RoHS Compliance in Metal Coatings: What You Need to Know
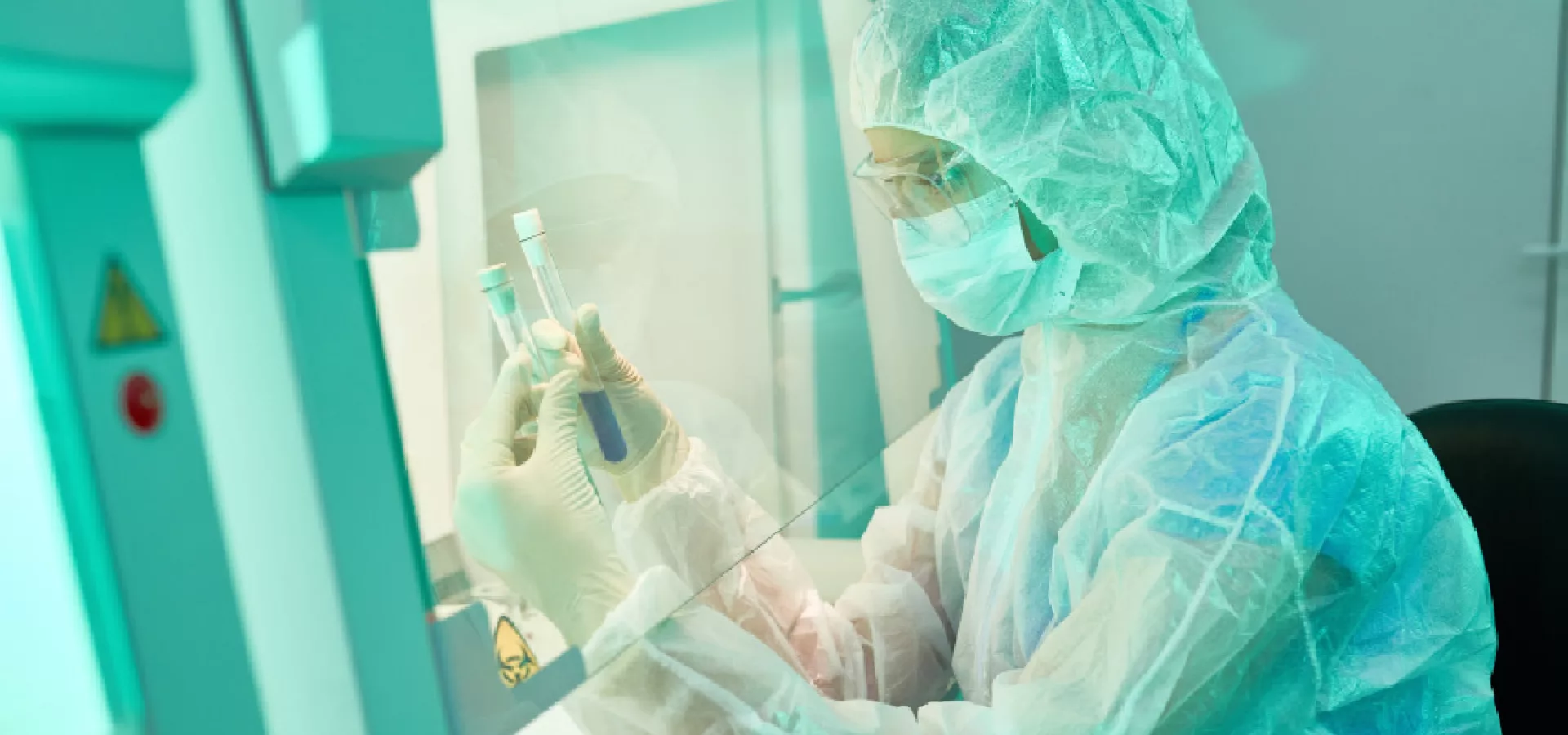
April 01, 2025
April 01, 2025
The Restriction of Hazardous Substances (RoHS) Directive has become a cornerstone in the global effort to reduce the environmental and health impacts of hazardous materials.
Initially introduced by the European Union in 2003, RoHS compliance has since evolved into a global standard, influencing industries ranging from automotive and aerospace to manufacturing and electronics.
In this blog post, we will explore the benefits of RoHS compliance in metal coatings, with a particular focus on its impact on the automotive, aerospace, and manufacturing sectors.
The Importance of RoHS Compliance in Metal Coatings
RoHS compliance in metal coatings ensures that products are free from hazardous substances, making them safer for both the environment and human health. Beyond regulatory adherence, it offers several key benefits:
Environmental Sustainability: RoHS-compliant coatings reduce the release of toxic substances into the environment, contributing to cleaner air, water, and soil.
Enhanced Product Safety: By eliminating harmful chemicals, these coatings minimize health risks for workers and end-users.
Global Market Access: Many countries and regions require RoHS compliance for imported goods, making it essential for businesses aiming to compete globally.
Improved Recycling and Waste Management: RoHS-compliant coatings facilitate the recycling of end-of-life products, reducing waste and conserving resources.
What Are the Key Requirements of RoHS Compliance?
RoHS compliance mandates that products do not exceed the allowable limits of specific hazardous substances. The directive restricts the use of six main substances, with additional categories added over time. The current maximum allowable concentrations are typically:
Lead (Pb): 0.1%
Mercury (Hg): 0.1%
Cadmium (Cd): 0.01%
Hexavalent Chromium (Cr6+): 0.1%
Polybrominated Biphenyls (PBB): 0.1%
Polybrominated Diphenyl Ethers (PBDE): 0.1%
These limits apply to homogeneous materials, meaning every material layer in a component must meet the requirements. Manufacturers must also implement robust documentation and testing protocols to ensure compliance.
What Do Common RoHS-Compliant Coatings Include?
Many metal coatings have been developed to meet RoHS requirements while maintaining performance standards. Common RoHS-compliant coatings include:
Trivalent Chromium Passivates: An alternative to hexavalent chromium, offering excellent corrosion resistance and environmental compliance.
Electroless Nickel Coatings: Often used in electronics, these coatings provide uniform coverage and enhanced durability and can be formulated without heavy metals to avoid exceeding RoHS limits.
Zinc-Nickel Alloy Coatings: Widely used in the automotive and aerospace industries, these coatings offer superior corrosion resistance while being free of restricted substances.
Lead-Free Solder Coatings: Used in electronics, these coatings help meet RoHS requirements without compromising electrical conductivity.
What Are the Main Challenges in Achieving RoHS Compliance for Metal Coatings?
While RoHS compliance offers numerous benefits, achieving it can present challenges for businesses:
Cost of Transition: Switching to RoHS-compliant materials and processes often requires significant upfront investment, including new equipment and staff training.
Technical Challenges: Developing coatings that match or exceed the performance of non-compliant alternatives can be complex and time-consuming.
Testing and Certification: Regular testing is necessary to ensure compliance, which can be costly and labor-intensive.
Supply Chain Management: Ensuring that all suppliers and materials meet RoHS requirements requires meticulous oversight and communication.
Global Variations: Different regions may have additional or updated regulations that require businesses to adapt their processes continually.
By understanding and addressing these challenges, businesses can unlock the full potential of RoHS compliance and position themselves as leaders in sustainability and innovation.
Partner with PAVCO for RoHS Excellence
For over 75 years, PAVCO has been a trusted partner in the metal finishing industry, delivering groundbreaking solutions that combine sustainability with superior performance.
With our cutting-edge technologies, you can embrace RoHS compliance as a strategic advantage—improving sustainability, enhancing product quality, and gaining access to global markets without compromise.
Ready to Transform Your Coatings?
RoHS compliance isn’t just a regulation; it’s a pathway to innovation and growth. With PAVCO’s expertise, your business can lead the way in creating a cleaner, safer, and more competitive future. Let’s shape the future of metal coatings—together.
Got a question? Contact us today to solve it.
IT’S HOW YOU FINISH
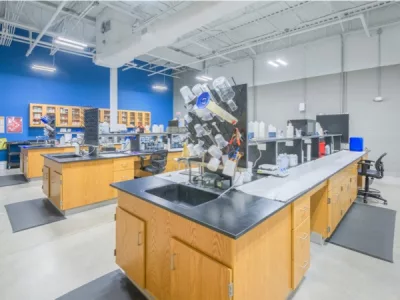
We’re a developer and supplier of chemistries for the metal finishing industry since 1948.
In PAVCO, we develop products and deliver services of the highest quality at a reasonable cost.