Heating Requirements in Metal Finishing Processes
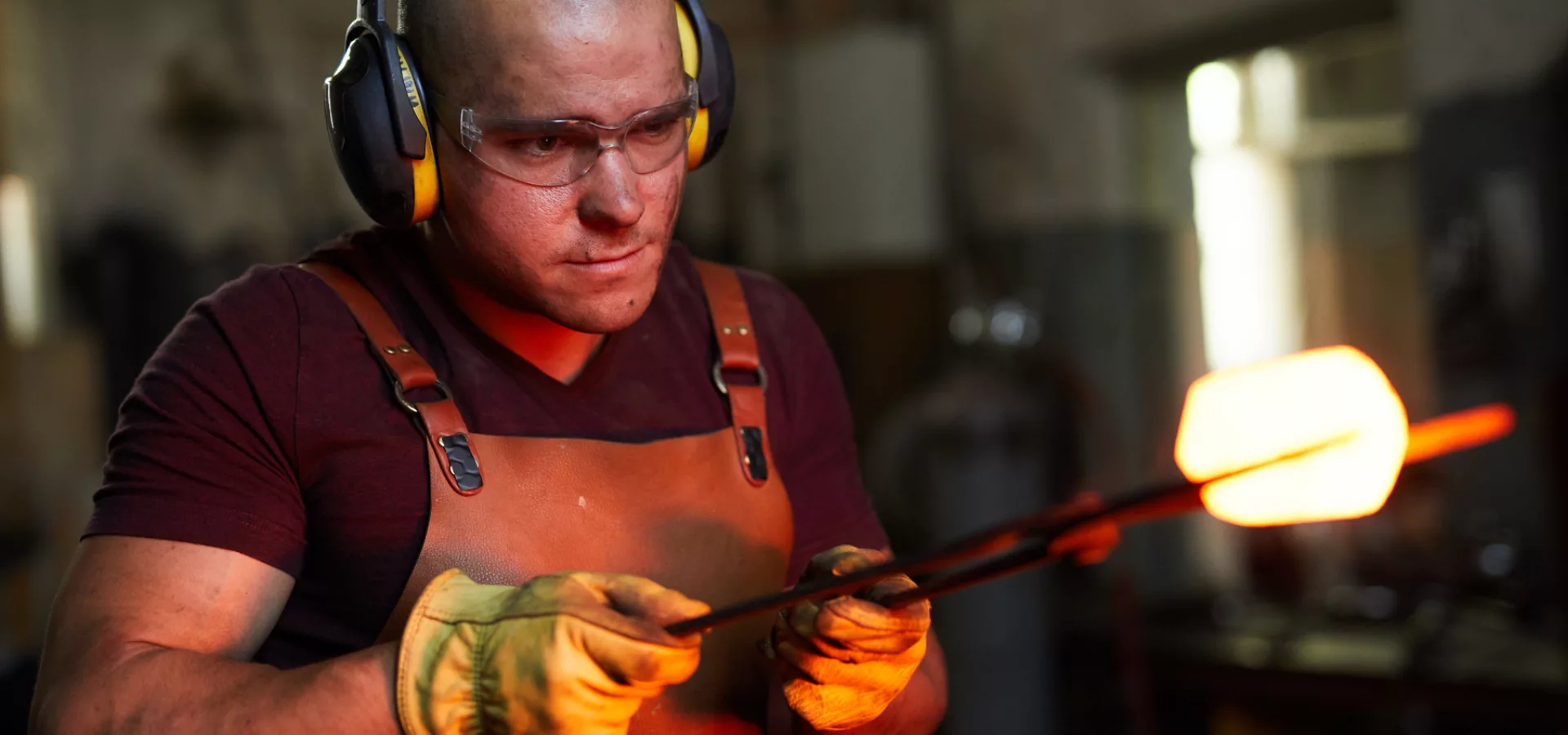
April 19, 2023
April 19, 2023
The metal finishing industry is complex, especially when dealing with certain types of metals, where success depends on controlling multiple variables. One key variable is temperature.
Temperature is critical in achieving a high-quality surface treatment in metal finishing. Controlling other conditions such as concentration, pH, time, and current density is also crucial.
At PAVCO, we develop chemicals for finishing with the highest quality and have different solutions for your surface finishing needs. Explore our pre-plating solutions, plating technologies, and post-plate solutions.
Processes where temperature makes the difference
Processes where temperature is critical include cleaners, bright dipping baths, chemical polishes, plating baths, electroless nickel, phosphates, chrome plating, and conversion coatings.
Some processes require heating but offer a broader range of operating temperatures. We must consider whether we are economically maximizing the required temperature for a successful surface treatment. Higher energy usage can significantly raise the cost of a cycle stage, sometimes with marginal benefits.
To find optimum cost savings while still providing a quality finish, it is crucial to have the best quality metal finishing chemical supplier who can collaborate with you to find these savings.
The impact of metal finishing deficiencies
Rejects due to defects can significantly affect budgets assigned to jobs and ultimately decrease profit margins. Reprocessed parts often have lower chances of meeting approval requirements. Temperature is one crucial parameter that requires no significant effort and, most times, only a specified range.
PAVCO offers a wide range of chemical developments that help the metal finishing industry create the ideal coat for various highly-complex applications.
Good practices to achieve the ideal surface finish
Controlling the temperature helps determine the heat used and how much is leaving the system. An operating temperature range allows for quality surface treatment in line with the maintenance of other complementary conditions. Processes like these contribute to cost savings. Companies can achieve savings through pre-programmed thermostats or by covering the tank when unused. Insulation can also reduce the heat escaping from temperature controlled tanks, leading to additional savings in reduced heating costs.
There are various plating systems that produce better results at low temperatures. Think traditional chloride and alkaline zinc. The ideal temperatures for these systems are often below ambient temperature and, thus, require cooling. A plating shop might also require other processes to operate at even lower temperatures.
Alkaline Zinc Nickel, Anodizing, Bright Tin are some other examples. Interestingly, plating technology in chloride and alkaline zinc can eliminate the need for cooling these baths and focus chiller capacity to more critical processes. Furthermore, chloride and alkaline systems can benefit from operating at high temperatures. Pavco’s Smart Zinc, Merlin, and Blaze systems can tackle this task.
Energy is expensive, and anything we can do to offset these costs can help the bottom line. At PAVCO, we strive to provide the best quality metal finishing chemicals while satisfying our customers to save costs.
IT’S HOW YOU FINISH
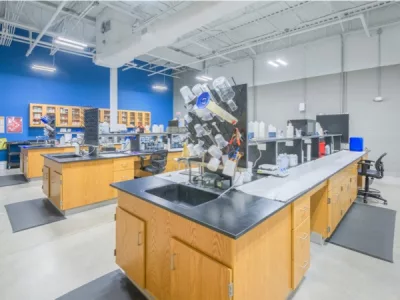
We’re a developer and supplier of chemistries for the metal finishing industry since 1948.
In PAVCO, we develop products and deliver services of the highest quality at a reasonable cost.