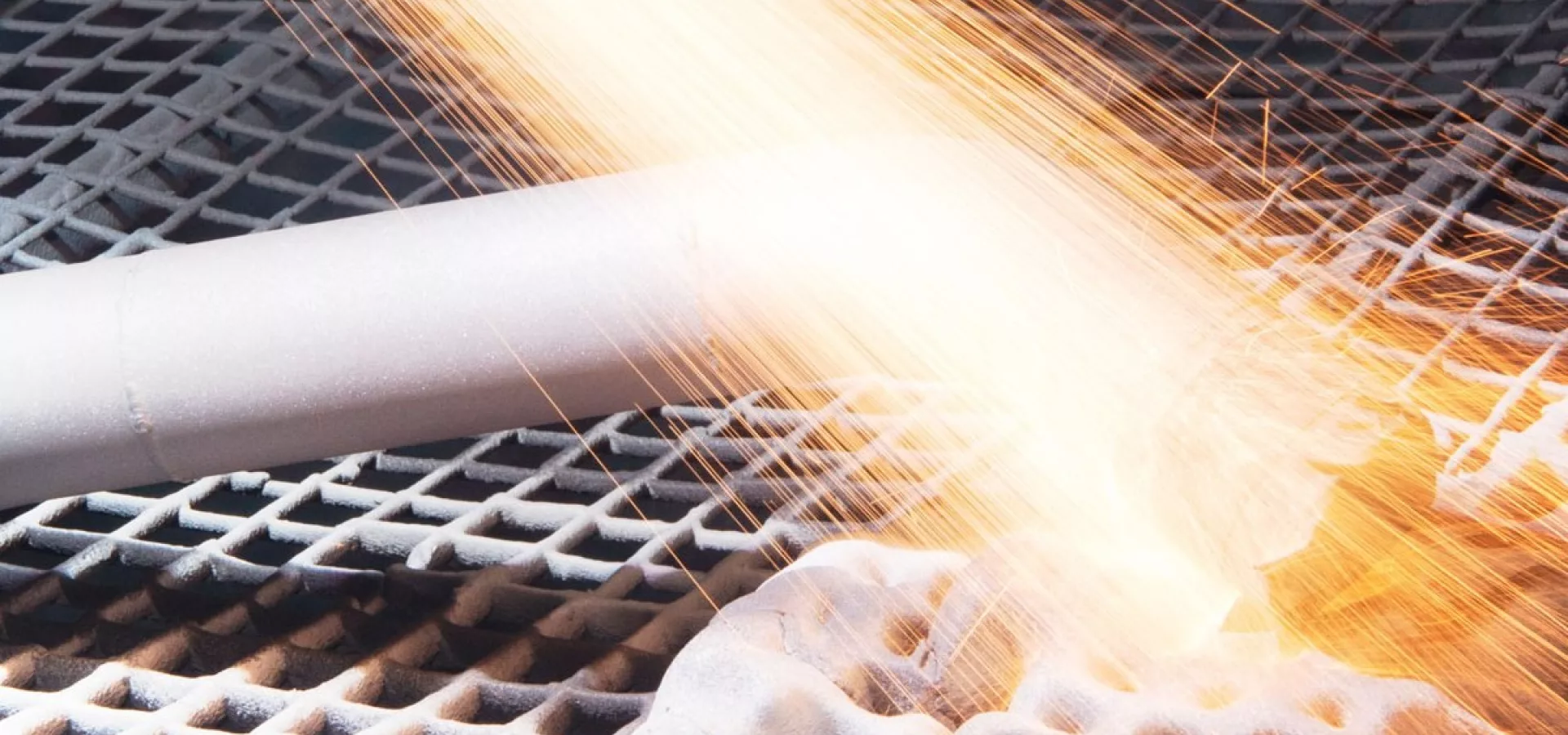
August 14, 2024
August 14, 2024
In the heart of extreme heat, where temperatures soar and metals face their ultimate test, lies a critical need for protection.
Thermal barrier coatings (TBCs) act as shields, guarding against the assault of heat and ensuring the integrity and performance of critical components across industries like aerospace, oil and gas, and automotive.
Understanding the heat of the moment
Imagine a jet engine roaring and its internal components subjected to temperatures exceeding their melting points. Or picture a gas turbine generating power, its blades enduring a continuous onslaught of scorching gases. In these demanding scenarios, heat management isn't just important, it's essential.
That's where heat-resistant coatings come in. These specialized coatings act as thermal insulators, significantly reducing the amount of heat transferred to the underlying substrate. This crucial function allows components to operate reliably at elevated temperatures, extending their lifespan and preventing premature failures.
The anatomy of a thermal barrier coating
TBCs are not your average coatings. They are complex, multi-layered systems engineered for optimal performance under extreme conditions. Typically, a TBC consists of:
A top coat: This outer layer, often composed of ceramic materials and provides the primary thermal insulation.
A bond coat: This metallic layer, usually made of a nickel-based alloy, adheres the top coat to the substrate and enhances its durability.
The substrate: This is the underlying component being protected, which could be a turbine blade or other high-temperature part.
PAVCO's approach to thermal protection
While traditional TBCs rely on thermally grown oxide layers, PAVCO takes a different approach, leveraging our expertise in surface finishing to deliver innovative thermal protection solutions. Our process involves three key steps:
Electrodeposition: We apply a protective metallic layer, such as nickel alloys, to the substrate using electroplating. These alloys are known for their excellent heat resistance, corrosion protection, and wear resistance.
Passivation: We enhance the corrosion resistance of the electrodeposited layer through a chemical passivation process, further reinforcing its protective properties.
Topcoat Application: We apply a final topcoat, tailored to the specific application requirements, to further enhance the thermal insulation and durability of the coating system.
This innovative approach offers several advantages over traditional TBCs:
Increased Versatility: Our process allows for greater flexibility in coating composition and thickness, enabling us to tailor the coating to meet the specific needs of diverse applications.
Enhanced Industrial Friendliness: Our method is more environmentally friendly and cost-effective compared to traditional high-temperature processes.
Improved Adhesion and Durability: Our multi-layered system provides superior adhesion and resistance to thermal cycling and mechanical stresses.
Mastering Heat: PAVCO's Ultimate Thermal Solutions
In the relentless pursuit of efficiency and performance, effective heat management is crucial.
PAVCO's approach to heat-resistant coatings provide a robust and reliable solution, enabling industries to push the boundaries of what's possible in high-temperature environments.
If necessary, PAVCO is also equipped to provide specialized training to your personnel to ensure optimal use and maintenance of these advanced coatings.
Contact us today to learn more about how our innovative coatings can help propel you ahead and elevate your operations.
IT’S HOW YOU FINISH
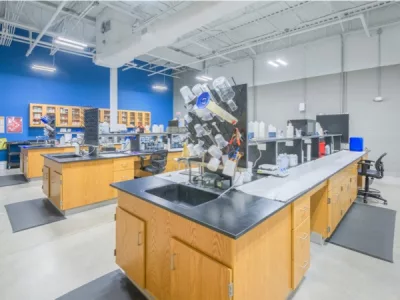
We’re a developer and supplier of chemistries for the metal finishing industry since 1948.
In PAVCO, we develop products and deliver services of the highest quality at a reasonable cost.