Plating Cast Iron for Industrial Applications
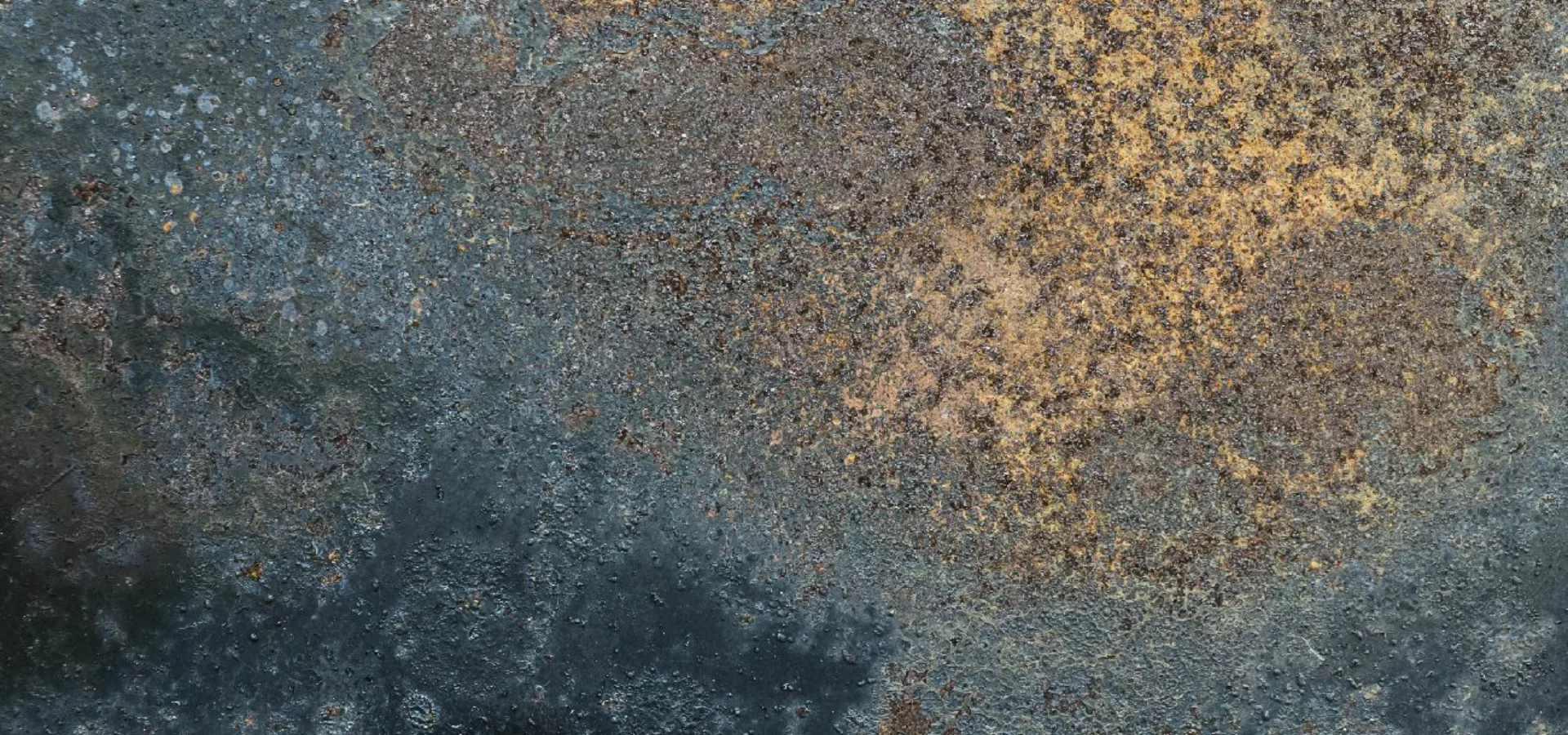
March 21, 2024
March 21, 2024
Cast iron, with its exceptional strength, wear resistance, and affordability, is a popular material choice for various industrial applications. However, electroplating cast iron presents unique challenges compared to other materials.
This blog post dives deep into the process, highlighting the importance of pre-treatment, addressing common challenges, and exploring solutions for achieving optimal plating results.
Why plating cast iron?
Although cast iron possesses inherent strength, its susceptibility to corrosion requires additional protection in specific environments. Plating cast iron offers several advantages:
Enhanced corrosion resistance: Plating creates a barrier against corrosive elements, extending the lifespan of cast iron components.
Improved wear resistance: Certain plating materials offer superior wear resistance, crucial for components under constant friction.
Aesthetic appeal: Plating can enhance the visual appearance of cast iron parts, particularly for decorative applications.
Pre-Treatment: The crucial first step
Pre-treatment is fundamental for successful plating of cast iron. Cast iron's porous nature and sensitivity to strong acids require a meticulous approach to ensure optimal adhesion and a smooth plating finish. Here's what you need to consider:
Mild Acid Pickling: Opt for mild acid pickling solutions. This effective solution removes surface contaminants without compromising the integrity of the cast iron.
Inhibitor Use: Always use inhibitors alongside mild acid pickling solutions. PAVCO inhibitors minimize hydrogen embrittlement, and reduce iron dissolution, further protecting the cast iron substrate.
Ultrasonic Cleaning: This technique employs sound waves to dislodge deeply embedded contaminants like sand residue and surface carbon, ensuring a clean surface for plating.
Remember: Strong acids should be avoided due to their tendency to increase porosity, resulting in rough and aesthetically unpleasing plating layers. Additionally, the higher sensitivity of cast iron to strong acids makes stripping and replating more difficult. Discuss with a Pavco representative for best methods of stripping and replating cast iron parts.
Overcoming challenges in plating cast iron
Plating cast iron can be intricate, demanding careful process optimization to achieve desired results. Let's explore some common challenges and potential solutions:
Dull Appearances: Recessed areas of cast iron parts often exhibit a dull plating finish. To address this, consider using Smart Zinc Premier or NiClipse C plating baths. These baths are formulated to achieve uniform brightness across the entire surface of the parts, eliminating the issue of dull spots.
Throwing Power: This refers to a plating bath's ability to deposit the plating material uniformly across the entire surface, even in recessed areas. Cast iron parts like brake calipers require a plating bath with high throwing power to ensure adequate coverage and, consequently, effective corrosion protection in recessed areas.
Burning: High current density regions, common in complex geometry cast iron components, are susceptible to burning during the plating process. This burning manifests as discolored or rough patches on the plated surface. Bath optimization is crucial to prevent burning in these high current density regions.
Choosing the right plating solution
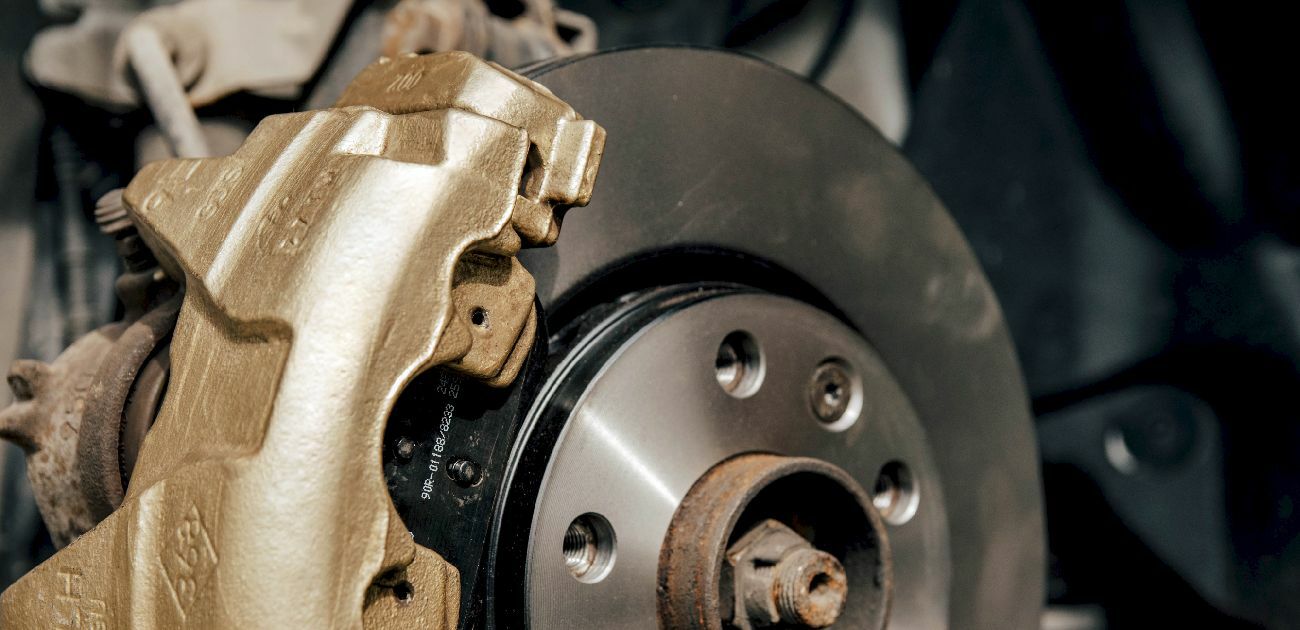
Unlocking the full potential of your cast iron components requires a strategic approach to plating. Several crucial factors influence the selection process:
Desired metal finish: What aesthetics and functionalities are you aiming for? Consider the impact on visual appeal, conductivity, or other desired properties.
Substrate material: Cast iron's unique properties demand compatible plating options. Understanding its characteristics is essential for optimal adhesion and performance.
Application requirements: What specific demands does your cast iron component face? Does it require enhanced corrosion resistance, wear resistance, or specific aesthetic qualities?
PAVCO's cast iron plating solutions
Acid Zinc: Cost-effective, reliable, and versatile for conductivity improvement.
Acid Zinc-Nickel: Unbeatable strength and corrosion resistance for extreme applications.
Beyond Plating: Protecting and enhancing your cast iron
Post-plating treatments act as the final layer of defense and beautification:
Cobalt-free Trivalent Passivates: These eco-friendly options offer an additional layer of corrosion resistance specifically designed for cast iron, without compromising environmental responsibility.
Trivalent Passivates: Provide a robust protective layer, significantly boosting the durability and visual appeal of your cast iron component.
Black Trivalent Passivates: This option combines enhanced protection against wear, abrasion, or chemicals with a sleek black finish, ideal for applications requiring both functionality and aesthetics.
Sealers/Topcoats: Specialized coatings designed for optimal performance on cast iron, these treatments further enhance the appearance and durability of the surface.
By meticulously selecting the right plating and post-plating solutions, you can significantly extend the lifespan, improve the performance, and elevate the aesthetics of your cast iron components.
IT’S HOW YOU FINISH
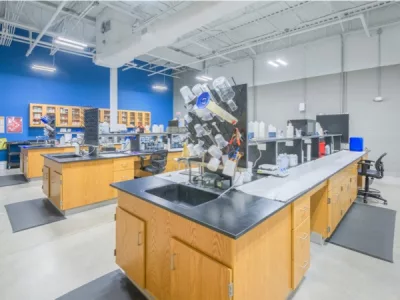
We’re a developer and supplier of chemistries for the metal finishing industry since 1948.
In PAVCO, we develop products and deliver services of the highest quality at a reasonable cost.