Minimize Replating Costs: How to Remove Zinc Plating Correctly
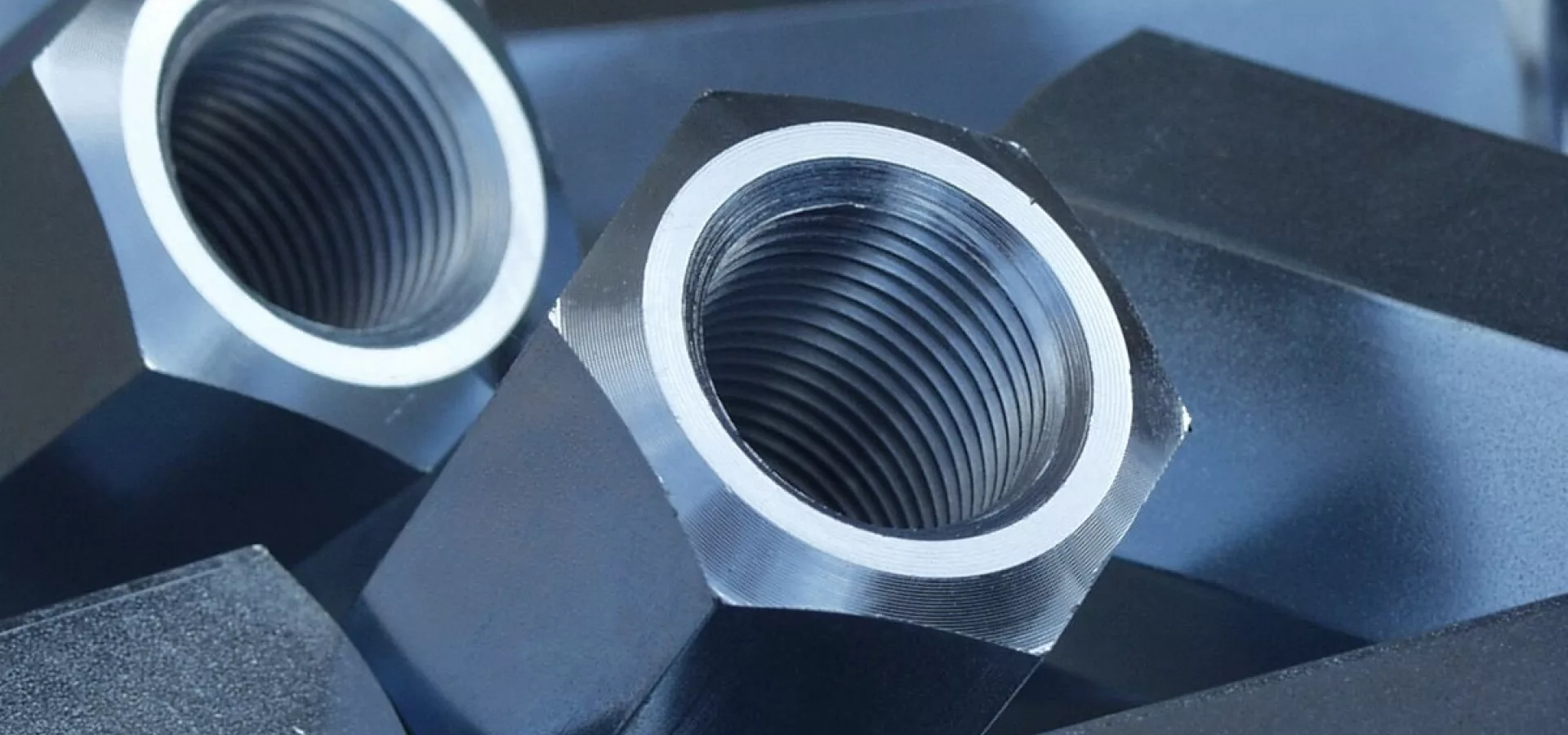
October 08, 2024
October 08, 2024
In any manufacturing process involving metal plating, the production of defective parts is an inevitable challenge. Whether due to inconsistent coating, contamination, or other unforeseen issues, some components will require rework to meet quality standards. In zinc plating, this reality can be especially costly, as defective plating must be removed before a component can be replated.
Understanding how to remove zinc plating correctly can help manufacturers minimize these costs by salvaging defective parts without damaging the underlying substrate or incurring unnecessary expenses. This article outlines the key methods for removing zinc plating, the factors influencing their selection, and how to prepare parts for replating.
Understanding the Zinc Plating Removal Process
Reworking defective parts requires more care and precision than plating new, virgin components. The zinc plating must be removed thoroughly without damaging the underlying raw substrate, which could compromise the part’s structural integrity or cause issues during the replating process.
Before selecting a method to remove zinc plating, several factors must be considered:
Type of base substrate: The material beneath the zinc plating will influence the method of removal, as some techniques can damage sensitive materials.
Stripping method: The method chosen must be technically viable for the type of part and commercially viable in terms of cost and scalability.
Let’s explore the most common zinc removal methods, their advantages, disadvantages, and best use cases.
You may be interested in our zinc plating systems. Get to know them here.
Chemical Stripping Methods
Chemical stripping is one of the most commonly used methods for removing zinc plating. It involves immersing the part in a chemical solution that dissolves the zinc coating while leaving the underlying material intact. Chemical strippers can be broadly categorized into alkaline and acidic solutions.
Alkaline Strippers
Alkaline strippers, such as sodium hydroxide or sodium bicarbonate, are often preferred for their gentle approach. These solutions dissolve zinc without attacking the base substrate, making them a safer option for parts with delicate or sensitive materials.
Safe for base substrates: Alkaline strippers are less likely to damage the underlying material, making them ideal for parts with complex or sensitive substrates.
Selective removal: These solutions can be formulated to target only the zinc coating, leaving other layers intact if necessary.
More expensive: Alkaline solutions tend to be pricier than acidic alternatives, which can increase costs, particularly for large-scale operations.
Waste treatment challenges: The spent solution and rinse water from alkaline stripping solutions can be more challenging to treat and dispose of compared to acidic solutions.
Acidic Strippers
Acidic strippers, such as hydrochloric acid, acetic acid, and acid salts like bisulfate or ammonium chloride, are another popular option for zinc removal. These solutions tend to work faster and are more cost-effective than alkaline strippers, making them ideal for high-volume production environments.
Cost-effective: Acidic strippers are generally cheaper than their alkaline counterparts, which can help minimize replating costs in high-volume applications.
Fast-acting: Acid solutions work quickly to dissolve zinc, reducing overall rework time.
Efficient waste treatment: The waste generated from acidic strippers is typically easier to treat, simplifying compliance with environmental regulations.
Substrate damage: Acidic solutions can attack the base material, especially if the substrate is sensitive to corrosion or etching. Inhibited formulations can reduce this risk but require stricter process control.
Tighter control needed: Due to the aggressive nature of acidic strippers, process parameters must be tightly controlled to prevent over-etching or damage to the substrate.
Mechanical and Electrolytic Methods
While chemical stripping is the most common approach, mechanical and electrolytic methods also offer viable alternatives for zinc removal, particularly in specific applications.
Mechanical Removal (Sanding or Grinding)
Mechanical methods, such as sanding or grinding, involve using sandpaper, abrasive tools, or grinding wheels to physically remove the zinc layer. These methods are simple and inexpensive but come with significant drawbacks.
Low cost: Mechanical methods require minimal equipment and materials, making them one of the cheapest options for zinc removal.
Labor-intensive: Sanding or grinding can be time-consuming and physically demanding, particularly for complex or large parts.
Inconsistent finish: This method often results in a rough surface, which may not be ideal for parts that require a smooth finish before replating.
Electrolytic Stripping
Electrolytic stripping involves using an electrolytic solution to remove the zinc coating. This process is typically more suitable for larger parts and can be highly cost-effective in large-scale operations.
Efficient for large parts: Electrolytic stripping can process large parts quickly and uniformly, making it ideal for components that would be difficult to strip mechanically or chemically.
Cost-effective for large volumes: In high-volume applications, electrolytic stripping can be a more economical option than chemical methods.
Requires specialized equipment: Electrolytic stripping demands a more complex setup, including an electrical power supply and electrolytic solution, which may not be feasible for all operations.
Wire Brushing
Wire brushing is another mechanical method where a wire brush is used to scrub away the zinc coating. This technique is simple and cost-effective but may not be suitable for parts requiring a more delicate approach.
Cheap: Like sanding and grinding, wire brushing is a low-cost option for zinc removal.
Not suitable for all parts: Wire brushing may not be appropriate for intricate or delicate components that require a more refined finish.
Preparing Stripped Parts for Replating
Once the zinc plating has been successfully removed, it is crucial to properly prepare the part for the replating process. This preparation includes cleaning the part, activating the surface, and ensuring that the component is free of contaminants or oxidation.
Cleaning
After stripping, the part must be thoroughly cleaned to remove any remaining contaminants, including oils, dirt, or residues from the stripping solution. This step is essential to ensure that the new plating adheres properly to the surface.
Surface Activation
Surface activation involves removing any oxidation or residues that may have formed during the cleaning process. This can be achieved using chemical treatments or mechanical methods, depending on the part's material and the specific requirements of the plating process.
Final Plating Cycle
With the part cleaned and activated, it is ready for the final plating cycle. This involves depositing the required metal layers to achieve the desired finish. Ensuring that the part is properly prepared before replating is critical to achieving a high-quality, durable finish.
Want a perfect finish?
Removing zinc plating correctly not only minimizes rework costs but also ensures that your parts are ready for a high-quality finish.
Whether you choose chemical, mechanical, or electrolytic methods, it’s crucial to follow the right process for cleaning and surface activation to prepare parts for replating. At PAVCO, we offer a range of specialized cleaners and zinc plating systems that guarantee top performance and consistent results in your metal finishing operations. By using our cutting-edge solutions, you’ll ensure a flawless, durable finish every time.
Ready to enhance your plating process? Explore our solutions today.
IT’S HOW YOU FINISH
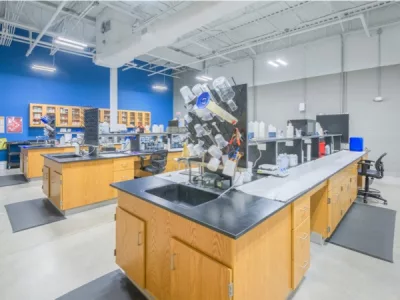
We’re a developer and supplier of chemistries for the metal finishing industry since 1948.
In PAVCO, we develop products and deliver services of the highest quality at a reasonable cost.