What Is a Soak Cleaner? A Key Step in Metal Pre-Treatment
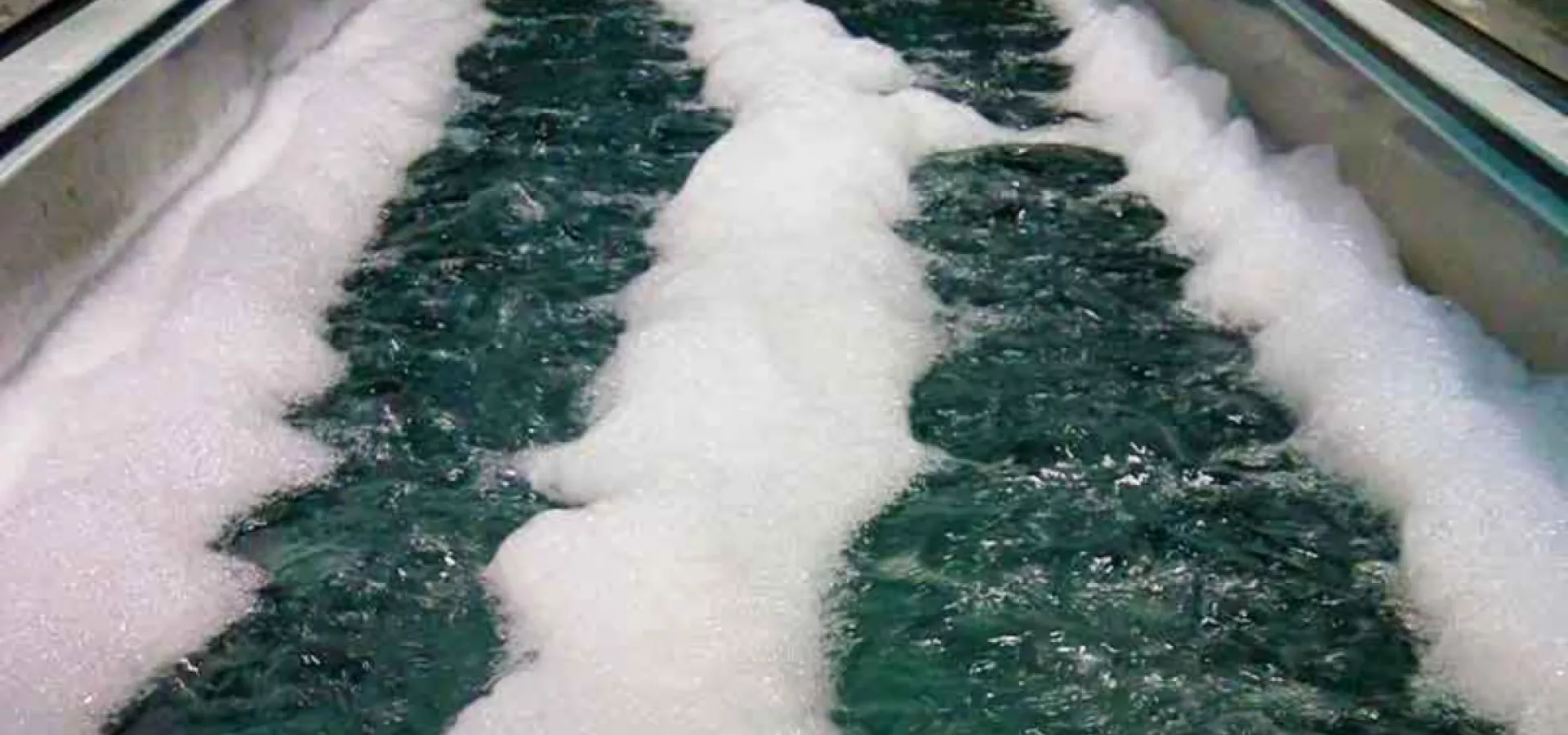
July 24, 2025
July 24, 2025
Metal finishing is a critical process in industries such as automotive, construction, electronics, and aerospace. A crucial yet often overlooked step in this process is soak cleaning, an essential pre-treatment phase that ensures metal surfaces are properly prepared for subsequent coatings or finishes.
In this blog, we’ll explore what soak cleaners are, how they work, their applications, and why they are indispensable in metal pre-treatment.
What Are Soak Cleaners?
Soak cleaners are chemical solutions designed to remove contaminants such as oils, greases, dirt, buffing compounds, and other residues from metal surfaces. A soak cleaner is a chemical solution that typically contains alkaline-based chemicals, detergent, and surfactants to effectively remove dirt, oils, grease, and contaminants from metal surfaces.
This cleaning process typically involves immersing metal parts in a tank filled with the soak cleaner solution. The solution works by breaking down and lifting contaminants from the surface, leaving it clean and ready for further processing.
Key Characteristics of Soak Cleaners
Versatility: Soak cleaners can be used on various metal substrates, including steel, aluminum, brass, copper, zinc alloys, and stainless steel.
Formulations: They are available in liquid or powder forms and can be emulsifying (holding soils in suspension) or rejecting/splitting (allowing oils to float for easy removal).
Environmental Considerations: Many modern soak cleaners are designed to be economical and environmentally friendly, reducing waste and VOC emissions.
How Do Soak Cleaners Work?
The soak cleaning process is straightforward yet highly effective. It involves the following steps:
Immersion: Metal parts are submerged in a tank containing the soak cleaner solution. Metals are submerged (soaked) in a heated cleaning solution, allowing the cleaner to dissolve and lift contaminants off the surface.
Chemical Action: The solution’s surfactants, builders, and other active ingredients break down oils, greases, and other contaminants. For instance, alkaline soak cleaners are particularly effective at removing organic soils like oils and fats.
Temperature and Time Control: The cleaning efficiency depends on maintaining the right temperature and immersion time. Mildly alkaline cleaners for soft metals often work at lower temperatures, while more aggressive formulations for steel substrates may require higher heat.
Rinsing: After cleaning, the parts are rinsed to remove any residual chemicals, ensuring a clean surface for subsequent processes.
Applications of Soak Cleaners
Soak cleaners play a pivotal role in various industries and applications:
Automotive Industry: Preparing components like engine parts, fasteners, and body panels for coatings or plating.
Electronics: Cleaning delicate components such as connectors and lead frames to ensure proper adhesion of finishes.
Construction: Treating architectural metals like aluminum and steel for durability and aesthetic appeal.
Sanitary and Decorative Finishing: Removing buffing compounds and oils from fixtures and fittings.
Benefits of Soak Cleaning
Enhanced Surface Preparation
Soak cleaning ensures that metal surfaces are free from contaminants, which is critical for achieving strong adhesion of subsequent coatings or finishes. As the saying goes, “Nothing gets plated until it gets cleaned”.
Improved Efficiency
Modern soak cleaners, such as PAVCO’s Clean-R solutions, are designed for efficiency and reliability. They reduce the need for rework, saving time and resources. They are also carefully formulated for compatibility with our electroplating processes.
Cost-Effectiveness
While some soak cleaners may have a higher initial cost, their superior cleaning performance and longer solution life make them more economical in the long run.
Proper soak cleaning ensures better adhesion and quality for subsequent treatments like electroplating, increasing the lifespan and durability of metal products.
Depending on the soils that need to be removed, it can be effective to consider a pre-soak stage where a rejecting or splitting cleaner can remove most of the oils while a second stage emulsifying cleaner can remove the rest. In this case, the first stage can be coupled with an oil separator and skimmer to increase its effective life.
Environmental Sustainability
Many soak cleaners are formulated to minimize environmental impact. For example, non-emulsifying cleaners allow for the separation and disposal of oils, reducing waste. Some of these oils can be repurposed. Surfactant technology and auxiliary equipment like ultrasonics have also decreased dependency on solvents or CFC (Chlorofluorocarbons)
Challenges and Best Practices
Common Challenges
Overloading the Cleaner: Excessive soil loading can reduce the effectiveness of the soak cleaner. Regular testing and maintenance are essential to ensure optimal performance.
Improper Temperature Control: Using temperatures that are too high or too low can compromise cleaning efficiency.
Neglecting Rinsing: Inadequate rinsing can leave residues that interfere with subsequent processes.
Best Practices
Monitor Soil Loading: Conduct soil load split tests to determine when the solution needs to be replaced or replenished.
Optimize Parameters: Maintain the recommended temperature, time, and concentration for the specific cleaner being used.
Use Pre-Rinses: A warm water pre-rinse can help remove water-emulsifiable soils, reducing the load on the soak cleaner.
PAVCO’s Commitment to Excellence
At PAVCO, we have been leading the way in metal finishing innovation for over 70 years. Our Clean-R™ solutions are a testament to our dedication to developing pre-plating technologies that are not only efficient and reliable, but also environmentally responsible.
Ready to optimize your cleaning and plating processes? Explore our full range of pre-treatment products and discover how PAVCO can support your operation.
Have questions or need a tailored solution? Talk to one of our experts today—we’re here to help you find the right approach for your specific application.
IT’S HOW YOU FINISH
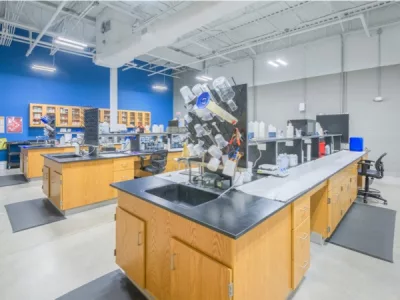
We’re a developer and supplier of chemistries for the metal finishing industry since 1948.
In PAVCO, we develop products and deliver services of the highest quality at a reasonable cost.