Galvanized or Electroplated Zinc: Which is Better for Industrial Applications?
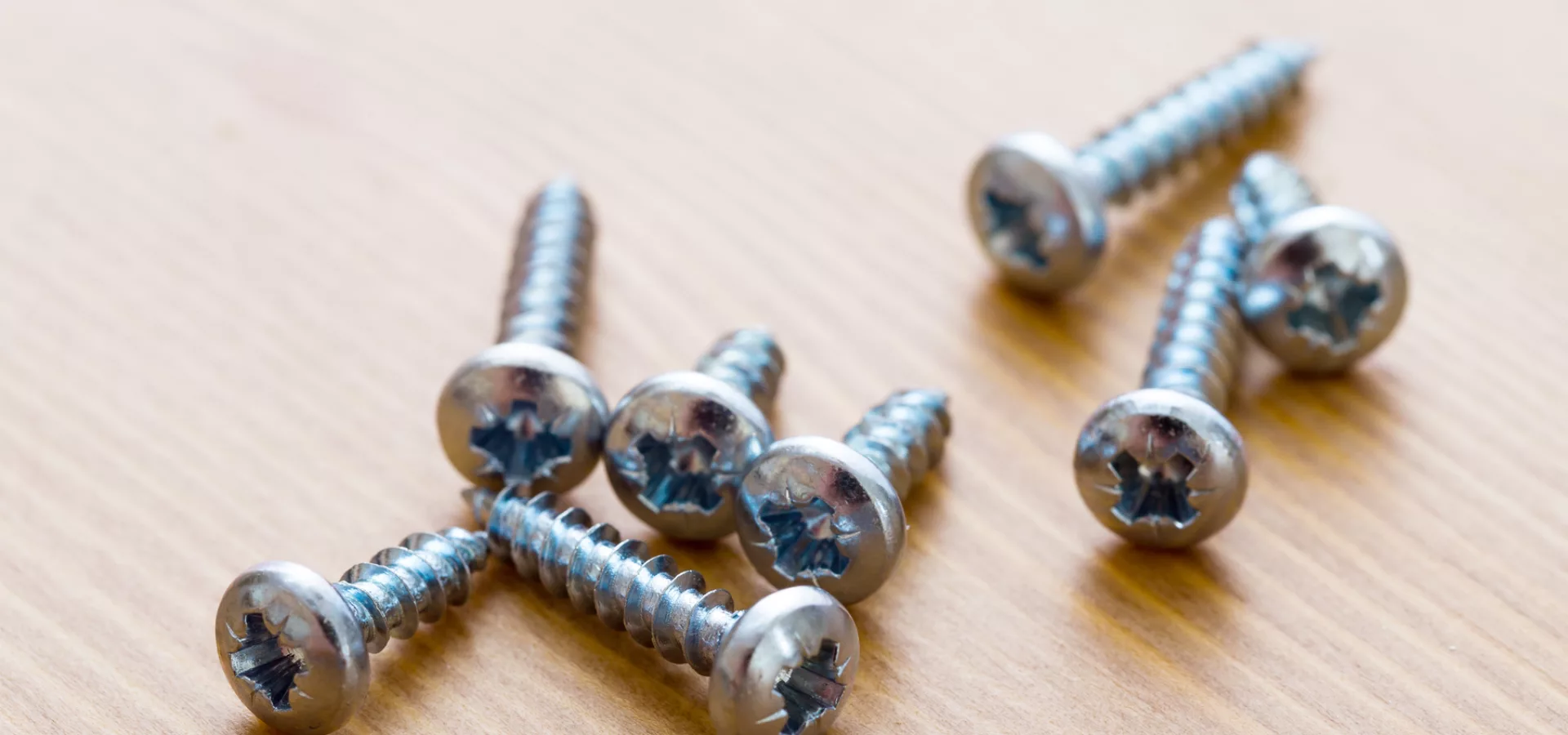
May 09, 2023
May 09, 2023
Two popular methods for protecting metals from corrosion and wear are hot-dip galvanizing and electroplating. Both processes involve coating the metal with another material to create a barrier against corrosion.
Still, there are differences in how they work and their suitability for different applications. In this article, we'll look at galvanized and electroplated coatings to help you decide which is better for your industrial needs.
What is Galvanization?
Galvanization is a process of coating steel or iron with zinc to protect it from rust and corrosion. The zinc forms a sacrificial layer that corrodes before the underlying metal does. Galvanized coatings can be applied in several ways, including hot-dip galvanizing, mechanical plating, and sherardizing.
Hot-dip galvanizing is the most common method, where the metal is dipped into a bath of molten zinc. At the same time, electro-galvanizing involves passing an electric current through the metal and a zinc solution. Sherardizing is a high-temperature process that uses zinc dust to create a coating.
What is Zinc Electroplating?
Electroplating is the process of coating a metal with a thin layer of zinc using an electric current. The metal to be covered is immersed in a solution containing zinc ions in an alkaline or acidic electrolyte. An electric current is passed through the solution to deposit the metal onto the surface.
Electroplating is commonly used for decorative purposes, such as adding a layer of gold or silver to jewelry. It can protect the metal from corrosion or wear. An electric current is passed through the solution to deposit the metal onto the surface.
Galvanized vs. Electroplated Coatings
Galvanized coatings are generally thicker and more durable than electroplated coatings. They can provide long-term protection against rust and corrosion in harsh environments, making them ideal for industrial applications such as construction, agriculture, and transportation. Galvanized coatings are also more affordable than electroplated coatings, which can be a significant factor for large-scale projects.
Electroplated coatings, on the other hand, are thinner and more decorative. They can be applied to various metals and create multiple finishes, such as shiny, matte, or textured. Electroplating is also a precise process that can be used without dramatically changing product dimensions. Average coating thicknesses for electroplated zinc are 5 to 12 microns.
Which One is Better?
The choice between galvanized and electroplated coatings depends on the specific needs of your application. Galvanized coatings are the way to go if you require a durable, thick, long-lasting coating that can withstand harsh environments and provide reliable protection against base metal corrosion.
However, electroplating may be a better choice if you need a decorative or functional coating that can add value to your product. Equally important, post-plating technology such as trivalent passivates, and sealers/topcoats can dramatically increase the service life of an electroplated part. This multilayer approach keeps the zinc coating looking new for longer.
In conclusion, both galvanized, and electroplated coatings have advantages and disadvantages, and the choice between them depends on the specific needs of your application.
IT’S HOW YOU FINISH
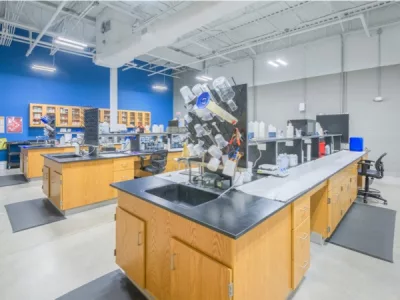
We’re a developer and supplier of chemistries for the metal finishing industry since 1948.
In PAVCO, we develop products and deliver services of the highest quality at a reasonable cost.