Addressing problems with Carbon Treatment for Nickel tanks
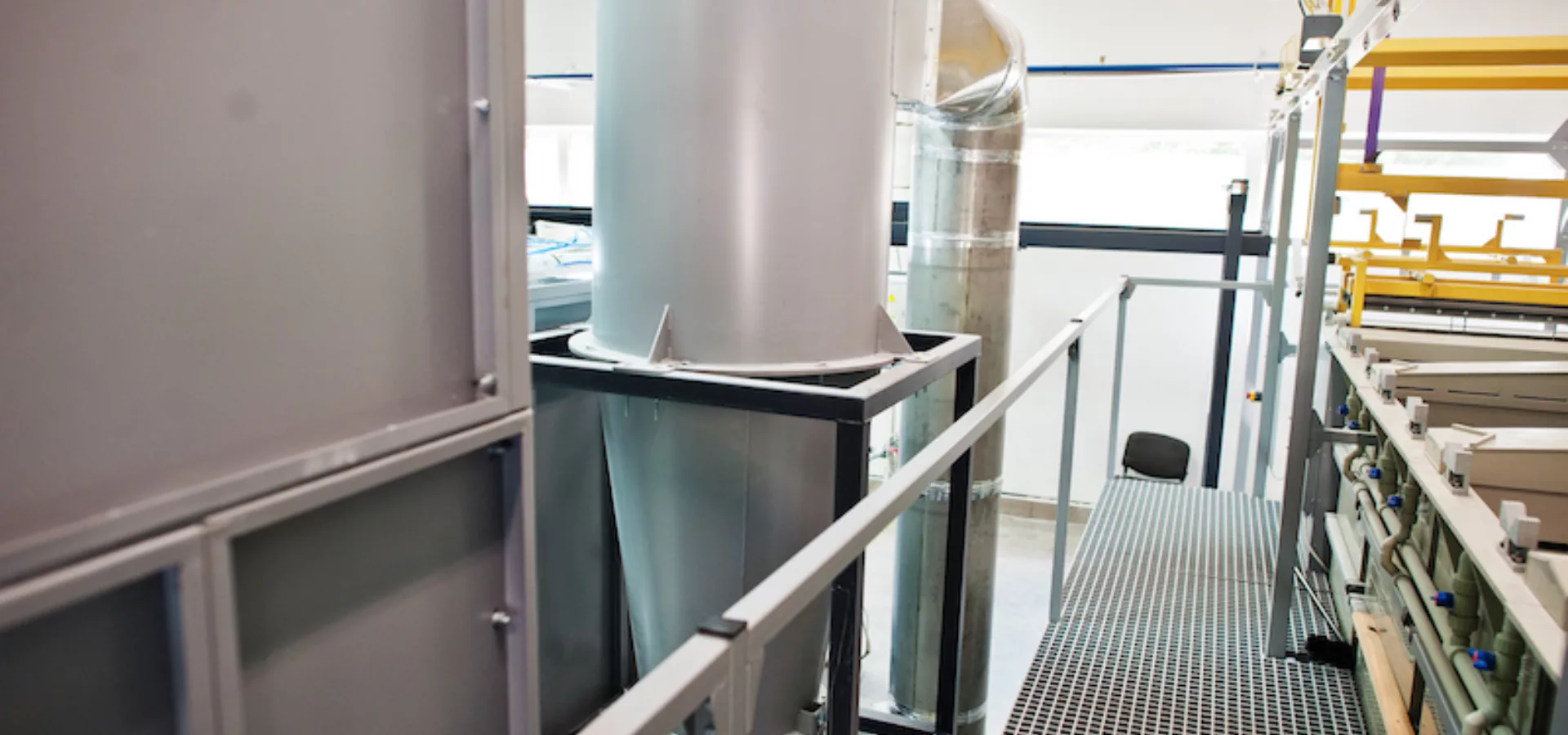
June 05, 2022
June 05, 2022
First, we should discuss the “why” behind doing a carbon treatment on a nickel tank. Nickel baths will build up with organics from multiple sources. Those include good organics from your carrier and brightener package.
Plus, bad organics from electrolysis (breakdown products of the good organics), bad organics from drag in from previous tanks on the line, and finally from soils/oils/greases/buffing compounds that are not always removed during the cleaning process.
As the organic load in the bath increases, you can see detrimental effects to the deposit characteristics like increases in stress and reduction of ductility. You can also start to see visual defects on the work such as hazing in the MCD-LCD areas, and organic pitting.
Because of these negative effects, regular carbon polishes, treatments, and maintenance should be done on the bath to ensure that you are producing a quality finish. Many platers will track the total organic carbon (TOC) in their nickel baths to determine when they need to be treated, while others will schedule the treatments at the same time every year.
The results of using carbon treatment for nickel tanks
When doing these treatments most platers take the time to do other maintenance on their tanks like removing sludge from the bottoms of the anode baskets and replacing anode bags due to iron (Fe) buildup or rips/tears.
Based on what we know about the defects looking like small lines/cracks or even described as “hairs” or “fibers” in the deposit, a common source of the problem is anode fines from the nickel sludge or fibers from the anode bags.
The best practice for removing anode fines is to remove the baskets from the plating tank to an offline position, remove the anode bags and then pressure wash the basket to remove the fines. This way you eliminate the possibility of spraying fines into the tank.
Also if the anode bags are not treated properly before putting them on the baskets, they can then release fines or “sizing” into the bath. The best practice for new anodes bags is to wash them using a slightly alkaline solution (like 10% sodium carbonate).
Then rinse the bags with water before soaking them for 8-24 hours in a 1% sulfuric acid solution with 0.1% nickel wetting agent. This will clean the bags of any potential organic contaminants that you can get from the sewing process of the bags and remove any loose sizing from the bags.
To evaluate this hypothesis, you can take two gallons of the plating solution and vacuum filter it in the lab with one gallon being filtered through a white filter paper and the other gallon through black.
By filtering this way, you can see if you have any particulates in the bath that could be co-depositing with the nickel creating this roughness. The white paper will show you particulates like carbon or dirt, while the black paper can show you filter aid or the sizing material from the white anode bags. You can also send a part showing the defect to your chemical supplier for defect analysis to help you get a better understanding of what is happening.
The real solution for carbon treatment
Unfortunately, if you do have particulates from any source (anode bag fibers, carbon/filter aid, anode fines, etc.) then you are at the mercy of your filtration system to remove them. If you need the production and can handle the current scrap rate, then letting your filtration run and continuing to plate will allow you to eventually “walk out” of the problem.
How quickly it corrects itself will depend on the amount of particulates in the bath, the speed of your filtration (bath turnovers per hour), and the layout/design of your filtration system. If you are running critical parts and cannot afford the increased scrap rate, the best course of action would be to pump the entire tank out to storage through your filter and then clean/inspect the entire tank including checking the anode bags for rips/tears.
Then change the filter pack and pump the solution back to the plating tank through the filter. This way the entire plating bath gets filtered twice and therefore any particulates should be removed.
Josh Fish
Technical Service/Lab Operations Director
IT’S HOW YOU FINISH
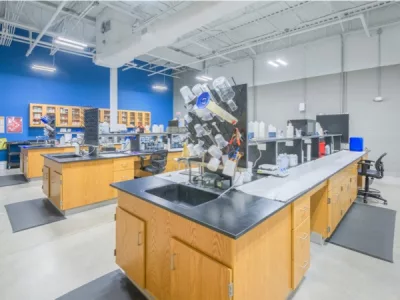
We’re a developer and supplier of chemistries for the metal finishing industry since 1948.
In PAVCO, we develop products and deliver services of the highest quality at a reasonable cost.